Chompix® - A Plastic Pre-Recycler
Chompix® (patented) is a novel, compact, automatic, easy-to-use plastic pre-recycling device that processes PET cups and bottles through cleaning, drying, shredding and compression into bricks.
Approximately 50 percent of plastics are used for single-use disposable purposes. Apart from this, a major portion of plastics are disposed within a year of manufacture. This shows that the present usage of plastics is not sustainable. Most plastics are not bio-degradable and take a long time – almost 450 years to decompose, leading to accumulation in landfills and as debris in the natural environment. Recycling plastics reduces the oil usage and carbon dioxide emissions during the manufacturing of plastics. There is a need for a compact, portable device that can aid this at the source and can find a place in restaurants, parks and coffee bars.
Chompix® is an easy-to-use plastic recycling device that aids the process of recycling by making blocks out of the everyday used PET cups and bottles through the process of cleaning, drying, shredding & compressing the plastic. These can further be used to make new plastic products directly in a recycling plant.
The construction of the Plastic Recycler is mainly done using sheet metal.
The main components used in the design are listed below.
- Outer Drum
- Inner Drum
- Shredder
- Conveyer belt assembly
- Compressor
Fig 1. Workflow of the proposed system
Chompix® is a Plastic Pre-Recycler. It is an automatic machine that can be placed in any public place for people to use. The working of the Plastic Recycler can be explained using 4 main steps - Cleaning, Drying, Shredding, and then Shaping. The used PET bottles of packaged water or soft drinks are fed into the machine in the input area. These bottles will then be cleaned with soap and water, clearing any kind of leftovers inside them. Then it is dried using hot air. These clean and dry bottles are then put into the shredder process, to shred. The shredded pieces of plastic are then shaped into a brick by compressing.
Chompix®, a novel, compact, automatic and portable device is the size of a big dustbin. This design is based on 3 years of product & market research with inputs from cafes like Coffee Day, Starbucks, Barista and several others. It has been designed to address the plastic recycling problem. This device can be used at restaurants, railway stations and other public places where a lot of plastic is consumed daily. This can help at the source by minimizing the hazards caused by plastic pollution and the challenges faced by regulatory bodies in handling this issue by tackling it at the source creating plastic bricks that can be directly used for recycling or upcycling into useful products. This innovation is aligned to the United Nations SDGs. Talks are going on with an interested manufacturing company and NGO in placing this device across cafes.
Having done my early education in a Jiddu Krishnamurti school which is on 100 acres of man-made forest, whenever I see greenery being taken over by garbage, I want to do something about it. This has led me to create a device that can assist in the plastic accumulation problem – Chompix® working since March 2020, along with Project Starfish, an MIT startup exchange organization under the mentorship of M r.Subhasish Acharya, an Harvard alumnus. Chompix not only helps nature but also contributes to everyone’s health indirectly, both of which will work in the direction of the urgency in change. We will be shortly partnering with a waste management company that will manufacture Chompix® and place them in cafes as well as upcycle the output plastic bricks into useful products. An interested NGO is also interested in partnering to collect the plastic bricks and maintain the device.
Chompix® is based on 3 years of product & market research with inputs from cafes like Coffee Day, Starbucks, Barista and several others. It has undergone several rounds of iteration through feedback and improvisation before arriving at the final design. We will be shortly partnering with a waste management company that has been doing a lot of work on upcycling plastic waste into useful products and an NGO that has been engaged in creating a clean environment.
- Taking action to combat climate change and its impacts (Sustainability)
- Concept: An idea being explored for its feasibility to build a product, service, or business model based on that idea.
We are designing a vertical standing system that cleans, dries, shreds and creates a block of plastic that can be further taken to the factory for reusing by employing additional manufacturing processes. This will be a fully automatic system that will be assisted by a timing circuit that controls the motor movements and activation of various parts of the system. While there are systems available at the industrial level, there is a need for a compact and automatic device that can be placed at coffee bars, parks and restaurants. Also, although there are similar bigger systems available that crush the bottles and shred them, it becomes difficult to transport this shredded plastic as they have to be packed in a separate bag manually. Our proposed solution tries to solve this issue by creating blocks of plastic that are easy to carry around and transport.
Chompix® aims to make a significant impact on the recycling industry. It will increase efficiency and reduce costs. This innovative design of a compact and mobile plastic pre-recycling device will make a significant impact in our community by promoting sustainable living and reducing plastic wastes in our parks and cafes. All this will be done by reducing the plastic waste accumulation by tackling and pre processing at the source as well as transportation to the recycling plant and subsequent upcycling.
The proposed system has the shape of a vending machine. Its overall dimensions are 1.3m x 1m x 2m (L x B x H) including all the attachments. The machine has an input area where people can put the used plastic cups for processing. The input area is covered by a transparent plastic door. The person can put the cups on the rod by opening the door. After the cups are placed, the person can activate the machine by pressing the start button. This will start the machine and the process begins. The rods are part of the outer drum. This outer drum is rotated by a motor that is controlled by the timer circuit. This motor aligns the rods with the holes on the inner drum. After the holes are aligned with the rod, a pump is activated which is positioned inside the inner drum. This pump will spray water from the holes, through the rod, and into the plastic cups. The rods have holes at various locations and so will help clean the cups. Slot holes have been made on the drums so that the water from the bottle drains back into the inner drum. The raised portions around the rods will prevent any leakage. The pump will be on for a specific time, controlled by the timer circuit. After the cleaning, the motor rotates the outer drum to make the rods vertical. This will help in draining out all the water inside the water. At this position, another set of holes on the inner drum is aligned with the rods on the outer drum. This activates the hot air blowers. The hot air is blown through the rods to help dry the cups completely. The rotation of the motors and activation of the hot air blowers is controlled using programmed circuits. After the cups are dried, the outer drum rotates and goes back to its initial position in the input area. During this rotation, the cups fall into the hopper of the shredder due to gravity. This activates the shredder motors. The cutting blades of the shredder pull the cups in and shred them into tiny pieces. The activation of the shredder motors also activates the motor for the conveyor belt. The shredded pieces of plastic are collected by the conveyor belt and dropped into the collector box. The motor of the conveyor only stops a few seconds later, after the shredder motor stops. The collector box collects all the shredded plastic and when it's filled, the compressor which is powered compresses the plastic. After this using a sensor, the bottom of the receptacle is moved and the compressed block falls down. The compressed cube falls into the storage.
Proposed Methodology
Fig 2. Inner and outer Drum description
The first process of recycling plastic is by cleaning it. For this, we have designed a rolling drum system. The rolling drum has 2 concentric drums - The inner drum and the outer drum. The inner drum is fixed while the outer drum rotates around it. The outer drum has 6 rods - a set of 3 rods each separated by 180 deg. At a given time, a set of 3 rods will be stationed at the input area. The input area is where people can put the cups. 3 cups can be put on the 3 rods. The rods have holes in them so that water can be sprayed through them for cleaning the cups. The length and spacing between the rods have been made considering the plastic cup dimensions. At a time, 3 such cups can be easily placed on the rods. There are two slots provided beside the rod so that the water that drains back from the cup goes back to the partition with water, which is present inside the inner drum. The slots are surrounded by a raised portion that will prevent water from leaking into other places. This outer drum will be connected to a motor and controlled using the sensors. The inner drum is fixed to the enclosure walls. Inside the inner drum is a separate partition that has a pump for spraying water and a container for water. On the other partition, we have attached hair dryers that will blow hot air to dry the cups. There are two slot holes to allow water to flow from the outer drum to the water container partition in the inner drum. There are rubber panels that will prevent water from leaking inside the inner drum.
The next step after cleaning and drying is shredding the cups. For this, we have created a shredder assembly that has a hopper to intake the cups. Below the hopper are two sharp-edged circular cutting blades. They are controlled by a powerful motor thus enabling the shredding of the plastics. As per the arrangement of the drum assembly and the shredder assembly, there was a lot of space being left out. To occupy those spaces and make the final device as compact as possible, we are making use of the conveyor belt. The shredded plastic will be collected by the conveyor belt and dropped into the shaping box.
Electronic components
Design considerations and adequate safety factor has been included while selecting components. The electrical components required to drive the entire system are listed below.
- Water pump
- Shredder motor
- Motor For Outer Drum
- Motor for conveyor belt
This system will run on a single-phase 240V supply and so can be connected to any normal power source. There are provisions for changing the water for cleaning and removing the plastic blocks from the storage box. The system is fully armed with sensors and timing circuits.
- Manufacturing Technology
- India
- United States
We expect to serve multiple cafes in the next year. This will work with a tie-up with a company that is both into manufacturing machines and upcycling of plastic waste. They will be assisted by an NGO that will help in the placement of Chompix® across multiple cafes, maintain the device and collect the plastic bricks to their waste management partner for recycling. This will result in impacting a great section of the city where a lot of plastic gets accumulated on a daily basis and bring about efficiency in addressing the plastic waste from the source to upcycled products.
The interested manufacturing company will have to invest time and money to bring out a working prototype of Chompix® and there will be technical challenges in this direction and testing before it can enter the market.
Currently the inventor of the Chompix® design, Neeraj Nagaraj works along with Project Starfish, an MIT startup exchange organization, mentored by Mr.Subhasish Acharya, an Harvard University alumnus.
Chompix®, patented in India and provisionally patented in US plans to partner with a waste management company and an environmentally agile NGO shortly.
Cost:
- Initial investment by the manufacturing company that is also into upcycling of plastic waste
- Subsequent profit from the sale of the upcycled plastic waste into useful products to feed into the purchase of plastic bricks from the cafes
- Placement of Chompix, maintenance, collection and transport of plastic bricks to be done by a voluntary, non-profit NGO
- Cafes will need to purchase Chompix
- Subsequent profit from the sale of the useful products created from the upcycled plastic waste to feed into the purchase of plastic bricks from the cafes
- Cafes will sell the output plastic bricks to our upcycling partner which will cover the expenses of the device over time leading to profit
Revenue Streams:
- Subsequent profit from the sale of the useful products created from the upcycled plastic waste to feed into the purchase of plastic bricks from the cafes
- Cafes will sell the output plastic bricks to our upcycling partner which will cover the expenses of the device over time leading to profit
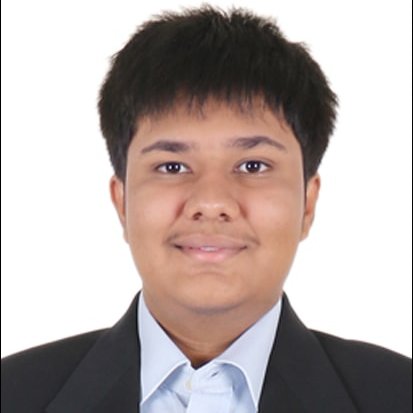
Design Engineer