PlaSTEAMed - Reimagine Recycling
Plastic isn’t the problem. The way we regard plastic is the problem. Everybody loves to recycle but nobody understands how it actually works. The centralised model of recycling with very large capital investments has significant logistics, sorting and cleanliness issues.
We are developing a distributed technology platform that uses plastic recycling to generate habit change through STEAM education.
We deliver a suite of equipment that has been specially designed to operate safely in schools. We also provide access to matching K-12 curriculum and complete training, operating and certification systems. Children bring their PET and HDPE bottles to school and learn how to make things from plastic. The excess is sold into the commercial market to generate revenue to pay for the equipment.
When scaled globally we will re-purpose 3 to 4 Mega Tonnes of plastic each year.
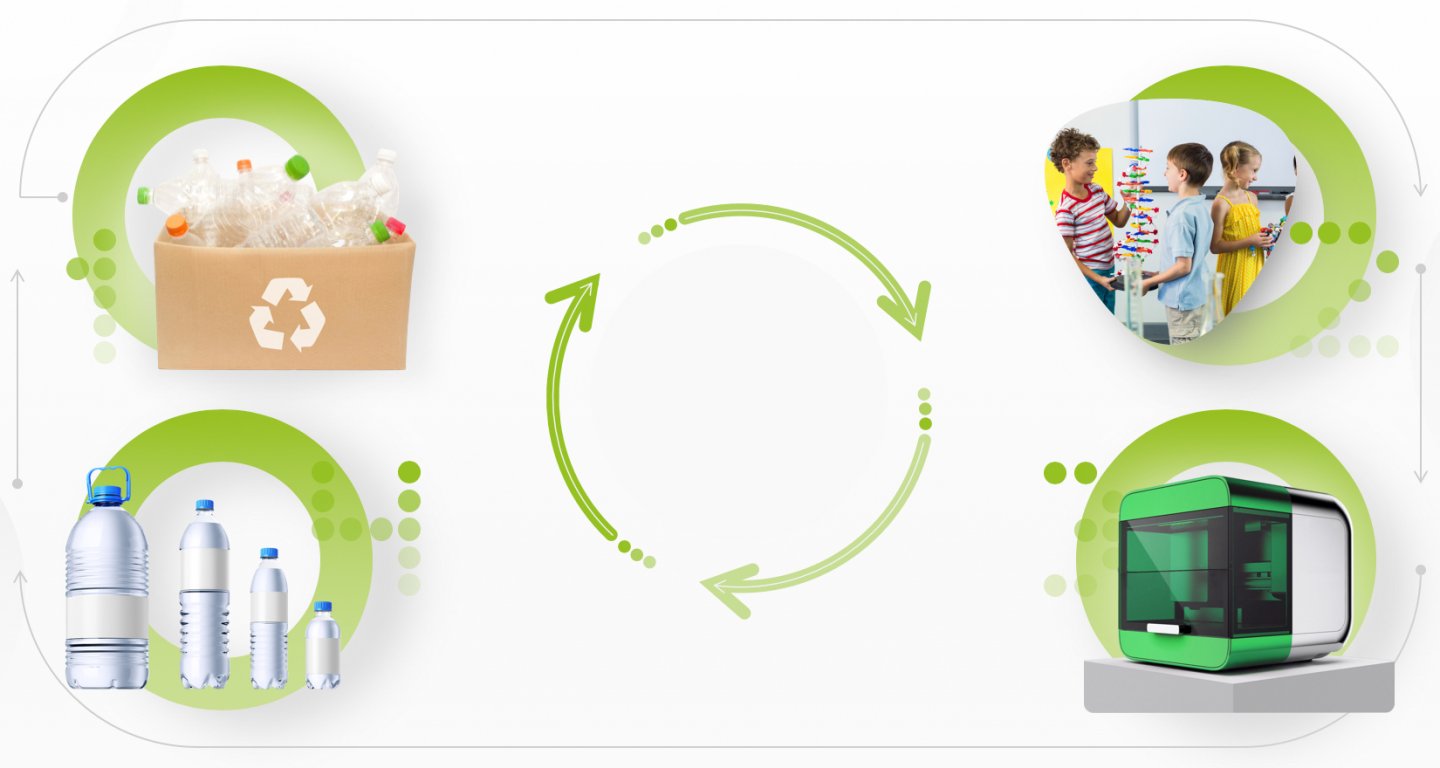
Initially we are addressing the plastic waste problem in Australia. Australia uses around 370kT/year of plastic packaging - the majority of which is PET and HDPE. In 2015 125kT of PET+HDPE were recycled however most of this was sent offshore. China, India and Malaysia have all stopped importing contaminated plastic waste. Australia imports rPET to meet local demand. At scale we will recycle 35kT of PET+HDPE in Australia. Our output will be uncontaminated, colour sorted and shredded.
We are also looking at the issue of plastic waste reaching the ocean in Pacific Island countries. Islands have a unique problem in that they have limited scope for landfill, high energy costs and plastic waste is impacting their primary source of revenue - tourism. We are scaling the business model to provide a combined education and commercial solution specifically for island communities.
Globally the recycled plastic market is worth around US$35B p.a. and is forecast to grow at 6.5% CAGR for the next 7 years. Companies such as Coca Cola have committed to achieving 50% rPET in their packaging by 2030. There is a huge opportunity for local communities/schools in every country to participate in this growing sector.
The key people we are working with are educators, education innovators and school children. During the design phase we are working primarily with the educators at a specific local learning precinct (network of government schools).
The specific configuration and layout of the equipment is being designed to enable:
- Simple workflow from sorting to shredding to making.
- High degree of visibility of the processes to maximise interest and engagement from the students.
- Robust safety and hygiene.
- Optimum footprint to enable space constrained schools to participate.
The curriculum is being developed with the educators to ensure it is aligned with state requirements and maximises the use of the installed equipment to ensure tacit knowledge to back up the theory.
The logistics tracking system is being developed to enable complete transparency for every container of shredded plastic. Every container is uniquely coded and traceable at every stage right through to the final customer.
We have had a very high level of interest from educators as we provide the capability to move education from theoretical knowledge to tacit knowledge.
Big Idea
Children bring their plastic to school and learn about plastic and recycling.
We place specialised equipment into the schools for shredding plastic and making things from this resource. This is backed up by dedicated Science, Technology, Engineering, Art and Maths (STEAM) curriculum.
As the students progress through school they learn how to make things from recycled plastic. In their final years at school they combine everything they've learned to work as a team to either solve a problem or generate an innovative business idea.
The excess plastic that the schools don’t use is sold into the commercial recycling market. The sales of shredded plastic are used to pay down the capital cost of the equipment over time. There is no up front capital cost for the school.
How It Works
We deliver a suite of equipment that has been designed and validated to operate safely in schools. The equipment consists of recycling machines plus simple extrusion, injection and compression moulding machines for making products. It’s effectively a tiny micro-manufacturing plant. Along with the equipment we provide access to a matching K-12 curriculum in the areas of Science, Technology, Engineering, Art and Mathematics (STEAM). The complete operating, training and safety certification system is also provided.
Children bring their plastic to school and learn about plastic and recycling.
We place specialised equipment into the schools for shredding plastic and making things from this resource.
As the students progress through school they learn how to make things from recycled plastic.
The excess plastic that the schools don’t use is sold into the commercial recycling market.
Data, AI and Product Packaging Design Feedback Loop
Every container that goes through the shredding process is imaged and scanned using near infra-red. We will be investigating the opportunity to use AI analysis of the scan data to eject containers that require additional cleaning.
Some containers are much easier to prepare for recycling than others. We will be providing detailed statistically significant data to manufacturers and retailers. We will also be encouraging product purchase decisions for each family based on the ease of recycling the packaging. There will be direct commercial feedback to retailers and manufacturers.
- Increase production of renewable and recyclable raw materials for products and packaging
- Demonstrate business models for extending the lifetime of products
- Prototype
- New business model or process
The entire recycling paradigm is based on traditional large scale industrial thinking. Recycling is something that happens in some mysterious dirty factory somewhere. This paradigm both disconnects us from problem and constrains our thinking around potential solutions.
The current recycling business model creates a problem by commingling materials. It is also very inefficient as it involves shipping around large volumes of air.
By shifting the paradigm to distributed local ownership of part of the recycling process we are able to generate an entirely new and commercially viable business model. A model that engages the local community, drives generational habit change, brings money into the local community and seeds future innovative thinking amongst an entire generation.
Our model never commingles plastic streams and minimises logistics costs by massively reducing the volume of material being handled which enables us utilise existing logistics networks. Networks that are typically returning to a central location with no load.
We are rescaling and repurposing existing technology to enable a completely new business model.
The key technology elements of our solution are:
- Individual sorting of containers through the education program backed up by scanning of individual containers. We will also be exploring the ability to use AI to validate the cleanliness of individual containers.
- Micromanufacturing sized shredding, injection moulding, compression moulding and extrusion machines.
- Reverse application of existing logistics tracking technology to enable individual tracking of every container of shredded plastic right though to final customer sale.
- Remote machine monitoring of the shredders using IoT sensors to enable predictive maintenance and remote problem diagnosis.
- Establish social networks between schools and students to foster sharing of designs, ideas and curriculum.
- Artificial Intelligence
- Big Data
- Internet of Things
- Behavioral Design
- Social Networks
Children get out of their normal classroom and into the recycling lab. There they become highly engaged in learning about sorting, shredding, designing and creating. They also get to track precisely where their excess shredded plastic truly ends up.
This close level of engagement leads to ownership of the recycling process. This genuine ownership of the process and direct personal experience of which forms of packaging are easiest to recycle will impact purchase decisions. Children will be influencing their parents about which products to buy. This drives a direct commercial feedback to retailers and product manufacturers.
Ultimately their routine of taking plastic to school to be recycled will result in a shift in their perception of plastic as a valuable commodity rather than waste. This will lead to significantly lower levels of plastic waste entering the waterways as they will be in the habit of hanging on to plastic containers rather than simply discarding them.
- Children and Adolescents
- Very Poor/Poor
- Low-Income
- Middle-Income
- Australia
- Australia
We are currently working with a network of local schools that have a student population of around 1000.
Within one year we will have around 40,000 students across more than 100 schools.
Within five years we estimate we will be in 2.3M students in Australia. We are also likely to be serving around 1M students across the Pacific Islands.
We have already initiated discussions to test the market in India. If these discussions are fruitful we should be able to reach a few hundred million students and villagers across India.
The business model is highly scalable and has low capital investment for any individual site.
Within Australia our goal is to achieve 65% of schools within 5 years. This represents around 2.3M students.
The goal within the Pacific Islands is slightly different as the solution required there is for a combined school or community recycling capability combined with a local government commercial solution. We are currently in talks with one Pacific Island nation to firstly conduct a feasibility study and then run a pilot program. If there is a successful partnership model for that jurisdiction then we plan to work with all of the island nations to develop an integrated regional solution.
Our expansion model is to partner with local organisations (commercial and government) in other countries to modify our technical solution to suit the specific regional requirements. In most countries there should be significant opportunity to establish local manufacturing of the equipment thus creating local economic development and building local technical support capability.
There are few constraints on scaling the solution to any market in the world. Our long term goal is to operate in every country.
The primary barrier is around capital constraints. It is not possible to self fund the growth just through cash flow. The business will take around 24 months before it is cash flow positive. The same constraints will exist in every new country as the technical and service network needs to lead the roll out of the equipment.
We have a growth model that works in countries where there is a large degree of central coordination of the school system. India for example derived its school management system from the Commonwealth system so it is very similar to Australia. In countries where the education system is more fragmented or locally coordinated this growth model will need modifying.
Whilst there will be many similarities in the curriculum across the world, this will need to be developed with local educators for each jurisdiction.
We are currently talking to investors in Australia to raise the capital required to grow. In addition, we are pursuing the application of the shredding technology to commercial buildings and tenants to shorten the time to achieve positive cash flow.
We will identify business partners in each new country to both raise the capital, build local expertise and lead the local business operation.
We plan to target countries that have a large degree of central coordination of the education system first.
We plan to make the curriculum open source to enable rapid and distributed development of the best possible curriculum.
- For-Profit
Two full time and one part time staff.
Five contract engineering.
Contracted product design house.
Andrew Hynson: 34 YEARS OF ENGINEERING AND EXECUTIVE MANAGEMENT EXPERIENCE. Andrew is an engineer with extensive executive and business experience. He was the Chief Engineer at GM Holden who brought the Monaro to market in half the standard time and a quarter of the standard budget.
Geoff Collinson: 15 YEARS OF BUSINESS START-UP AND DIGITAL INNOVATION EXPERIENCE. Geoff is a constant innovator and entrepreneur in the digital business and musical education domains. He has founded multiple successful businesses including RivusTV/Spondo, Icestorm Digital and Aeyons.
Duncan MacWhirter: 25 YEARS OF FINANCIAL RESEARCH AND BUSINESS LEADERSHIP. Duncan has extensive global business expertise. He successfully combines a drive for disruption with robust financial management.
In addition we have a non-executive board member:
Greg Muller: Greg is the Founder & CEO of Gooroo, an ASX listed company that leverages the science of human thinking and artificial intelligence to empower every person and every organisations realise their true potential.
Combined we have the skills and experience to deliver technically, commercially and socially.
We are currently partnered with Footscray Learning Precinct and Gowrie Victoria Early Learning. They are developing curriculum and will be involved in the final detailed equipment design process as the voice of the customer.
They will also operate as our test sites for the pilot stage.
PlaSTEAMed installs unique equipment for recycling and making things from recycled plastic. We also provide machine monitoring, logistics solutions, shredded plastic sales contracts and information sharing platforms. The capability to instil tacit knowledge on top of theoretical knowledge is very highly valued by educators.
The equipment is financed so each school has no up-front capital spend. Excess plastic that is not used internally in the school is collected, aggregated and sold into the commercial market. PlaSTEAMed earns revenue primarily from a percentage of the plastic sales. We also gain revenue from program branding sales.
We have fully developed business models with monthly cash flows. We are raising investment capital to fund the growth phase. Our modelling indicates that we will be cash flow positive within two years in the Australian market. Revenue will exceed costs once we reach around 1000 to 1500 schools. The total domestic school market is 9500 schools and we have a plan to be in two thirds of those schools over a five year period.
In addition, we are applying for a state government sustainability and circular economy grant.
In parallel with the capital raising we have commenced negotiations to utilise our scanning-shredding-logistics capability in the commercial building sector. Any additional revenue from commercial sales will accelerate the time to positive cash flow.
The primary reason we are applying to Solve is get connected into a broader innovation ecosystem. The hardware/new business model startup eco-system in Australia is quite limited. By connecting to the Solve network we hope to get access to potential investors as well as advice from people who have walked this path before.
Additionally we hope there is potential for this network to connect us to potential partner organisations in other countries who may be interested in working with us to accelerate the growth of the business.
Of course, being selected to be part of something that is run by an institution with the gravitas of MIT would significantly add to our ability to raise capital. Winning one of the prizes on offer would also significantly add to our credibility when talking to potential investors as well as government agencies.
- Distribution
- Talent or board members
- Media and speaking opportunities
We would be interested in partnering with educational organisations, especially those that have experience in the development of engaging STEAM curriculum. We would be interested in exploring the opportunity for a global branded curriculum.
We would also be interested in partnering with companies that have a requirement for STEM employees. There is an opportunity for a company such as Siemens or GE or one of the global automotive companies to strongly influence future generations of students.
There is an opportunity to significantly improve the quality of the shredded plastic in the overall recycling ecosystem by using our technology. Product contamination, especially with different types of plastics with different mechanical properties acts as a drag on the entire plastics circular economy.
By combining education around why separation of plastic streams and cleanliness of input packaging is important, with a combination of sensors (and the ability to scan individual packages at a non-industrial rate) backed up by AI, there is an opportunity to produce extraordinarily clean recycled plastic. Our aim is to get our system certified to produce the gold standard of recycled plastic - food grade PET and HDPE. This minimises the degradation in the circular value chain and increases the value of the shredded plastic.
Our business model enables the scanning of bottles at speeds that result in AI analysis of each individual bottle. We intend to have key schools participate in training the system to recognise new containers. We will develop specific curriculum to teach students about AI and how to use off the shelf algorithms in their school projects.
Disclosure - Andrew Hynson worked with Mark Reuss at GM Holden.
Our system significantly increases the volume of PET/HDPE that is recycled. Our community level technology drives a significant increase in ownership of the recycling process.
Key to its success is the impact on purchase decisions providing immediate economic feedback to the retailers and product manufacturers combined with statistical packaging data.
Our focus is on habit change around recycling plastic. We will raise awareness of what is involved in the recycling of plastic and through that drive changes in purchasing decisions around product packaging. By educating an entire generation about which plastics are easy to recycle and which aren’t, these changes in purchase decisions will result in significantly less waste going to landfill.
Recycled plastic requires ~50% less CO2 to produce than virgin plastic. We will significantly reduce the quantity quantity of virgin plastic required to meet the global demand.
Our distributed model of shredding eliminates a large portion of the logistics costs. By shredding the plastic before transporting it we avoid shipping large quantities of “air”. We use existing logistics networks that would otherwise be empty.
Our technology enables STEM to come alive. By combining theoretical education with tacit knowledge from our STEAM curriculum, we will lift the interest and engagement of students – starting in Kindergarten.
The pinnacle of our curriculum will be final year design challenges. School teams will compete to establish a genuine start-up business based on the design of a new product made using micromanufacturing techniques.
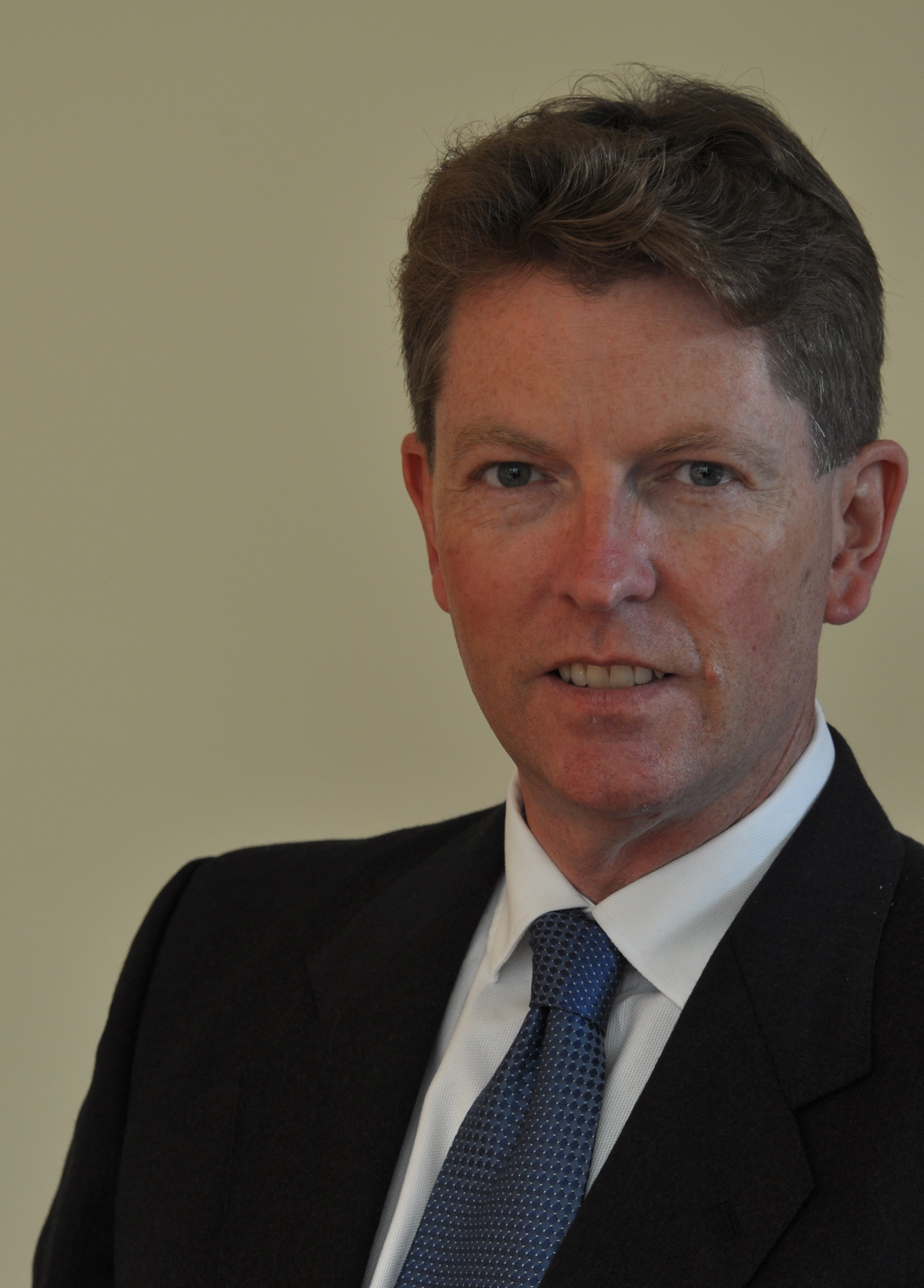
CEO