Tridealhouse Urban Farming Solution
Urban slum poverty is one of the world’s most persistent problems. The poorest billion people lack decent shelter, proper sanitation, jobs and food. They cannot afford any house. Tridealhouse is a self-financing, modular, triangular house with urban farming in hydroponic gutters on the sides and micro-livestock at the back. Tridealhouse breaks the poverty cycle by creating a micro-job and by increasing supply of nutritious food for own consumption and resale. Tridealhouse repays itself through farming revenues, rent-savings and sustainable utilities.
Tridealhouse is made of steel profiles and pre-cast composite concrete elements. It collects rainwater in 18 m3 foundation tanks. It generates solar thermal and PV energy. It is designed to last 50 to 80 years with minimum maintenance.
Tridealhouse generates economic activity, growth and increases GDP. This compensates for the inflationary effect of providing housing loans. Therefore, it can be scaled globally to help solve urban slum poverty.
Globally, over 1 billion people live in urban slums today and this number will increase by 2050. In Africa alone 300 million people live in slums. With 3.15 persons per slum family there is a need for about 95 million decent houses for these urban poor in Africa.
The day-to-day challenges of people in slums are interconnected and related to 12 of the 17 SDG. The lack of jobs creates poverty and perpetuates social problems. There is insufficient access to water. Lack of private sanitation increases diarrheal diseases and puts women's safety at risk. Food related costs expend 50%-80% of the income. Slum inhabitants pay average rents of ~20$/month. Domestic fuel constitutes 20%-40% of expenditures. The use of charcoal and firewood creates indoor pollution and health hazards. Women, children, and elderly are especially vulnerable. Elderly have no pension and no food security.
People in slums are too poor to acquire any house. Some countries have social housing projects, but these cannot meet more than a few percentage of the urban slum needs.
Our scalable and sustainable solution to this global urban slum poverty is to create a house that repays itself and fulfills 12 of 17 SDG needs: the Tridealhouse.
Tridealhouse is an ideal triangular house for happy living, urban food production and sustainable utilities to help solve urban slum poverty
Tridealhouse collects rainwater in 18m3 foundation tanks during the rainy season for use in the dry season. Nutritious food is grown in hydroponic gutters on the sides of the triangular house. Micro-livestock is raised at the back. Tridealhouse creates a micro-job and provides 50$-90$/month incomes through resale of food. Private sanitation safely processes the sludge, decreases diarrheal disease incidence, and provides a safe toilet to women. Solar PV provides electricity. Solar thermal collectors on the top reduces household use of charcoal by 30%-60%.
Tridealhouse components are manufactured 75% from local raw materials, such as composite concrete panels using cement. This reduces the need for foreign currency. The 25% imported materials are PVC gutters, adapted steel profiles and OEM solutions.
Once mass-production lowers the price to 12,000$/Tridealhouse, even the poorest slum families can afford to repay a Tridealhouse in 10-15 years by urban farming incomes and saved costs. Then the solution can be scaled globally.
To succeed, Tridealhouse cooperates with 5 stakeholders/partners: 1)Government, 2)UN, 3)Universities, 4)Industry and 5)impact investors/foundations.
A 1/3 scale prototype was presented at the UN-Habitat Assembly: https://www.facebook.com/tridealhouse/
Our solution targets urban slum inhabitants. We worked >50 years with 15 UN organizations and integrated relevant validated know-how and best practices in the fields of urban poverty mitigation.
We engage the urban poor by fulfilling their 12 SDG needs:
Impact on SDG nr.:
1- 50$-90 $ per month extra income in local currency
2- 40%-60% of nutrition needs of average family (including children) fulfilled
3. 30%-70% decrease of diarrheal disease, safer private toilets
5. 40%-66% of woman living in TH feel empowered
6. 50%-75% farming water needs met. 40%-60% family water needs met
7. 30%-60% less need for charcoal. Led light 2-4 hours per evening
8. 50% micro-job on the house for 1 household member
10. 40%-66% of elderly feel empowered
11. local urban food trade of 500$-1000$ PPP per year
12. 30%-60% of community food needs fulfilled by local production
13. Hurricane and flood resistance
17. Uniting cross-sectoral partners to solve slum poverty
We work with the Ethiopian Ministry of Innovation and the main technical university in Addis Ababa in the prototype phase to evaluate 5 Tridealhouses we are building from August to November 2020. Moreover, 20 slum households will live in 20 houses we will build early 2021 for testing, monitoring and evaluation before scaling up.
- Other
Lack of food, jobs, income, and poor health are major challenges in urban slums. These problems can only be sustainably solved by empowering people to lift themselves out of poverty with houses that finance themselves and provide jobs.
Tridealhouse urban farming solution grows nutritious foods and raises micro-livestock. It addresses the Solve food and poverty challenge for urban slums. At the same time Tridealhouse fulfills 12 of 17 SDG for the urban poor.
Tridealhouse generates economic activity, growth and increases GDP. This compensates for the inflationary effect of providing housing loans. Therefore, Tridealhouse can be financed locally and scaled globally.
- Prototype: A venture or organization building and testing its product, service, or business model
- A new application of an existing technology
Our solution is innovative in five dimensions
1) Product:
Tridealhouse is a sustainable and climate-resilient house that finances itself by own food production. It is expected to cost 12,000$ at mass production. Social housing in developing countries cost 15 to 20,000$, and do not address other SDG. Other low cost housing such as EmpowerShaks, Ketto, Pop-Up House, Volks.house, SHouse, BloomingBamboo, BetterShelter etc., do not collect water nor have urban farming or other SDG components. Tridealhouse integrates 12 SDG dimensions and has no global alternative for the moment.
2) Materials and OEM solutions
We develop or adapt technologies to use as much local raw materials as possible to limit foreign currency restrictions. We select appropriate OEM solutions/partnerships that can be mass-manufactured either at very low cost and/or in local joint ventures
3) Partnerships: we partner with 5 types of stakeholders: 1)Government, 2)UN, 3)Universities, 4)Industry and 5)impact investors/foundations
4) Collaborative humanitarian-industrial factory setup:
Together with industrial partners we source components with optimal quality/price preferably in joint-ventures. The industrial partner shares production and management know-how and can sell the products on the regular market. Tridealhouse gets access to OEM components at lowest cost and contributes to higher production volumes.
Each factory will have a training center so that we can hire and train slum dwellers to become co-workers.
5) Best practices and research driven
Every single component/function/solution is based on best practices of UN and development agencies. We combine this with technical or materials solutions we find in research papers and/or obtain from industry partners
1. Concrete composites: we co-developed and co-own technology of concrete composites combining foam, ultrastrong and CSA concrete types.
2. Hydroponic gutters with double layering protect the plant roots from the tropical heat. Initially imported and in PVC, we will cooperate with our OEM partner to make these gutters locally
3. Durable Magnelis steel profiles adapted to resist strongest hurricanes (eg. Mozambique/Philippines)
4. Water tank foundation in foam/superstrong concrete composite
5. Basalt fibres based panels for cladding are humidity and temperature resistant
6. Foam concrete side walls panels are covered with an impermeable thin layer of super-strong concrete. These provide acoustic and thermal insulation and fire-resistance
7. Optimal plant mixes selected in cooperation with local and international agricultural research and UN partners for most nutritious outcomes
8. Hybrid thermal and PV solar combination on top to cook, produce sanitary hot water and extra electricity
9. Community development and social engineering. Hamlets consist of ~50 Tridealhouses on concrete 1-storey levels built around one enclosed multifunctional courtyard with shared facilities. This will include space for chickens and goats, a washing area, fruit trees, a playground, and micro-business spaces.
10. Local financing scalability. Houses can be repaid fully in 10 to 15 years. As the house increases GDP, giving housing loans in local currency will not trigger inflation.
11. 80-years durability in tropical climate with high durability and minimum maintenance costs.
12. OEM solutions. We select appropriate OEM solutions/partnerships that can be manufactured locally at low cost and/or in local joint ventures
Co-founder Dr Loots has worked with 15 UN agencies the last 25 years for best practices and knowledge transfer via his NGO www.humaninfo.org. All selected technologies of Tridealhouse are based on best practices and transformed into products in cooperation with R&D and industrial partners in Europe and Ethiopia
1. Concrete composites: https://machinebouw.be/blog/value-ash-technology/
2. Hydroponic gutters: with our partner https://goponic.fr/
3. Durable Magnelis steel profiles : with our partner https://www.voestalpine.com/sadef/en based on Belgian research center for metals https://www.ocas.be/activities/materials-for-the-future-2/ that co-developed the Magnelis steel with the Belgium Arcelormittal factory https://belgium.arcelormittal.com/innovatie/productinnovatie/magnelis/
4. Water tank foundation combining ultrastrong, ultrathin concrete and foam concrete
www.valueash.com /Flame
Ultrathin concrete presentation to State Minister of Innovation, Ethiopia
5. Basalt fibers based composite panels : our Ethiopian partner Ministry of Innovation is developing basalt factories, from which we will source basalt fibers and basalt wool
6. Foam concrete side walls panels ; in cooperation with our UK partner https://www.eabassoc.co.uk/Foamed-Concrete-Block-Cutting-Machine.php
7. Optimal horticulture mixes in cooperation with www.FAO.org for which Dr MIchel Loots has been knowledge transfer partner for 6 years. Sourcing seeds from a long time contact ECHO https://www.echocommunity.org/en/pages/echo_global_seedbank_info
8. Hybrid thermal and PV solar combination in cooperation with www.energyville.be and German solar cooking NGO http://www.solarglobal-ev.de/projekte.html
9. Community development and social engineering in cooperation with our Addis Ababa Science and Technical University partner.
10. OEM Solutions: For every components, ranging from the toilet solution, oxygenation of the gutters or inside cladding, we will strive to cooperate with existing manufacturer for technology transfer or low-cost/ high-quality OEM production/cooperation
- Manufacturing Technology
- Materials Science
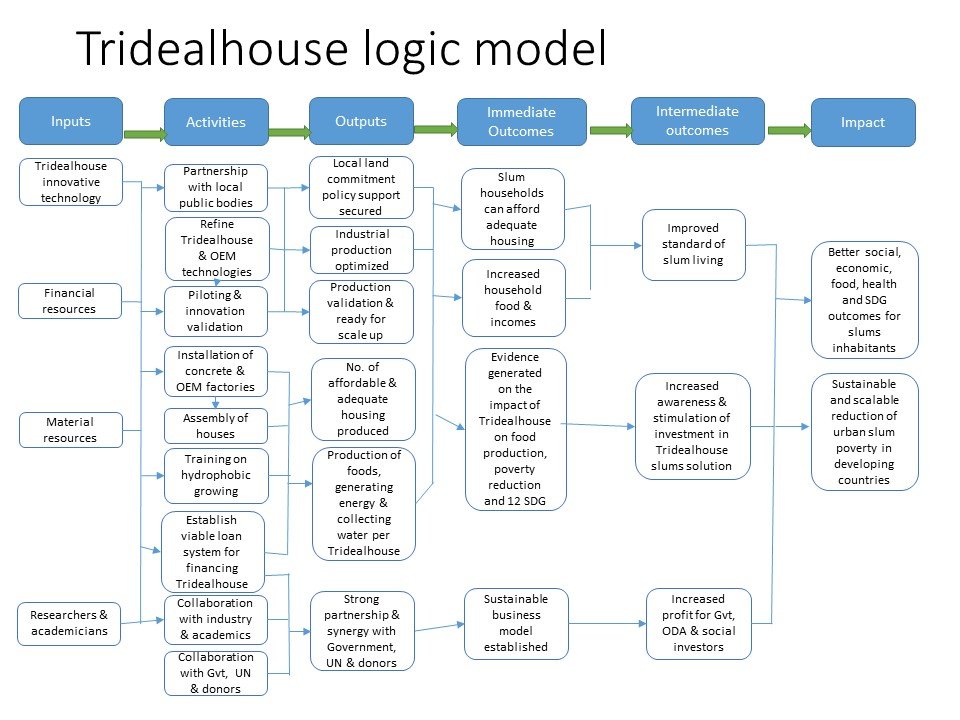
Our strategy focuses on partnership building, piloting and expansion.
We established excellent partnership with the government of Ethiopia and signed MoU with commitment to deliver the necessary local support and resources. We secured financing for prototyping and piloting from Happel Foundation. Moreover, IFC and EIB indicated their interest to collaborate for financing the expansion phase including factory set up and establishing mortgage system once phase 1 and phase 2 Tridealhouses are built and validated.
Based on learning from the piloting phase, in collaboration with research & academics both in Ethiopia and Europe, we will expand our implementation in 2021 by developing a factory and start local manufacturing and assembly of the houses, on land plots provided by the government.
In Ethiopia, we collaborate with the Federal Ministry of Agriculture and urban agriculture office in the city of Addis Ababa. We will provide on-site training on hydroponic growing, supply of urban agro-inputs and market linkages with local vegetable outlets.
In Europe, we collaborate with the major research institute in Belgium, VITO, and 4 Belgian (Antwerpen, Leuven, Gent, Hasselt) and 1 German (Aachen) universities.
Our target is to produce 2000 to 10,000 affordable houses for slum households per year in our own factory. The houses will provide living space, proper sanitation, rain water collection tanker underneath and hydroponic fresh vegetables growing structures equivalent to a garden of 90m2
At the same time we will develop our factory as a model factory both in terms of inclusion and training of slum inhabitants as co-workers, as in usage of local materials, as in integrating best practices from industry, UN and research institutes. That model factory can then be replicated in other countries.
The goal is to enable slum inhabitants worldwide to become food-self-sufficient, reduce malnutrition, disease and social exclusion. Tridealhouse seeks to address the interrelated problems of people in slums through multi-purposed house which provides food, job and income for each household.
We will regularly validate our business model and refine our domestic expansion and international scale-out strategy.
- Women & Girls
- Infants
- Children & Adolescents
- Elderly
- Peri-Urban
- Urban
- Poor
- 1. No Poverty
- 2. Zero Hunger
- 3. Good Health and Well-Being
- 5. Gender Equality
- 6. Clean Water and Sanitation
- 7. Affordable and Clean Energy
- 8. Decent Work and Economic Growth
- 9. Industry, Innovation, and Infrastructure
- 10. Reduced Inequalities
- 11. Sustainable Cities and Communities
- 12. Responsible Consumption and Production
- 13. Climate Action
- 17. Partnerships for the Goals
- Belgium
- Ethiopia
- Belgium
- Ethiopia
Currently, we are at the prototyping and piloting phase of 5 units that are being built from June till October 2020. From November to February we will build 20 Tridealhouses in which 20 slum families or 63 people will live.
1 year. Our plan is to build 1,000 units of Tridealhouse by the end of 2021 to benefit over 3,150 inhabitants. This will be done with the Ethiopian Government. A MOU is in place to support this.
5 years. we aim to have built more than 100,000 Units by 2025 in three factories. This will allow us to reach around 315,000 people directly. More than 1 million people to benefit from supply of fresh vegetables in the city.
5 years if factories are replicated.
By 2022, we expect to have all optimal production and OEM sourcing of low-cost/ high-quality components in place. We will produce 10.000 Tridealhouses per year in a model factory that can be replicated. Once the factories are replicated in other countries in cooperation with major stakeholders, then multiples of 10.000 Tridealhouses per year, lifting 33,000 families from poverty, can be provided per year per factory. European Investment Bank and World Bank country offices in Ethiopia informally indicated that if our solution is validated the next year, financing more factories from 2022 to 2023 would be possible. If we include other types of investors, then, 50 factories could be built, and 500.000 Tridealhouses could be produced every year, lifting 1,260,000 people from poverty.
Tridealhouse wants to become a global solution for food and income generating houses for over a billion people living in slums.
Our impact goals for next years are:
1) Next year: quality of solution. We develop, demonstrate and validate a housing solution that helps solve 12 of 17 SDG of urban poor living in slums. We refer to our answers and KPI/impact list in the solution overview part.
2) Within 5 years: quantity of replication. Our solution will be a financially sustainable and replicable industrial solution. We use as much local resources as possible to limit foreign currency restrictions. We produce Tridealhouses in model factories that can be replicated/adapted in other countries in cooperation with local or international stakeholders.
A factory Capex to produce 10,000 Tridealhouses per year is about 25 million $. We will generate a fixed, transparant, re-invested 4% net profit on turnover. Because of ODA loans and support, the actual IRR on own funds will be high. Therefore, exponential financing & replication of factories should be possible.
We calculated that to solve the global slum problem in a 10 year span, 3000 factories should be established each producing 10,000 Tridealhouses per year. For housing loans, a revolving housing fund of around 350 billion $ should be established during 15 years to finance 25% foreign currency component. 75% local loans can be financed without causing inflation as the houses increase GDP. Therefore, it is a globally scalable solution, as it will generate a profit and repays the debts.
1) High level barriers:
To succeed, 5 types of national and international stakeholders are needed. We succeeded to have cooperation with all of these for our Ethiopian project. Therefore these barriers have mainly been solved for Ethiopia. But to succeed in any country, each time these 5 stakeholders are needed on local and international level for that country.
1) Governmental support (land, regulatory, local housing financing etc). We work with and have a MOU with the Ethiopian Government
2) UN agencies, WB/EIB etc (validation and support, international financing). We currently work with 3 UN agencies - Un-Habitat, UNDP, FAO, strong interest from WB/EIB
3) Research institutions and universities. We work with 1 research institute and 6 universities, we also have a international management consultancy partner supporting us
4) Industry/OEM partners (production): we cooperate with 3 industrial partners and are expanding this
5) Impact investors/ foundations: we recently have an 175,000K Euro investment from the Swiss Happel Foundation for phase1.
A barrier we currently have is optimal OEM selection and industrial production.
The second barrier is that we are a small, albeit brave, organization. therefore we need support, advice and guidance to grow.
2) Developing country barriers/ risks:
On local level, there are specific country/ project barriers or risks, of which the main that we identified till now are
Absolute:
Political turmoil risks/ violence/war/ looting etc
Relative:
Financial handling risks
Corruption
Weak judicial and administrative structures
Transport and related logistic problems.
Quality / production/ management control issues in local factories.
Limitations in financing the foreign currency components.
1) High level barriers:
As pointed above, we already have full support of the 5 major stakeholder types in Ethiopia and therefore they are part of our resources. We have access to most technical solutions and know-how, and since recently have funds to start phase 1. As we are entrepreneurs, we do not see problems setting up local factories and expanding partnerships.
The two main barriers that we have to overcome are
1) how to set up local production of OEM components. Based on our experience, we think we will be able to attract and create partnerships. But this is still ongoing work
2) how to overcome the severe foreign currency limitation in Ethiopia. That will have to be discussed/ agreed with the government and major ODA/WB/EIB financial institutions
2) Developing country barriers/ risks:
Political turmoil/ conflicts/ looting/ war barriers or risks are less applicable at this moment as we will only start in stable countries.
Mitigation of other risks/barriers is as in following table
The general rule and mitigation of risks and barriers for our project is by expanding cooperation with many stakeholders and building on their experience, inputs and advices.
- For-profit, including B-Corp or similar models
A total of 30 to 40 people are engaged on the implementation/advisory of the solution.
Two full time Directors, in Belgium and Ethiopia, one part-time finance director and one part time assistant are directly working on the solution.
Contractors, consultants and advisors are involved in the work.
The Government of Ethiopia assigned a team of Addis Ababa Science and Technology University. The advisory team include Assistant Professors in civil engineering, material science, architecture and agriculture.
In Belgium/Europe, 5 universities, 1 main research center, and 6 company partners are involved, and supporting us with their know-how, resources, laboratory capacity and networks.
Tridealhouse integrates best practices of 15 UN agencies to solve global slum problems. The concept is developed out of years of lessons learnt and best practices in various international organizations. Tridealhouse directors count 50 years of combined UN and ODA cooperation. Our extended team embeds business skill, development know-how, and scientific skills obtained through long years of experiences.
Founder and CEO,
Dr Michel Loots, has been high level best practices expert for 15 UN agencies
the last 25 years of which UN-Habitat, FAO, WHO, UNESCO. He also owned and
managed several SMEs and NGOs. He has a medical doctor degree and also a full economics degree. To create slum solutions he obtained
certificates in concrete technology and building.
Dr Fasika Kelemework holds a
Doctorate in Business Leadership and Master in Development Evaluation and
Management. He worked for the last 24 years in various organizations including
the European Union office and International NGOs in Ethiopia. He worked as
Director of Performance Management in the Ethiopian Agricultural Transformation
Agency and as a Senior International Consultant in different countries in
Africa.
Our team of
technical advisors in Ethiopia are senior professors at the Addis Ababa Science and
Technology University. They are supporting Tridealhouse in refining
technologies, selection of alternative building materials and confirmation of
local building codes.
In Europe we work with 5 universities and a main research center.
Addressing the global market needs cooperation of five essential stakeholders with whom Tridealhouse is cooperating .
The Ethiopian Government provides the necessary land, regulatory support, local currency housing loans. We signed a MoU with the Ministry of Innovation and Technology in Ethiopia to pilot and scale up Tridealhouse in the country. Several Ministries, including Ministry of Agriculture & Ministry of Housing and Construction are interested to collaborate.
The other essential partners are UN organizations and related donors for global validation & outreach, financing early stages of the introduction of the Tridealhouse; for the moment UN-Habitat, FAO, UNDP are interested. Our solution has been very well received and featured as “a true example of urban innovation in housing” at the UN-Habitat Assembly https://www.facebook.com/tridealhouse/
Universities and research centers play significant role in local validation and extension. They contribute to adapt technologies and select available local construction materials in each country. We are currently collaborating with Addis Ababa Science and Technology University, in Ethiopia. In Europe we work with 4 Belgian universities (Antwerpen, Leuven, Gent, Hasselt) and VITO
Industry helps to apply their best know-how and production technologies for efficient manufacturing of components of Tridealhouse. We work with Sadef Voestalpine for the steel profiles, Goponic company for the gutters, De Bonte Beton and VASHT NV for concrete technology
Tridealhouse is a social impact company and needs strong partnership with Foundations and Impact Investors as shareholders and investors for parts own equity. We recently got funding for phase 1 by Happel Foundation in Switzerland.
1) Selling Trideallhouses that the poorest can repay by generated revenues and savings
Tridealhouse delivers decent houses with proper sanitation and hydroponic growing structures which allows growing of fresh vegetables on the sides. At mass production each house cost 12,000 to 14,000 $. It will be financed by mortgages or micro-credits. Partial government subsidies might be needed in the beginning. The house is income-generating and self-financing. It creates job opportunity and generates total income of over 1,200 $ per year both in cash and self-food supply. In addition to this, the house saves a total of 200 $ on rent and 200 $ cost of energy through the solar energy it collects for cooking, lighting and warm water. It provides total benefit of minimum 1,600 $ per family per year which enables to repay the mortgage in 10 to 15 years.
2) Developing profitable industrial-humanitarian factories that can be financed and replicated.
The factories will work transparently with 4% net profit and a high IRR. We strive that ownership of factories are as much possible in hands of foundations or impact investors so that maximization of outreach, number of factories replicated and reinvestment of profits are the main common objectives.
3) Tridealhouse will provide following circular benefits to the community and the government, which in turn will support us locally and internationally
Poverty reduction
Better social and health outcomes
Direct and indirect employment
Better urban planning, infrastructure, and disaster preparedness
Industrial and economic development
Long term GDP growth
Strengthening government policies
- Organizations (B2B)
Primarily we are applying to Solve to expand our technical and industrial OEM solutions as outlined in the solution page, search for additional funding / investment sources and support in our organizational model.
- Business model
- Solution technology
- Funding and revenue model
- Board members or advisors
- Marketing, media, and exposure
- Other
The most important is to find additional OEM solutions/components to fulfill the needed functions of the Tridealhouse. These components should be manufactured preferably locally (because of foreign currency restrictions) or at low costs , with high quality and durability. The main technical issues are relating to energy, water, sanitation, and hydroponics subjects.
We seek to refine and enhance our mixed international/ local business model. What model of management should we develop for our local industrial production. How to mitigate the risks, as outlined in barriers, in an international structure?
As we are still a small organization with ambition to grow into a big organization, we seek support and advice on how to structure this in our DNA, and how to secure long term financing.
We want to identify the best marketing/ media/IT strategy and potential partners in this field?
For technical solutions MIT faculty and Solve members could contribute to help find the best OEM or open source solutions that use as much as possible local materials or resources.
For industrial organizational and management model support, we think support from an established industrial consultancy company would be useful
For funding/ investment we would like some guidance and advice in this respect
The main users and beneficiaries of Tridealhouse are woman and children.
Tridealhouse addresses the day-to-day challenges of women and their children living in slums. Tridealhouse provides food and job opportunity on the house. The private sanitation makes it safer for woman. The solar thermal and PV energy will diminish need of collecting firewood and will reduce cooking in unhealthy environment. Overall, Tridealhouse will bring a happier, healthier and safer living environment to women.
We will use the Innovation for Women Prize to specifically create teams of local woman and woman user groups in Addis Ababa.
They will contribute to evaluating and adapting Tridealhouse to their needs, and co-develop business models of joint community activities, such as joint vegetable, fruit or micro-livestock growing, community markets. They will also help study and develop a social engineering model of woman-and family friendly hamlets of 50 Tridealhouses on 50 concrete 1-storey levels that are built around safe, enclosed multifunctional courtyards. This will include space for chickens and goats, a washing area, fruit trees, a children playground, joint caring for the elderly, and micro-business spaces for woman.
CEO
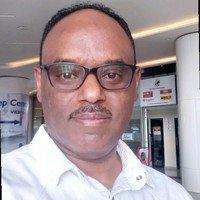
Director Ethiopia/ Africa
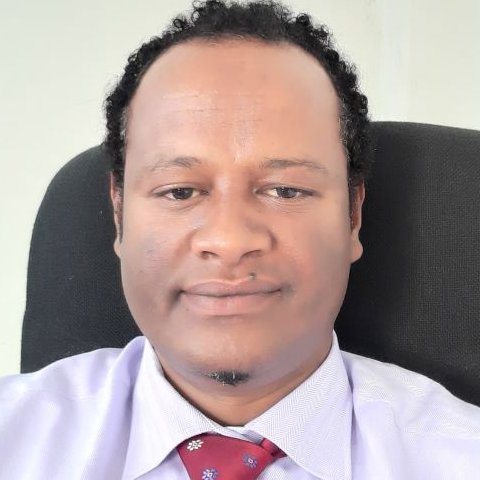
Assistant Professor of Civil engineering, Director of Center of Excellence in Construction Quality and Technology