MycoTile Panels
Wall and roof insulation panels made of agricultural waste (sugar bagasse, coffee husks, and corn cobs), bonded organically with oyster mushroom mycelium.
Solution Pitch
The Problem
Kenya has an annual housing demand of 250,000 units with an estimated supply of just 50,000, leaving an 80% deficit. Hundreds of thousands live in informal housing to cover this deficit.
The Solution
MycoTile offers a high performance and cheaper alternative to traditional building materials. A carbon negative process is used to bond agricultural waste (such as maize cobs, coffee husks, coconut coir and rice husks) with mushroom mycelium to create a building material composite. The pilot product is wall and roof insulation, which have superior acoustic performance and fire-retardant properties compared to the available alternatives. The fire-retardancy is naturally enhanced by the chitin present in mycelium. MycoTile intends to prototype a larger portfolio of products, such as ceiling tiles, construction blocks, MDF-style panels and furniture. An important growth step was the conclusion of a co-manufacturing contract with a Kenya government entity. MycoTile is establishing partnerships with small scale farmers, who are compensated for providing agricultural waste, to assure security of raw material supply.
Stats
There are currently 28 contracted farmers and locals who package agricultural waste for MycoTiles and six non-contracted suppliers of agricultural waste.
Since the product has not been installed on a large scale, the benefits of the product in housing are yet to be documented.
One metric ton of waste has been reduced through reduction, recycling, and reuse so far, with the aim of upcycling hundreds of tons of agri-waste once production is rolled out.
Market Opportunity
Our pilot market is retrofitting informal settlements with thin-walled housing. Nairobi houses 2.5 million in these informal settlements with an assumed 10SQM of walling per person. This is a $150 million market in Nairobi alone. This does not include offices and roof insulation.
Organization Highlights
Partnered with the Kenya Government through Kenya Industrial Research and Development Institute (KIRDI) for consultancy services in mycology and space and facility for co-manufacturing.
Implementing partners of Challenge Fund for Youth Employment through Habitat for Humanity Kenya and Netherlands.
Partnership Goals
MycoTile Panels seeks:
Expertise on product management / review of a product roadmap
Expertise on accounting and financial reporting
Technological expertise in testing products for fire, heat, acoustics and life cycle analysis to prepare a standard and specification sheet
Financial partnership that will help grow out of government partnership and build internal production set-up
Imagine a tough, fire-resistant building material that could simply grow from a combination of mushrooms on agricultural waste. In Kenya, most construction materials are imported, and for this reason are relatively expensive and often simply not the best quality. The country has an annual housing demand of 250,000 units with an estimated supply of just 50,000, leaving an 80% deficit. This deficit will not be met using traditional building material or importation of materials. At the same time, there are local natural resources whose potential application in construction is largely untapped. One is agricultural waste produced by small-scale farmers. Another is mycelium, a natural fungal material with industrial-level strength.
MycoTile offers a high performance and cheaper alternative to traditional building materials. We use a carbon negative process to bond agricultural waste (such as maize cobs, coffee husks, coconut coir and rice husks) with mushroom mycelium. The product is denatured through heat treatment in order to inhibit mycelium growth. Our first product is wall and roof insulation, which have superior acoustic performance and fire-retardant properties compared to the available alternatives. The fire-retardancy is naturally enhanced by the chitin present in mycelium.
We intend to prototype a larger portfolio of products, such as ceiling tiles, construction blocks, MDF-style panels and even furniture. Although the major challenge has been changing public perception on the use of mycelium in construction, we currently have more demand than they can supply. A recent important step in our growth was the conclusion of a co-manufacturing contract with a government entity. We are establishing partnerships with small scale farmers, who we pay for agricultural waste, to assure security of raw material supply.
Our insulation panels, though can be used in commercial projects, target thin walled structures, especially those done in tin metal sheets that house urban population but with inhabitable indoor climates. Our affordable and inert insulation will help regulate the indoor temperatures of these homes and encourage more builds to meet the housing deficient.
We are also adding income to small scale farmers who sell their waste to us that would otherwise be left to rot.
With our continued research, our revolutionary building block will be solving the mountains of sugar bagasse found in large scale in sugar milling factories in western Kenya where they have become a challenge to the factory and the environment of the surrounding community at large.
Nairobi is home to some of the largest informal settlements in the continent with makeshift thin tin walled structures. With our product we vision the potential of creating decent and habitable spaces without breaking the bank and with raw materials that are available in abundance across the country, highly renewable and completely compostable at the end of the building life.
There is rapid movement towards embracing green product, with the Kenya government specifically investing in both affordable housing and local manufacturing as two of the Big 4 agenda of the current government.
- Enable mass production of inexpensive and low-carbon housing, including changes to design, materials, and construction methods.
- Pilot
MycoTile is looking for strategic partnership to advance its testing of the product and scale to a minimum viable product. Locally, analysis of the product has been challenging with no standards to guide us but having to create our own standards.
Aggressive marketing and uptake of the is required to create a shift from conservative building technologies that are not willing to accommodate alternative materials.
- Human Capital (e.g. sourcing talent, board development, etc.)
Our solution is completely organic and the building material is grown as opposed to be manufactured. We have zero waste with all the defective products moved back in the production line for a fresh start.
Our product is affordable but more appropriate because our vision is to create a portfolio of products that will cover floor, walls and ceilings significantly reducing the cost of building and making homes more affordable and accessible to all.
We intend to be fully rolled out in the market in the next year with at least 50 employees and youth entrepreneurs who collect and package our wastes.
We have established partnerships in villages across Kenya and with Sugar millers that provide their waste at no cost, as we are solving their problem, to help us grow faster and meet our targets.
We also have partnerships with Architects including MASS Design Group, BuildX studio and Cave Ltd, to name a few, who are our early adopter in waiting and channels to create the shift in perception as they are thought leaders in the industry.
We take opportunity to exhibit our work to wide range of audience with our latest being the exhibition starting this May at the Barbican Centre Our Time on Earth
- Productive and decent employment measures using ILO standards.
- Equivalent carbon credits in our production process.
- Tonnage of waste converted to building material.
- Number of retrofitted informal houses in Nairobi.
- No of youths and women employed.
Our affordable solution looks at a wholesome growing of building materials as an alternative to traditional brick and mortar.
We imagine multiple products using the same process of production to tackle the shortage of building materials and housing in general in the continent using resources that a readily available and technology that is accessible to all.
Sterilized substrate constituents are inoculated with fungal spawn (mycelium) to achieve the initial growth. A growth media (sugar bagasse) is applied into an enclosure/mold which represent the final geometry of the desired product. Mycelia from the inoculated substrate is allowed to grow through the substrate in a controlled incubation chamber, to bond bulky particles while consuming the allotted nutrients. The fully bonded panel is removed from the enclosure/mold and rendered inert by killing the fungus through dehydration. Finally, the panel is completed by post-processing to obtain a good surface finish.
The composition of the panel is as below;
1. Sugarcane bagasse 70%
2. Bamboo sawdust 10%
3. Rice husk 10%
4. Wheat bran 5%
5. Calcium carbonate 2%
6. Gypsum 2%
The MycoTile Insulation Panel is used a building wall and roof insulation being sandwiched by either tin or plywood boards to moderate indoor temperatures.
The edible oyster mushroom mycelium is used to bond the agricultural waste and the product is neither hazardous nor has it any recorded allergic reactions from users.
- A new application of an existing technology
- Biotechnology / Bioengineering
- Manufacturing Technology
- Materials Science
- 5. Gender Equality
- 8. Decent Work and Economic Growth
- 9. Industry, Innovation, and Infrastructure
- 10. Reduced Inequalities
- 11. Sustainable Cities and Communities
- 12. Responsible Consumption and Production
- 13. Climate Action
- 15. Life on Land
- For-profit, including B-Corp or similar models
Our leadership team is all made up of youths under 35 years and below. We endeavor to create decent working environment with 30% women targets in our waste processing stations.
We have to channels for our business model. A B2B and B2C.
In our B2B model we intend to sell to suppliers of building materials who stock our product to sell to the market. It this model we market our products as samples to Architects and Engineers who specify our products in their projects to be sourced from the selected suppliers.
Our B2C is aimed at selling directly to homeowners a common building process in Nairobi where homeowners build their own houses. In this process we demonstrate our product with show homes that can be tested to create a perception shift and acceptance of the new technology
- Individual consumers or stakeholders (B2C)
Our goal is to be selling our products and ploughing back profits to invest in expansion and research.
With our abundant raw material we project production cost of $2.32 and selling the product at $6.00 which is still below the cheapest and low quality available insulation panels in the Kenyan market
We received seed funding from ShelterTech Accelerator Program and just signed a Youth Challenge Fund Contract with Habitat for Humanity Nederland.
However, our aim is to be independently selling our products and ploughing back profits
Organization Type: For-profit, including B-Corp or similar models
Headquarters: Nairobi, Kenya
Stage: Pilot
Working In: Kenya
Current Employees: 12
Solution Website: https://mycotile.co/
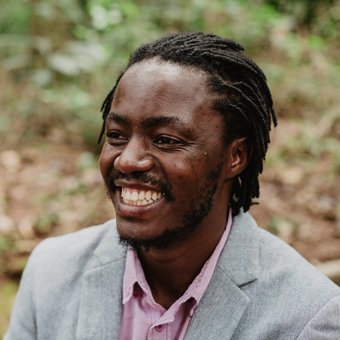
CEO