MicroRecycling Systems
MicroRecycling Systems is working on a platform technology aimed at disrupting how we extract value out of recyclable materials. We are developing a new type of “micro” recycling equipment, designed to handle complex products at low cost with an exceptionally small footprint so it can be utilized outside of the traditional recycling venues. Our equipment quietly and quickly shreds and separates the base materials of complex, compounded products so they can be sold to the existing scrap material supply chains.
A large quantity of the stuff in our trash cannot be recycled even though they are made of recyclable and potentially valuable materials. This is a profit-making opportunity that is currently wasted because there are technology gaps that stand in the way to realizing those opportunities. We are inventing those technologies.
A sizable portion of the 2 billion tons of solid waste generated per year are complex products, with no path to sustainable disposal. Today’s recycling system is focused on a short list of prescribed waste from homogeneous products (e.g., plastic bottles, metal cans) that are disposed regularly and in vast quantities. The waste is collected regularly on a massive scale and treated in large centralized facilities. The current system is therefore ill-suited for processing complex products because they are heterogeneous in composition and shape, and generated sporadically (e.g., we throw away phone chargers once or twice per year, not every week).
Most of the materials in complex products are recyclable and sometimes are quite valuable (e.g., gold, palladium), unfortunately, once assembled together the materials cancel out each other’s recyclability and value. Disassembly by hand, employed for high-value waste like computer components, is too expensive to be practical for processing most products. Therefore, there is a need for recycling technology for complex waste that is inexpensive to own and operate, scalable to support large populations, and yield materials that can be sold for profit or used in new products.
We are focusing on strategic junctures in large cities (> 1 million people) of developed economies, reasonably connected to local or global supply chains, where waste from complex products can be collected cost-effectively. The need seems to be most urgent in the U.S., where waste and recycling policy is notoriously lacking (technically, the U.S. is not even part of the Basel Convention, that governs the export of e-waste, since the U.S. Congress has not yet ratified it), and a large population and wealth makes for tremendous amounts of waste. We foresee that natural adopters of our technology are (a) entities that already come across complex waste as part of their operations, like IT asset destruction companies, thrift shops, department stores, (b) manufacturing operations generating scrap or byproduct waste that is not “clean” enough for current scrap trade, and (c) organizations with a large member-base that they can rally behind collection programs (e.g., large bureaucracies, schools, churches, community organizations). Our impact in the communities we serve will consist on (1) diverting waste destined for landfill or incineration; (2) opening untapped revenue streams; (3) supplying raw materials for local, circular economic activity.
We are developing an enabling platform technology to automatically separate and sort materials from complex products that is 100x to 1000x smaller, in size, capacity, and cost, than current recycling technology, while incorporating greater sorting capabilities. We are currently targeting processing capacities of 10 - 100 lbs/hour.
Scaling down the size of the equipment means that our systems can be deployed in marginal spaces within cities (e.g., basements, mechanical rooms) and will not require trucks, forklifts, or operators, thereby significantly reducing capital and operational costs. Since small scale systems can use methods impractical for large scale sorting, they can sort material according to a wider and more nuanced criteria than current systems, such that the material sorted reaches the quality necessary to have a demand (by and large, current recycling technologies are not able to do this for complex products). Our aim is for the output material to be of sufficient quality to be able to “plug-and-play” into current recycled and virgin material supply chains. Additionally, our systems will “know” the type, value, and amount of material it has processed in real time. This can support business decisions and just-in-time maintenance schedules. They can also shift sorting algorithms to adapt to the materials provided to the machine, for example by prioritizing accuracy in sorting high-impact materials over speed.
- Enable recovery and recycling of complex products
- Prototype
- New technology
MicroRecycling Systems is leveraging deep technical expertise in research and development areas such as medical devices, advanced materials, sensing, meso- and microfluidics, and nuclear physics, to develop a new generation of cost-effective recycling technology.
Our technical approach allows sensors to ask nuanced questions about the materials being processed (if plastic: what type? If glass: what color? If metal: what elements?) and sort it in just one pass with more granularity than an entire building of current recycling systems could. The system will also “know” the type, value, and amounts of materials it has processed, which can be useful for maintenance, business, and supply chain management.
Because this technology is so fundamentally different from current technologies, in both scale and capabilities, we expect it to enable novel business models beyond our own. For example, we foresee that our technology could enable mobile processing units, easy to use and rented by the hour, that anyone can use to run their own recycling pickup routes and earn extra cash in their spare time.
We are fitting the functionality of an entire sorting facility inside a small machine. To do so, we borrow the approach taken by cell cytology systems: they sort tens of millions of cells per hour by quickly looking at each individual one and deciding which “bin” they belong to. In our case, we start by crushing waste products to pieces (i.e., mechanical separation) small enough so that each piece is mostly made of a single material. Then we run each individual piece, very quickly, through “sorting units” comprised of a suite of sensors that identify the piece’s composition and decides to which bin to direct it.
The capacity of our systems scale with the number of “sorting units” in each system. Systems small enough to fit in a limited space may have a few sorting units, while larger capacity systems will have many (we estimate that a typical system will have 10 – 100 sorting units working in parallel). Since each sorting unit is small, it becomes practical to employ powerful inexpensive sensing methods that are impractical for large scale systems, and that provide greater functionality for equivalent cost-to-capacity ratio as large systems
The materials that make up complex products are commodities, and as such they have a price set by market forces. However, each load of material has to be sufficiently free from deleterious contaminants to find a buyer, regardless of the price. The response from our market research among people in the recycling and metal scrap industries has been clear: if the technology can deliver the sorting quality and price point required, there will be strong interest in adopting it.
- Peri-Urban Residents
- United States
- United States
One of our partners is the largest ITAD service provider in the Washington, D.C. metropolitan area (U.S.), which has a population of +6M. Within five years we plan to have expanded to other U.S. metro areas, thus covering geographic areas of several million people and billions of USD in economic activity (and accompanying trash).
number of people you’re serving: 0
number you’ll be serving in one year: 100 - 1,000
the number you’ll be serving in five years: +10,000
In the next year we plan to deploy a beta prototype to separate materials from a single product (hard drives, which are collected and destroyed verifiably for a fee, but whose mixed scrap sells at a discount despite containing precious metals). In years 2 – 4 we will refine our technology to increase reliability and expand the breadth of products our systems can handle. In year 5 we plan to start shipping our recycling systems to third parties.
Our greatest short-term needs include a working space appropriate for developing hardware (MicroRecycling Systems is currently operating out of the basement of the founder), a larger technical and business team.
Over the next five years we will need to expand relationships in the scrap supply chains in order to align technical capabilities with market opportunities. We will also need support in designing and manufacturing equipment for scale-up production and sale.
We engage with events and activities, such as MIT Solve Competition and local professional “green” entrepreneurship networks, reach the passionate talent that we need to attract. We have an industrial partner that will serve as a bridge to the local scrap material supply chain. We are in discussion with another potential partner to provide expertise in manufacturing of our recycling systems. Options for working space should open up as we meet technical milestones, strengthen external partnerships, and become successful at attracting early stage funding. The founder is focused on developing and demonstrating the technical capabilities of our systems.
- For-Profit
The core of MicroRecycling Systems is Mario Urdaneta, PhD, an engineer with 20 years of experience developing advanced technologies for areas that include nuclear medicine imaging, additive manufacturing, and microelectromechanical systems Additionally, MicroRecycling Systems benefits from highly-trained volunteers and advisors, that provide guidance on business strategy, technology development, and intellectual property.
Our team and partners combine deep technological and scientific expertise, a track record of entrepreneurship, and experience working specifically in the e-waste recycling industry. Our founder, Dr. Urdaneta, started focusing on technical solutions for e-waste (waste from electronics equipment) in 2015 while working at the U.S. Department of Energy, Advanced Manufacturing Office, as an AAAS Science and Technology Policy Fellow. His focus continued during his tenure at MForesight, a U.S.-based manufacturing policy think tank, while analyzing systemic economic challenges and technology gaps in the U.S. manufacturing industry. As the potential of advanced small-format recycling became increasingly evident, Dr. Urdaneta returned to his hardware-development roots in the medical devices and 3D printing industry and started MicroRecycling Systems.
Additionally, we are located in a region (Eastern seaboard of the U.S.) with abundant waste rich in valuable materials, good access to commodity markets and infrastructure, and a large pool of high skill workers.
Our most important partnerships are with Elizabeth Wilmot and Marc Dandin, PhD. Elizabeth is a pioneer in the e-waste industry who founded and operated one of the first e-waste disposal services in the U.S. for over a decade. Elizabeth’s grounded and informed advice has enabled us to focus technology development on commercially-relevant solutions. Marc Dandin, PhD, CEO of Kiskeya Microsystems and incoming electrical engineering professor at Carnegie-Mellon University, has deep expertise in sensing technology and intellectual property that is helping position MicroRecycling Systems for long-term success.
We will be first testing and employing our systems in partnership with the largest Information Technology Asset Destruction company in the Washington, D.C. area. This company will provide us a steady supply of material and a channel for the sorted material into their recycled material supply chains.
We are in discussions with a local entrepreneur with experience scaling up the production of 3D printers (related to one of his startups that had a record-shattering Kickstarter campaign). The NSF I-Corps program, based at George Washington University, and Potential Energy DC, a local incubator for “green” technology companies, are providing additional entrepreneurial coaching and training.
1-5 yrs.: Our short-term business plan is to use our own systems to process materials and sell them in the commodities market.
5-10 yrs.: Sell or rent our disruptive recycling systems and provide maintenance, material pickup, and brokering services to our customers. Other options include entering the scrap material business by purchasing low-cost mixed waste and selling it at higher price once sorted.
10-15 yrs.: To scale globally we are considering various options, including licensing the technology to recycling equipment incumbents and franchising the service activities to local partners.
Early operations are being funded by the Founder. MicroRecycling Systems will need seed funding, like that from prizes or angel investors, to move from an engineering prototype to a production prototype. Once we have viable prototypes operational, we will use them earn revenue for sorting high-value e-waste generated by our industrial. This revenue will bootstrap further technology development and scale-up manufacture of recycling systems.
Visibility from participating in MIT Solve Prize gives us the opportunity for establishing partnerships across communities, institutions, and private companies, that we need in order for our promising technology to be relevant in the real world. MIT Solve also gives us a chance to attract professional talent and “smart money” funding, and the opportunity for direct funding in the case we are honored with an award.
- Technology
- Talent or board members
- Media and speaking opportunities
- Other
In order to thrive we need to be better connected to the U.S. hardware startup innovation ecosystem. Innovation ecosystems encourage a flow of ideas, solutions, talent, business opportunities, and boost morale, all of which would be gainful to us. We would also benefit from strategic partnerships with generators of complex waste to guide technology development and serve as early adopters of the technology.
MicroRecycling Systems will use the monetary prize to design and manufacture production prototypes and acquire needed scientific equipment.
We will also leverage the bragging rights to rally new partnerships. Including partnerships with GM manufacturing facilities to treat complex waste and scrap from their manufacturing operations using our equipment .
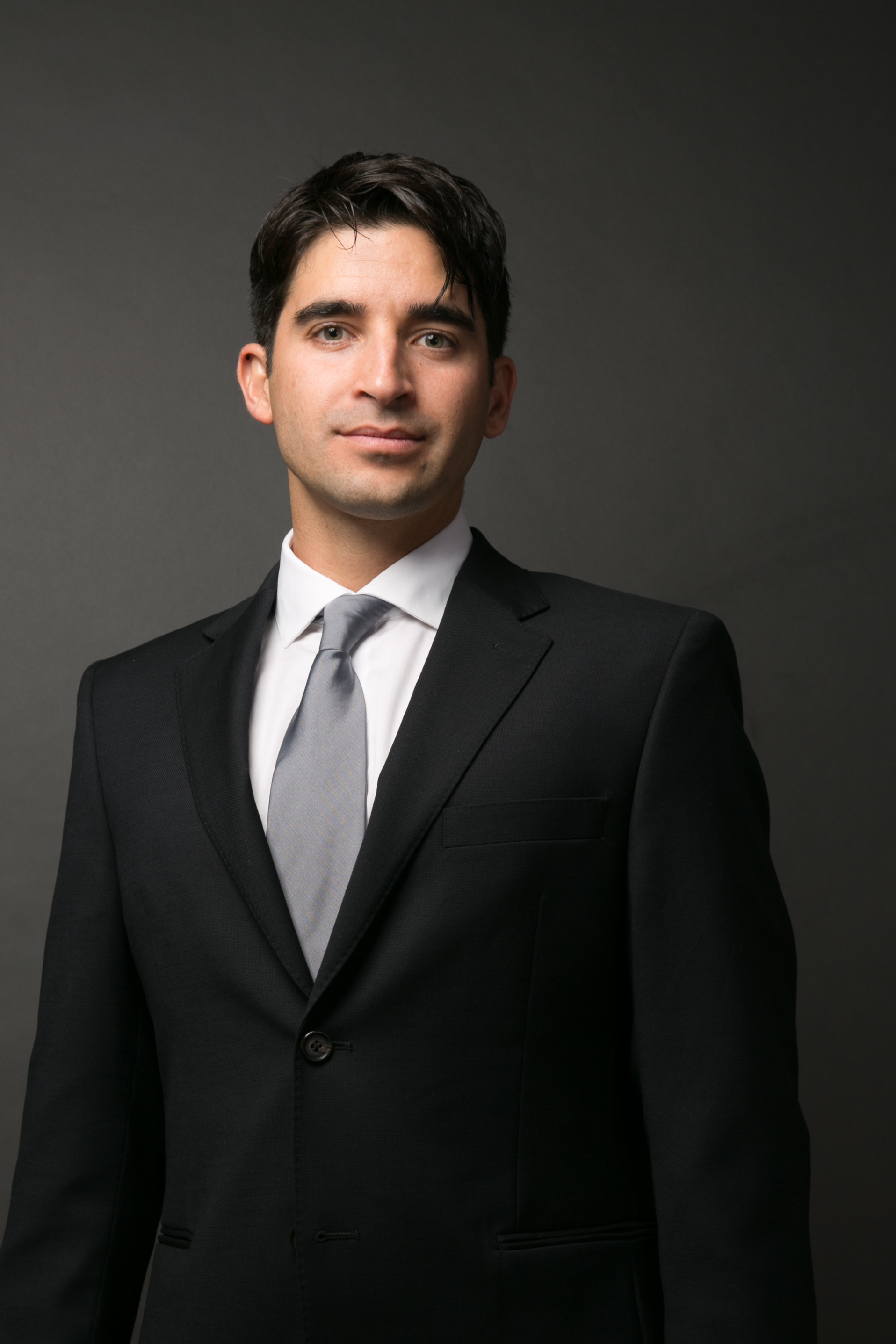
Founder and CEO