IRO IRO: zero waste
We upcycle textile waste through crafts of India transforming it into elegant zero-waste clothing. This way we plant circularity into the system of apparel manufacturing, generate employment in rural villages, help craft traditions to sustain all while cleaning the environment. We collaborate and implement this system into apparel manufacturers, hotels, design houses and any textile waste producing businesses. We design clothing and accessories that are multi-functional, and zero-waste, bold and elegant.
We focused on 3 problem areas 1) Apparel manufacturing units these units would manufacture for export purposes to developed countries hence their clients are growing conscious. They provide the raw material, which is waste and a client base. 2) Crafts clusters India is renowned for its textile crafts located at sometimes isolated villages when fast fashion grew their livelihood depleted and these craftspeople were forced to find other work. They upcycle it. 3) Design houses/hotels with growing consciousness about the value chain of fashion, they need a full proof product for their customer that is aesthetically pleasing. They pay for the end product.
The weavers we work with were given hand-looms at 12 rupees a loom post independence. They had always been weaving khadi therefore could develop their skills and pass it on but the craft could never develop a character of its own. Onset of 2008 they had not been receiving enough work therefore had to move to alternative jobs. However weaving remained something that they could do from their homes without having to move to metro cities where their quality of life vastly depleted. Iro iro grew from 3 weavers in 2017 to a family of 26 weavers by the end of 2018. Many of them are women who were not allowed to work outside of their homes decided to learn weaving and now maintain an independent income.
We upcycle waste through craft like hand-weaving, creating a quality product. This way the age old craft gets a unique value proposition to have sustained business. For the making of the IRO IRO up-cycled fabric we sourced textile waste from clothing industries. Offcuts are pieces of waste material that are left behind after cutting a larger piece. Hence offcuts would come in irregular sizes, qualities and colours. All these offcuts are first sorted by hand by women who have formed Self Help Groups and then they are cut into tiny scraps and tediously sewn back together to form a liner yarn. This liner yarn is then hand woven into our fabric. This process is time-consuming and difficult but it is as beautifully unique as it is kind to the planet and its people.
· We are also developing a fabric made from an alternative fibre called aakh that grows without water. We have researched and we know we can scale it up and develop the actual fabric. This fibre does not require any water to grow and grows as a wild plat in the hottest of areas and blooms during the hottest months. The plant itself has been proven advantageous for the desert soil, improving its quality and sustaining it. We have developed natural 25 shades in natural dyes, and offer a shade card to our collaborators for the same. This development came into operations in April of 2019.
- Design and produce mass-market clothing and apparel through circular processes
- Demonstrate business models for extending the lifetime of products
- Pilot
- New application of an existing technology
Our mission is to not just make a garment that is zero waste but to intervene and integrate circularity into the system of the textile industry. Our focus is to make well designed long lasting products that speak rawness in a refined creation.
We see "lowbrow" crafts through design.
We understand that integrating sustainability in one, isolated system is really not sustainable; therefore we collaborate with other businesses that share our values and help them go green.
The origin of weaving in India dates back more than 5000 years; a fragment of faded pink madder-dyed cloth was found in Indus Valley excavations and in Roman times Indian cottons and silks were exported in massive quantities. The trend continued for centuries until industrialization and demand for cheap mass-produced goods meant weaving skills were almost lost until a timely revival in ethnic and ethical products. We utilizef this age old craft with the spin of upcycling.
- Indigenous Knowledge
The growth plan would create employment opportunities in isolated rural villages of India because the fiber grows in the hottest of areas during the hottest of months. It would also create specialized income-generating opportunities for women. The brand concept itself is an opportunity to showcase India as not just a manufacturing hub but a design house that dates back to ancient times.
- Women & Girls
- Rural Residents
- Very Poor/Poor
- Low-Income
- Middle-Income
- India
- Japan
- Singapore
- France
- United Kingdom
- United States
- India
- Japan
- Singapore
- France
- United Kingdom
- United States
We started with 3 artisans and now have 27 artisans working with us. We have also organised women in Rural areas into self help groups who now have a steady income. This is a group of 10 women. In 5 years we are working towards attaching 500 artisans and 200 women from rural areas.
Our focus is to make well designed long lasting products that speak rawness in a refined creation.
We see "lowbrow" crafts through design.
We understand that integrating sustainability in one, isolated system is really not sustainable; therefore we collaborate with other businesses that share our values and help them go green.
We are also developing a fabric made from an alternative fibre called aakh that grows without water. We have researched and we know we can scale it up and develop the actual fabric. This fibre does not require any water to grow and grows as a wild plat in the hottest of areas and blooms during the hottest months. The plant itself has been proven advantageous for the desert soil, improving its quality and sustaining it. We have developed natural 25 shades in natural dyes, and offer a shade card to our collaborators for the same. This development came into operations in April of 2019.
Our mission is to establish IRO IRO as a global zero-waste fashion and lifestyle brand and design collective. Through our ongoing collaborations in upcycling, aakh and natural dyes and growing B2C presence and launch of our repair program, we expect to see considerable revenue growth in the next 2 years.
We are dependent on nature for all our raw materials except for waste. All our processes are done by hand which make them laborious.
Organisng work season wise
- For-Profit
we are a team of designers, museum professionals, artisans who have honed their crafts and have a passion to do it, and founders with a vision to carry and communicate that passion. We are a team of passionate individuals tempered by experienced team members. We have accesses to our own manufacturing facility which has been catering to the Japanese market famous for its notorious quality standards. It is a family run business whose founders have an industry experience of 30 years. We are committed to making fashion that is evocative, ethical and circular and we have strong foundations to execute on that commitment.
MATTER PRINTS
AKFD, jAIPUR
IRO IRO takes a collaborative approach to fashion. We have collaborated with a luxury heritage hotel, design houses based in Japan and Singapore, kids wear brand based in America, a very celebrated design studio from Jaipur. All these collaborations not only allowed us to use all our offcuts but also allowed us to use the waste other businesses were producing and help them go circular. It also gives our artisans and us an opportunity to keep redefining a refined fabric made from waste. We also cater IRO IRO original line B2B2C through concept stores and online stores.
We have seen a growth rate of 16% in our business in just one year.
1) sustainability is collaborative. 2) we are unique in our deliverables 3) the field of work is ever growing and competition will only boost innovation and lead to better problem solving 4) We provide unique Indian zero waste solutions relevant for modern aesthetics 5) We work with Indian crafts and artisans and integrate upcycling and revive traditions with innovations
Because it was suggested to us by our mentor
- Business model
- Distribution
- Funding and revenue model
- Media and speaking opportunities
Design houses
Fashion revolution
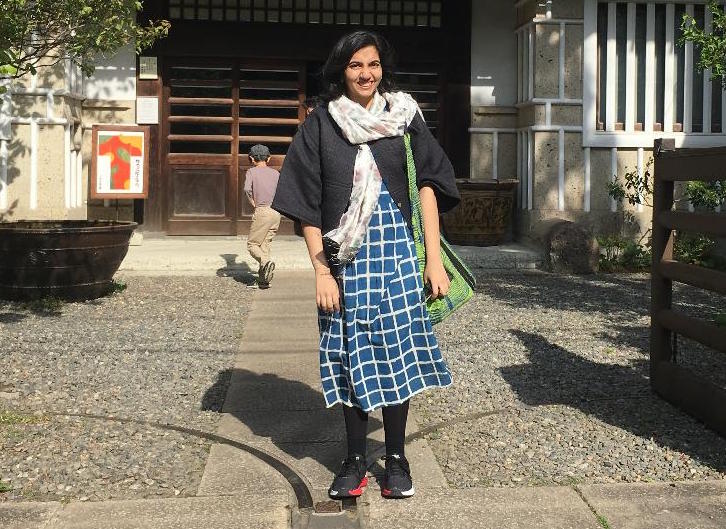