First Decarbonized TiO2 Plant
- Nigeria
- For-profit, including B-Corp or similar models
The chemical industry alone accounts for 2% of global carbon dioxide emissions. According to McKinsey, the industry's total carbon dioxide emissions was 925 million tonnes in 2021.
While the idea of mitigating these emissions by firing and powering chemical plants with renewable energy like solar seems exciting, the vast resource required, like land area required, to set up solar farms big enough to power the plants makes the idea impractical. Emphatically, the land area required to set up a solar farm big enough to generate sufficient energy to run a plant can run into multiples of the land area needed to erect the chemical plant itself. If you have ever seen a typical chemical plant, with its sheer size that can span hundreds of acres, you will easily appreciate the magnitude of this challenge - a fact that makes the chemical industry a hard-to-abate sector.
Paradoxically, Africa relies heavily on chemical imports, yet the individual markets for these chemicals on the continent are too fragmented for investment in large-scale domestic plants. But then this fragmentation presents a unique opportunity in the area of adaptable small-scale modular plants, which can be designed to cater to regional needs with minimal environmental footprint.
Titanium dioxide is one of the many products of the chemical industry that fits this paradox. The production of titanium dioxide alone results in the emission of over 24 million tonnes of carbon dioxide per annum. At the same time, purchasing titanium dioxide is challenge for the hundreds of paint manufacturers and other buyers of the chemical in Nigeria and West Africa due to lack of domestic production. They either have to pay exorbitant prices to importers or face challenges due to foreign exchange scarcity to buy the chemical directly from overseas manufacturers. For instance, based on a customer survey we conducted in September 2022, while the average global price of titanium dioxide was $3,000/tonne, Nigeria’s paint manufacturers pay an average of $9,850/tonne to buy the chemical.
Due to their smaller sizes compared to conventional large-scale chemical plants, small-scale modular plants can be fired and powered more easily with renewables. Accordingly, we are developing a modular chemical manufacturing platform to decarbonize the chemical industry, with a focus on Africa’s fragmented markets, bolstering the chemical supply chain on the continent in the process.
Our first will be a decarbonized titanium dioxide plant. Titanium dioxide, being a solid, is a chemical that can be easily produced in a compact modular plant via the chloride process. A conventional chloride-route titanium dioxide plant, on a feed-to-gate basis, emits 4 tonnes of carbon dioxide for every tonne of titanium dioxide produced.
Through prefeasibility studies, we have determined that suitable plant capacity for economic viability should be 20,000 to 50,000 tonnes/annum of titanium dioxide (the final plant capacity will be determined through bankable feasibility studies). By establishing a decarbonized titanium dioxide plant with a capacity in this range, we will be offsetting 80,000 to 200,000 tonnes per annum of carbon dioxide emissions. We will also be helping buyers access the chemical more easily and at lower cost in West Africa. We view the decarbonized titanium dioxide plant project as a model for Africa's industrialization with minimal or zero carbon footprint. A successful execution of this project will pave the way for replicating the model for other chemicals imported in fragments into the continent.
There are over 100 paint manufacturers in Nigeria who rely on import of titanium dioxide and pay exorbitantly for the chemical in Nigeria and West Africa. Other industrial users impacted by the complete dependency on import for titanium dioxide in West Africa include plastic manufacturers and ceramics producers.
With the product form our plant, they will pay less for the product and access it more easily.
We bring together the finest talents with the requisite experience and unwavering motivation, boasting a cumulative experience of over 25 years in process design, plant construction and operations, process safety, and electricity distribution infrastructure management. The CEO is a chemical engineer with 6 years’ experience in process design and synthesis and a doctorate degree in chemical engineering from a top STEM-focused institution in the U.S. (Purdue University) and holds 2 U.S. patents in process engineering. Our Director of Operations is also a chemical engineer with 6 years’ experience in the design, construction, commissioning, and operations of the largest refinery & petrochemical plant in Africa, the Dangote refinery. He is an assistant manager at the refinery, managing a team of more than 15 personnel at the refinery's Residue Fluid Catalytic Cracking (RFCC) unit. Yet another member of our team is a chemical engineer with 8 years’ vast experience in process safety engineering in oil and gas, railway, and renewable energy industries.
Our technical advisor, Deborah L. Grubbe, was formerly a corporate executive at DuPont and boasts over 25 years experience in the titanium dixoide business. She is also a chemical engineer and a member of the National Academy of Engineering. We are also blessed to have other esteemed technical advisors comprising renowned chemical engineering professors from Purdue university. Among them is Professor Jeffrey J. Siirola who boast over 39 years' experience in process research and retired as a technology fellow at Eastman Chemical Company and Professor Rakesh Agrawal who holds 131 U.S. patents and was a recipient of the National Medal of Technology and Innovation from former President Obama.
- Adapt cities to more extreme weather, including through climate-smart buildings, incorporating climate risk in infrastructure planning, and restoring regional ecosystems.
- 8. Decent Work and Economic Growth
- 9. Industry, Innovation, and Infrastructure
- 13. Climate Action
- Concept
We are in project preparation phase or conceptual planning phase, which entails carrying out feasibility studies to evaluate alternatives, economics and risks for the decarbonized titanium dioxide plant project prior to Detailed Engineering, Procurement and Construction.
We are looking to raise funding for feasibility studies, gain visibility and connect with the right people who can help us to succeed in the long haul.
Over the past 4 months, we have collected and studied 11 titanium dioxide mineral (raw material) samples from several locations across Nigeria. 3 of these samples have been identified to be promising, containing as high as 70% of titanium dioxide. A $10,000 grant from MIT Solve will assist us to study the promising samples and their locations further, and proceed to acquire mining lease from the Nigerian government. This would help us to demonstrate the raw material feasibility aspect of the project, and take us a step further in attracting investors.
- Financial (e.g. accounting practices, pitching to investors)
- Human Capital (e.g. sourcing talent, board development)
- Public Relations (e.g. branding/marketing strategy, social and global media)
We are solving decarbonization problem in a hard-to-abate sector using a simple approach that leverages the fragmented nature of Africa's chemical market. Our solution is able to address two problems at once: Minimizing global carbon footprint and promoting Africa's industrialization.
Moreso, the import of our solution can be likened to the role of electric cars in the automobile industry. It embodies a similar concept: a decarbonized modular chemical manufacturing platform tailored for the chemical industry.
The titanium dioxide that will be sold from our decarbonized plant to the West African market will replace imported ones from overseas which are produced in facilities that emits 4 kg of carbon dioxide for every kg of titanium dioxide produced. By selling from our plant to the market, we will be eliminating these carbon dioxide emissions. Additionally, domestic production in West Africa will eliminate carbon dioxide emissions associated with the shipping of the chemical across the sea to the region.
We aim to help Africa achieve industrialization with a minimal or zero carbon footprint, one chemical at a time. We are not just building a decarbonized titanium dioxide plant. We are establishing a model that can be replicated to easily build decarbonized modular plants for numerous other chemicals imported into the continent. Lessons from the decarbonized titanium dioxide plant project will be well documented for replication purposes.
Our impact will be measured by two metrics: The quantity of carbon emissions we mitigate, and the cumulative value added to the African economy.
Energy consumption in a chemical plant occurs through heat and power. In our decarbonized plant, we will be utilizing solar hydrogen, rather than fossil fuel, for heating. This solar hydrogen will be produced via water electrolysis by passing current from solar PV through water. The solar PV will also supply power to buildings, equipment and units that require electricity within the plant. Accordingly, the titanium dioxide plant will have an integrated solar farm with a power generation capacity of 35 to 88 MW.
- A new application of an existing technology
- Manufacturing Technology
- Nigeria
We currently have 6 people in our solution team: 4 process engineers, 1 process safety engineer, and 1 geologist.
2 are full time staff. 4 are part-time staff.
3 years
Our leadership team is diversified, comprising both male and female, and a person with disability. Members of our team also includes individuals from three ethnic groups in Nigeria.
As the team expands, we will continue to diversify our talent base to include individuals from different groups.
We will make money by selling titanium dioxide to paint manufacturers and other industrial users of the product in West Africa. Our product will help customers to cut down on the exorbitant price they currently pay for the chemical due to total reliance on importers for supply. Our product will offer customers opportunity to contribute to mitigation of carbon emissions, a they will be paying for a product with less carbon footprint compared to the imported counterparts. We will also generate revenue from the carbon credit market for the carbon mitigation achieved in our plant.
- Organizations (B2B)
We plan to secure funding for the plant's construction through a combination of equity and debt financing from investors, maintaining a debt/equity ratio of 2. The estimated capital requirement for the project ranges from $150 to $250 million. Our plant, like any other chemical manufacturing facility, will be meticulously designed to ensure profitability and facilitate swift returns for investors.
Prior to investors committing their funds to the project, our bankable feasibility studies must be concluded. These studies are imperative in confirming the plant's profitability, providing assurance to all stakeholders before investment decisions are made.
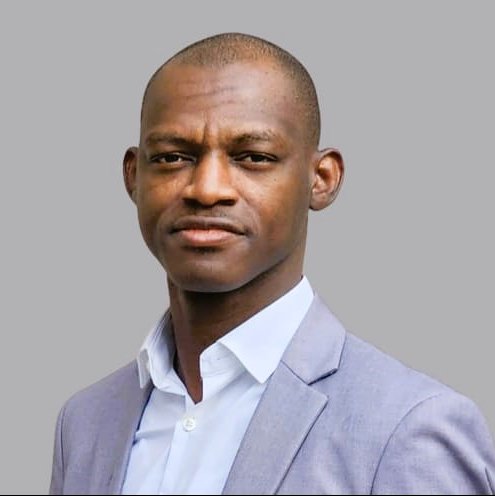
Founder & CEO