ATP's CRBBP Process=Cost-Advantaged Circular Economy Fillers
There is a growing need for plastics and composites which are stronger, lighter and more water and heat resistant. And, due to environmental concerns, there is a need for bio-based and recyclable plastic and composite materials.
ATP seeks to license and utilize a patented process, developed by the University of Akron (UA), in combination with ATP’s patented torrefaction process, to convert CRBBP Process biomass into cost-advantaged, bio-based fillers, which, when blended with polymers and resins, will make enhanced plastics and composites, which are stronger, lighter and more water and heat resistant, for use by key customers in the $380 billion US plastics market.
Given the growing concerns about climate change, environmental contamination and plastic pollution, our recently-patented Combined Remediation Biomass and Bio-Product Production (CRBBP) Process, by which we plant and then multi-task certain bio-crops and their biomass to do good things for people and the planet, less expensively, enables us to both remediate air, soils and waters, and make a bio-based, filler powder, which when blended with bio-based polymers, makes “circular economy plastics”, which can be recycled and never need to end up in a landfill. As difficult as it may seem, our CRBBP Process' multi-tasking approach can overcome multiple environmental challenges, while making cost-advantaged bio-products, including enhanced bio-based fillers.
Everyone.
Approximately 10 years ago, we licensed and patented a mobile and auto-thermal torrefaction technology, which converts biomass into a carbon and energy-rich material, which can be used to make a variety of bio-products, including: bio-based fillers, which make better-performing plastics; biochar, to enhance the productivity of poor soils; and clean and renewable bio-coal, to lessen the environmental impacts of coal-fired power plants.
Plastics and composites are created by combining resins and/or polymers with a filler powder, traditionally made from wood flour, mineral powders or carbon black. Plant and woody biomass material, which has been carefully heated (Torrefied) and ground into a powder, will out-perform traditional fillers and allow the production of plastics and composites which are stronger, lighter and more water and heat-resistant, than if they were made using traditional fillers. The University of Akron has patented a process of making torrefied biomass fillers.
Again, using our patented CRBBP Process, we plant and then multi-task certain bio-crops and their biomass to do good things for people and the planet, less expensively, including remediating contaminated land and water and capturing atmospheric CO 2, then reusing and sequestering the captured carbon in a cost-advantaged bio-products, like torrefied biomass fillers.
- Increase production of renewable and recyclable raw materials for products and packaging
- Prototype
- New business model or process
I believe the multi-tasking and cost-saving features of our CRBBP Process are the most important differentiation. Again, the ability to cost-effectively solve multiple problems, because of the multi-tasking features of our CRBBP Process cannot be overstated, as we seek to solve several environmental problems, either simultaneously, or sequentially, using our innovative CRBBP Process.
Again, we plant and then multi-task certain bio-crops and their biomass to do good things for people and the planet, less expensively, including remediating contaminated land and water and capturing atmospheric CO 2, then reusing and sequestering the captured carbon in a cost-advantaged bio-products.
- Biomimicry
I believe the multi-tasking and cost-saving features of our CRBBP Process are the most important differentiation. Again, the ability to cost-effectively solve multiple problems, because of the multi-tasking features of our CRBBP Process cannot be overstated, as we seek to solve several environmental problems, either simultaneously, or sequentially, using our innovative CRBBP Process.
- Women & Girls
- Pregnant Women
- LGBTQ+
- Children and Adolescents
- Elderly
- Rural Residents
- Peri-Urban Residents
- Very Poor/Poor
- Low-Income
- Middle-Income
- Minorities/Previously Excluded Populations
- Refugees/Internally Displaced Persons
- United States
- United States
None, as we are in a demo mode.
ATP’s Project Plan involves it collaborating with companies, in Ohio and the mid-West region, who prepare bulk amounts of concentrated formulations (compounds), from which plastics and composites are made, for sale to industrial companies and other manufacturers in the region. ATP anticipates market entry within one year after the project begins. ATP-OH is already talking with prospective customers and may include one or more customers in the Project Team.
ATP will produce and supply the torrefied, bio-based fillers to such compounders, for $300-$600/ton, instead of their using fillers made from wood flour, corn starch, mineral powders or carbon black. This will allow the compounders’ customers to make stronger, lighter and more heat and/or water-resistant plastics, depending on which traditional filler has been replaced. As it prepares to enter that market, ATP-OH will use this project and its funding to prepare and perfect samples of its fillers and have them tested by compounders and bench-tested, by their customers, to confirm and optimize performance. ATP will source the raw materials (biomass), contract to have that material torrefied and ground and then provided to one or more compounders, for testing.
None.
Work hard.
- For-Profit
one.
Hard working
University of Akron.
ATP’s Business Model involves it collaborating with companies, in Ohio and the mid-West region, who prepare bulk amounts of concentrated formulations (compounds), from which plastics and composites are made, for sale to industrial companies and other manufacturers in the region, who make products containing plastics and composites.
ATP will produce and supply its torrefied, bio-based fillers to such compounders, for $300-$600/ton, instead of their using fillers made from wood flour, corn starch, mineral powders or carbon black. This will allow the compounders’ customers to make stronger, lighter and more heat and/or water-resistant plastics, depending on which traditional filler has been replaced.
As it prepares to enter that market, ATP will use this project and its funding to prepare and perfect samples of its fillers and have them tested by compounders and bench-tested by their customers to confirm and optimize performance.
ATP will source the raw materials (biomass), contract to have that material torrefied and ground and then provided to one or more compounders, for testing. ATP will work with its contractors to make sure its torrefied biomass fillers meet the appropriate standards.
ATP’s commercialization strategy is to provide samples of torrefied biomass fillers to compounders, so that they and their customers might prepare and test the resulting plastics and composites, during the last third of a year-long project.
ATP believes that TVSF Grant funding, in the requested amount ($95,000), will be sufficient to get its torrrefied fillers tested and entered into the market. ATP-OH’s founder has already begun to explore collaborations with compounders in the region, with encouraging levels of interest.
It is expected that one or more customers will want to purchase fillers from ATP on an ongoing basis and, with such purchase contracts in hand, ATP believes it will be able to secure SBA-guaranteed bank loans for required equipment and working capital.
Given the great concerns about plastic pollution, our recently-patented Combined Remediation Biomass and Bio-Product Production (CRBBP) Process, by which we plant and then multi-task certain bio-crops and their biomass to do good things for people and the planet, less expensively, enables us to both remediate air, soils and waters, and make a bio-based, filler powder, which when blended with bio-based polymers, makes “circular economy plastics”, which can be recycled and never need to end up in a landfill. As difficult as it may appear to be, we can solve several environmental problems, either simultaneously, or sequentially, using our innovative CRBBP Process.
- Business model
- Technology
N/A
Car and plane manufacturers.
N/A
Make cars lighter but stronger to max fuel efficiency.
N/A
N/A
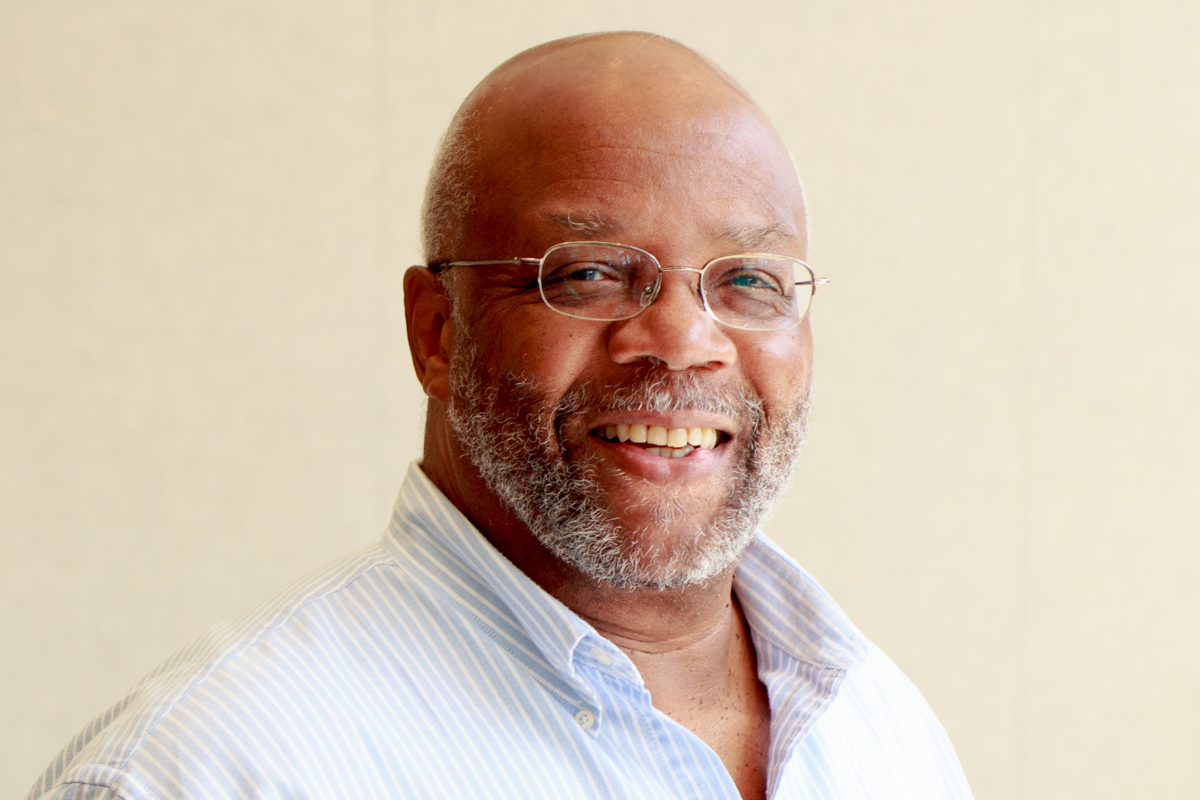
President