ECOACT TANZANIA
We are using a chemical free and energy conserving technology to recycle and transform post consumer plastic garbage and packaging materials into durable and long lasting plastic timbers, Plastic timbers are affordable alternative to wood timbers, hence reduces the need for building material manufactured from wood, helping to preserve forests, cut down on deforestation and further mitigation of climate change.
Every year more than 9 million tons of plastic garbage end up in our oceans causing threat to marine life, and by the year 2050 there could be more plastics than fish in the ocean, Plastic pollution doesn't just hurt marine species. It's also harmful to people. Practically solid waste management is one of the environmental problems that most African cities are struggling to manage. As the number of residents in most cities is increasing so is the production of solid waste. Very unfortunate, effective environmental and sustainable measures to manage the waste are lacking
On the other hand, Deforestation is a big problem, a 2017 report by the United Nations Food and Agriculture Organization (FAO) estimated that Earth's total forest area continues to decrease at about 13 million hectares per year. In our country we saw our forests are fast depleting, the growing demand for timber in building and construction activities was putting a lot of pressure on the country’s forests reserves and natural forests around Mount Kilimanjaro (Our country loses about 400,000 hectares of forest every year due to increase in building and construction activities.
We are targeting to impact more than 100,000 people who lives in slum ares in our country, these are people who will be giving us waste plastics on exchange with medical insurance for their families.
We have developed a chemical free, energy conserving plastic extrusion technology called “Waxy ӀӀ technology” to recycle and transform post consumer plastic garbage and packaging materials into durable and long lasting plastic timbers, Plastic timbers are affordable alternative to wood timbers, hence reduces the need for building material manufactured from wood, helping to preserve forests, cut down on deforestation and further mitigation of climate change. The plastic timbers which are ideal product for building, construction and furniture making are normally made in 10ft on average and shaped either round or square.
Our technology is environmental friendly, that uses natural profiled waxy ( from the bees) inversion in the plastic extrusion process set at different temperatures, the technology helps plastic materials of different polymers reach their melting point quickly while retaining their original stability and strength, hence low energy consumption resulting to low production costs, enabling production of plastic timber which are 32% less compared to price of wood timber, the technology converts more than 12 different types of plastics and packaging materials, producing durable, long lasting, termite resistant plastic timbers used in building and construction estimated to last more than 60 years without replacement whether used in sunny areas, marine or in water applications. We are simply pioneering the chemical free and energy conserving plastic extrusion technology in Africa.
- Demonstrate business models for extending the lifetime of products
- Enable recovery and recycling of complex products
- Pilot
- New technology
Normally the challenge with the plastic extrusion process is it takes time, which increases energy consumption and increases production costs, this situation has been a major challenge to many plastic extrusion facilities in different parts of the world, hence this has forced those facilities to use chemicals to speed up the extrusion process, these chemicals in turn pollutes the environment.
We have developed a chemical free, and energy conserving plastic extrusion technology called “Waxy ӀӀ technology” The technology solves both issues, it uses natural substance – natural profiled waxy (from the bees) which are inverted during the extrusion process set at different temperature, helping plastic materials of different polymers reach their melting point quickly while retaining their original stability and strength, hence low energy consumption resulting to low production costs. We are simply pioneering the chemical free and energy conserving plastic extrusion technology in Africa.
Our Plastic extrusion technology is environmental friendly, which uses natural profiled waxy ( from the bees) inverted in the plastic extrusion process set at different temperatures, the technology helps plastic materials of different polymers reach their melting point quickly while retaining their original stability and strength, hence low energy consumption resulting to low production costs, enabling production of plastic timber which are 32% less compared to price of wood timber, the technology converts more than 12 different types of plastics and packaging materials, producing durable, long lasting, termite resistant plastic timbers used in building and construction estimated to last more than 60 years without replacement whether used in sunny areas, marine or in water applications. The technology simply pioneers the chemical free and energy conserving plastic extrusion technology in Africa.
- Biomimicry
- Behavioral Design
There are numerous non-profits in Tanzania’s waste industry which quickly cease to exist once donor funding ends These initiatives have proved to be unsustainable. Our project permanently withdraws an item which is considered to be a waste and converts into a useful product which is highly on demand. This way we provide sanitation to slum areas where blocked drainage & sewers due to plastic is common, we employ locals in plastic waste collection where they earn US$ 5.75/day, we pay those employed in our plant at 1.3 times the average national wage. Being a for-profit social enterprise, we are economically sustainable through sales of plastic timbers. The market loves the plastic alternatives because they do not rot, are not effected by termites hence last longer, and are easy to work with as they can be cut, drilled and nailed just like timber.
- Peri-Urban Residents
- Very Poor/Poor
- Middle-Income
- Tanzania
- Kenya
- Uganda
- Tanzania
- Kenya
- Uganda
We are currently serving 134 clients, next year we expect to serve 500 clients and the next five years we expect to serve 10,000 clients.
- To improve our waste collection, we have launched "Garbage Medical Insurance" which is a micro health insurance program which uses garbage as a financial resource. With this program, the community and uninsured poor slum dwellers are able to pay for health cover, drugs and other clinical services by using garbage as payment to an insurance scheme.
- Currently we are seeking US$ 40,000 in financing to acquire high capacity technology (Shredding Machine & Extrude machine) capable of producing 200 plastic Lumber/day to be able to meet the current demand.
- We plan to push branding and sales efforts countrywide, to able to sell in our Country most of our products that we produce and the remaining to start to push to the regional markets in Kenya, Uganda, Rwanda and Southern Sudan.
- We will also introduce other applications for our plastic waste recycling technology to manufacture roofing tiles and pavements.
- Unavailable of enough waste plastics for production.
- Lack of market for our products:
- Competition from Timber
Unavailable of enough waste for production. Our capital city produces 3,800 metric tons of waste everyday of which 40% percent is plastic waste, meaning there will always be enough raw materials for production of plastic poles, because we cannot consume even 20 percent of what is available at the moment.
Lack of market for our products: We currently have more than potential 32 clients who are buying our products this includes government projects, construction companies and the national game reserves. However we plan to export to nearby countries like Uganda and Rwanda of which we are negotiating to get the agents.
Competition from Timber: Unlike timber plastic lumber, do not rot or absorb water and is highly resistant to insect damage, making it perfect also for marine and other water applications, It also eliminates the need to treat the lumber, unlike treated wood, which uses toxic chemicals to impart the same qualities that plastic naturally has.
- For-Profit
Our social enterprise is a for profit company.
15 Full time staffs and 26 part time staff.
- Mr. Bernard Ernest is the co- founder and Technical Director of EcoAct Tanzania who oversees all operations of the organization. He holds a 1st Class Honors, Master of Engineering degree in Biochemical from University College London. He has performed highly specialized design, research and analysis on plastic extrusion and refurbishing of machinery and has a strong track record in improving profitability and productivity.
- Mr. Christian Mwijage is the co founder and Managing Director of EcoAct Tanzania who oversees the overall operations of the company from production, quality assurance to sells and marketing, he holds a bachelor degree in Business Administration and Marketing from Washington University with business experience of 6 years.
- Madam, Elineca Ndowo is the co-Founder and EcoAct Tanzania Chief Finance Officer, She holds a Masters Degree in Project management and financing from the University of Daressalaam, with experience of five year working with local and international organizations in project financing.
- Baraka Zakaria is our Chief Strategist Officer. He holds a business degree from the University of Sheffield and brings his deep industry knowledge and great connections. He is involved in making key strategic plans for the organization and marketing.
- Mrs. Mariam Lameck, EcoAct Tanzania Advisor holds a Finance degree & a Masters of Business Administration from the United States International University. She carries out internal Auditing & Financial Analysis for EcoAct Tanzania.
We are partnered with Cocacola, Together with cocacola we organize the monthly beach cleanup, where we clean and collect the waste around the oceans. The plastic waste we collect we use them as raw material to manufacture plastic timbers i our factory.
Our Business Model involves designing, manufacturing and direct delivering and selling of plastic lumbers to real estate developers, advertising agencies, domestic home developers, telecommunication infrastructure contractors, road contractors, wildlife conservation agencies, farmers and the government.
We generate revenue by manufacturing and selling of plastic timbers that are used for building, construction as well as furniture making.
To access the network, resources and funding so as to scale our project and create a big impact.
- Business model
- Technology
- Funding and revenue model
- Monitoring and evaluation
- Other
Busniess Plan Review
Waste Management organizations and Machine manufacturers companies
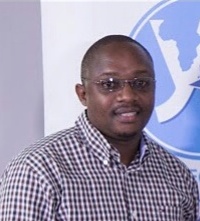