ECO-BRICKS BUILDINGS
Several cities in Africa are faced with the problem of indiscriminate disposal of plastics waste and at the same time housing deficit is on the increase. To solve both problems, recycling of post-customer plastic waste for eco-bricks production and utilization for building construction is evolving. However, the limit state of building components constructed of plastic waste lacks credibility as there are no specific standard addressing the technology and such buildings pose serious threat to life of occupants and the technology may fail to gain traction. This solution involves the production of eco-bricks using plastic waste in three different modes of application to investigate the limit states of walls constructed of eco-bricks with a view to developing
alternative masonry that satisfies limit state requirements. The solution not only promote circular economy but it is also beneficial to the construction industry and the built environment in delivering sustainable buildings.
Plastic is considerably one of the major innovations of man that finds its applications in virtually all sectors of industrialization. The wide range application is attributable to the unique properties of plastic such as durability and low cost of production resulting in consistent rise in demand for plastic.
Geyer et al., (2017) reported that the worldwide production of plastics is approximately 8.3 billion metric tons, while over 7.3 million metric tons of plastic waste is generated annually. In some places, waste PET bottles are discarded indiscriminately, constitute huge environmental nuisance, blocking drains and impeding the free flow of water channels and canals (Adewumi, 2006).
Contrary to plastic waste excesses is shortage of houses for the poor and the number of homeless persons is increasing. To solve housing problems the use of plastic waste especially waste PET bottles is gradually evolving. However, there are no standards guiding the technology and such buildings pose serious threat to life of occupants. It is therefore important to investigate the limit states of eco-bricks masonry to develop alternative masonry that satisfies limit state requirements and serve as guide for the technology.
This solution is beneficial to a wide range of people who are involved in the recovery of waste plastics from the streets and refuse dump sites, masons and labor who produce eco-bricks and use same for building construction. The solution is currently being conducted in a university community with senior researchers and cleaners who are involved with recovery of waste plastics. Masons and labor assist in production of eco-bricks and construction of masonry wall prisms with eco-bricks made with plastic waste. The eco-bricks and prisms are tested in the laboratory.
The solution will be beneficial to the construction industry and the built environment in delivering sustainable buildings. It will contribute significantly in enhancing the quality of life and promote low energy buildings. Eco-bricks Technology will also increase housing provision and create millions of jobs for unemployed persons and advance the sustainability of plastic production business and also provide opportunity for diversification.
Waste plastics is employed in various modes in the production of eco-bricks to verify suitable application of the plastic waste to building work. Plastic waste is applied as an encapsulate, fine aggregate replacement and binding agent for eco-bricks production.
The use of waste plastic as a binding agent for eco-bricks production involves heating of waste plastics in a drum to liquefaction and the resin is used in binding fine aggregates (sand) and the mixture cast in brick molds. Within three hours the resulting product – eco-brick sets and it is demoded for use as bricks in masonry walls construction.
As fine aggregate replacement, waste plastics are shredded to less than 5mm particle sizes which are used as aggregate in partial replacement for sand in the presence of cement and water for eco-bricks production. The mixture of waste plastic aggregates, sand, cement and water is cast in molds which hardens in less than 24 hours. The bricks are demoded and cured for 14 days after which it is ready for masonry wall construction.
The use of plastic waste as encapsulate involves filling waste PET bottles with air dried laterite soil material or moist sharp sand which are compacted in three layers and corked. The resulting eco-bricks or bottle bricks are used together with mortar for masonry construction.
All eco-bricks and masonry walls constructed of the eco-bricks are subjected to various limit state tests in the laboratory to determine the suitability for building construction.
- Enable recovery and recycling of complex products
- Prototype
- New business model or process
The current methods of plastic waste management in many countries do not promote circular economy. The three major plastic waste management methods - incineration, landfilling/disposal and recycling. Among the management methods incineration irrefutably constitute CO2 gas emission; also, methane gas emission from waste plastic landfill site contribute to global warming. Approximately 5% of plastic waste is dispose into the sea 43% in landfills and 52% are shipped to low environment regulation countries. Recycling method of plastic waste promote circular economy but presently the huge quantum of waste plastic generated on daily basis overwhelms available recycling plants and the limit to which plastic could be recycled beyond which the plastic looses essential properties constrains perpetual recycling. Hence there is need to find sustainable solution to plastic waste management. This solution proposes not only production of eco-bricks from plastic waste but also determine the suitability of such eco-bricks for sustainable building construction.
Some researchers have investigated the potential use of waste plastics for manufacture bricks and paver blocks but it is important to examine the performance of masonry constructed of such waste plastic materials as the performance of masonry does not solely depend on bricks but also mortar joints and environmental conditions. Literature on waste plastics modified bricks masonry are currently not available. Hence, investigating a whole masonry wall constructed of waste plastic to determine the suitability for construction in line with Euro code 6 is a necessity for such material to gain traction in the construction industry.
The technology of the project involves use of washing tube, oven or kiln, shredders, concrete mixers, vibration platform, brick molds, spade, trowels and pallets. The washing tube uses water to reins off dirt from waste plastics, which are then sent to the oven/kiln or shredder. At the kiln washed waste plastics are heated to temperature between 1200C to 2000C to produce resin used as binding agent in place of cement for eco-bricks production. The shredder receives washes waste plastics and cut the plastics to fine aggregates less than 5mm particle sizes. The fine aggregates are then feed to the concrete mixer where it is mixed with sand, cement and water. The resulting mixture is placed in brick molds which are compacted at the vibration platform. The vibrated eco-bricks are demolded on the pallets and conveyed to a curing position. The trowel is used for finishing the eco-bricks surfaces in the mold when necessary before demolding while deformed eco-bricks are packed with spade.
The use of waste PET bottles for eco-bricks production as bottle bricks involves filling washed waste PET bottles with sand and corking same. The bottle bricks are then place in a pallet and conveyed to store or site for use as eco-bricks for building construction.
- Indigenous Knowledge
Production of eco-bricks with plastic waste will significantly reduce the threat of plastic waste disposal because exploratory survey has shown that plastic waste cannot be found in Yelwa Village, Kaduna State, Nigeria where the first eco-bricks building in Africa was constructed. Rather, as more eco-bricks buildings are been constructed waste plastics are sold and procured at a cost from nearby cities. Hence, if the technology is extended to accommodate non-PET bottle waste plastics for use as aggregates and resins in eco-bricks production and building construction, Africa will be rid of plastic waste. Also, the region of Cameron covered by Roger Mila Foundation which is involved with the use plastic waste in production of interlocking stone is free of waste plastic threats.
However, there is a serious threat to the propagation of the eco-brick masonry technology as professionals in the construction industry do not recommend eco-bricks to clients for building construction because the ultimate and serviceability limit sates of eco-bricks masonry are unknown. This solution is designed to fill this gap so that the limit state of eco-bricks masonry will be known and then, the technology can be used by professionals in the construction industry for building construction.
- Women & Girls
- Pregnant Women
- Children and Adolescents
- Infants
- Elderly
- Rural Residents
- Peri-Urban Residents
- Very Poor/Poor
- Low-Income
- Middle-Income
- Refugees/Internally Displaced Persons
- Persons with Disabilities
- Nigeria
- Nigeria
Although this project is at the experimental (pilot) stage, 14 persons excluding researchers are currently working on the project. The 14 persons include 2 masons who build the masonry walls, 6 labor deployed for eco-bricks molding and 6 cleaners involved with retrieving and washing of waste plastics. It is expected that the experiment will produce eco-bricks masonry that will satisfy minimum requirement standard of 50 years life span specified in BS EN 1990 (2002). Ones the eco-brick masonry wall designs satisfy the requirement the project will be commercialized to serve the lager society. It is expected that in the next one year 50 persons will be involved in the project and in the next 5 years over 150 persons will be using eco-bricks technology to earn a living with over 200 buildings constructed with eco-bricks in Nigeria.
The goal of the project is to promote sustainable building construction, cleaner built environment, circular economy and create jobs for our people.
We project that in the next five years, commercial eco-bricks production sites will be established in six major cities in Nigeria to utilize the overwhelming chunks of plastic waste been generated on daily basis. In addition, training centers will be establish to train interested persons on how to use the technology.
The major challenge to this project is funds. If funds is available equipment and machine could be procured easily for testing of specimen and onward operation. Alternatively, specimen could be conveyed to standard laboratory where relevant tests could be conducted to be sure of the eco-bricks masonry before full operation could commence. Also, technical personnel and equipment to properly instrument specimen in the laboratory is scares. The operation plants will also require technical personnel to set up a workable plant for commercialization of the products.
We are presently in talk with Stellenbosch University, South Africa for permission to conduct fatigue loading test on eco-bricks masonry in their Civil Engineering Laboratory. Once the application is granted and positive result is recorded from the test, commercialization of the eco-bricks production will be kick started.
In the absence of funds, the production of eco-bricks will be started in small scale with local fire drums, manual washing of waste plastic, spade, and trowel. These tools will be used just as employed in the production of experimental samples to produce eco-bricks.
At the initial stage of the commercialization process funding is expected to come basically from personal salary just like this experimental stage. Although, financing the project from personal salary has not been ease and this has caused the project to face delays, the results of the findings have been encouraging. We are hopeful grant will be made available for the project in the future to facilitate the entire process.
- Not registered as any organization
The solution team members are 19 in number comprising two full-time staff of University of Lagos, Nigeria, one full-time staff of Bells University of Technology and University of Lagos postgraduate student and 16 others.
Our team will deliver on the project because the team is composed of experienced members in the minute details of component required to achieve the goal of the project.
For instance, Professor Martin Dada, a member of the team has published several articles on construction management while Associate Professor J. O. Ameh has been conducting series of research on construction materials. Their experiences in these areas are yielding the needed result.
The project is at the experimental stage and ones the results of the experiment is positive we will partner with Greener Environment and Materials Sustainability initiatives (GEMS).
The Eco-bricks technology involves production of eco-bricks from plastic waste. Retrieval of plastic waste from the built environment promotes cleaner environment and reduces the threats of plastic waste disposal on the environment. Also, the technology provides job for persons involved in the recycling process; it provides jobs to the cleaners who basically are the extreme poor engaged with retrieval of plastic waste from the environment. They are paid on daily basis with respect to the mass of plastic waste gathered or washed.
The eco-bricks moulders are paid on daily basis.
The financial sustainability of this solution is dependent on the experimental results. We are hopeful, as the results of the experiment so far have been positive and hereafter the technology will be commercialize. Ones the technology is commercialized it is expected that it will get patronage from the construction industry and the eco-bricks technology will become sustainable and profitable.
We are applying to Solve for assistance in funding the conduct of the experiment in an equipped laboratory.
Apart from funding, we will be grateful if Solve could assist in setting up industrial plant in Nigeria where plastic waste could be recycled into fine aggregates and resin for eco-bricks production. Also, assistance in training interested persons (labor and masons) on the use of eco-bricks for sustainable building construction will be highly appreciated.
- Technology
- Funding and revenue model
We will like to partner with construction industry professionals and building material producing companies such as Nigerite, Dangote Group and Lafarge.
We will apply for GM Prize on Circular Economy.
The funds that will be made available to our solution by GM Prize on Circular Economy will be used to complete the conduct of experiment in a world class laboratory like the MIT or Stellenbosch University. Part of the funds will be used to set up eco-bricks production plant in Nigeria.
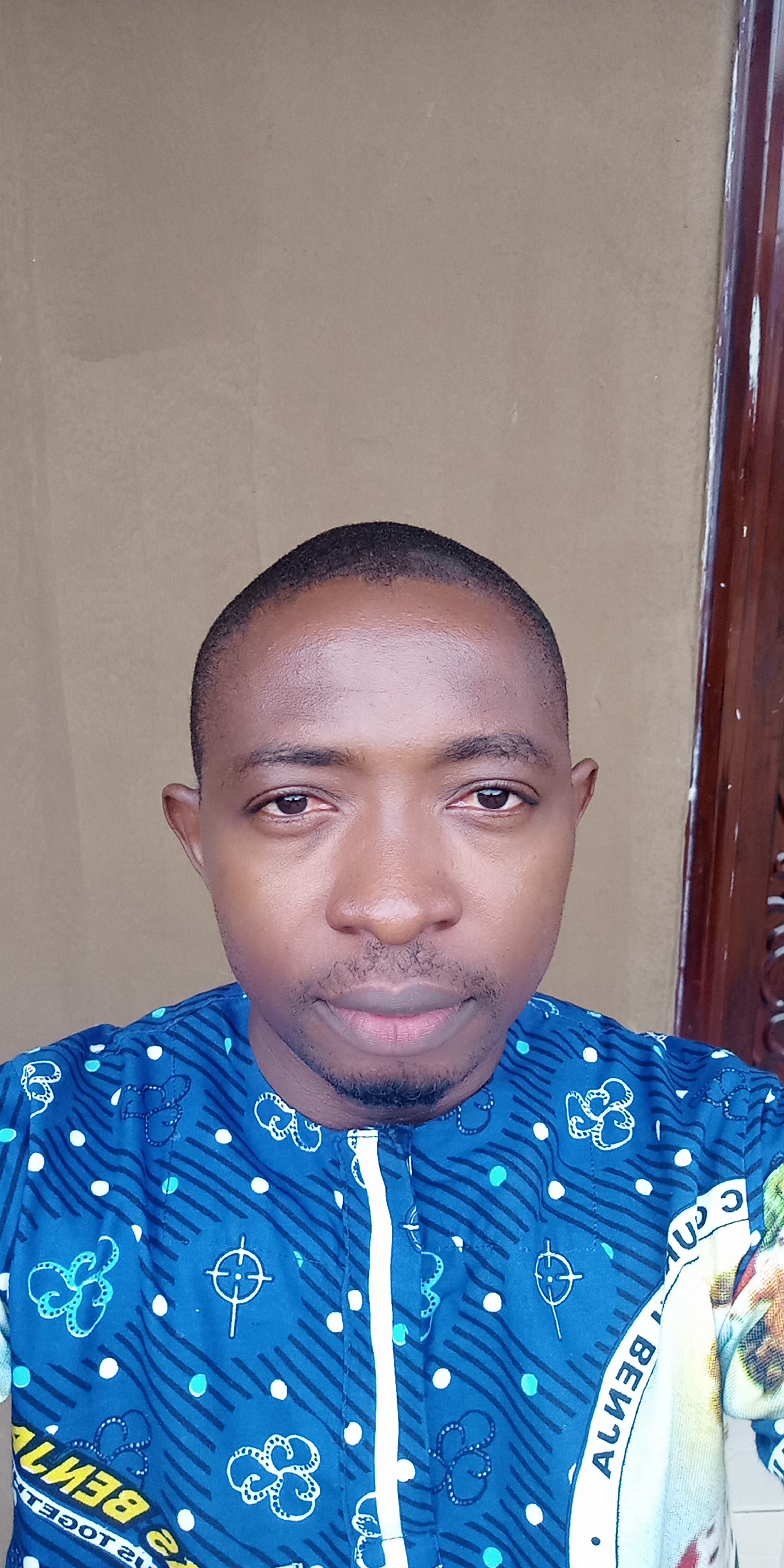