Reducing post harvest loss in Africa
The problem we want to solve is the post harvest food loss (PHL) in Africa, where PHL amount to 100 millions tons annually (FAO - SAVE FOOD).
This means loss of income for the farmers and loss of water, land, labor and capital.
PHL is mainly due to low roads infrastructures, lack of cold warehouses and low processing facilities.
Our solution is technical and organizational.
On the technical hand, we bypass the lack of infrastructure and low finance of those countries by designing mini-factories, that can process fruits and vegetables as close to the farms as possible.
Vegetables are processed into puree and fruits are processed into puree or juice.
On the organizational hand, we designed an ecosystem which address the whole food value chain in those countries.The ecosystem will include government agencies, food processors, farmers, end products distributors, etc.
According to FAO (“SAVE FOOD” report):
- Food loss and waste amounts to US$ 310 billion in developing countries, fruits and vegetables having the highest wastage rates.
- In Africa alone, post-harvest food loss (PHL) amount to 100 millions tons annually,
- PHL amount to a major squandering of resources, including water, land, energy, labour and capital and needlessly produce greenhouse gas emissions, contributing to global warming and climate change,
- PHL aloso means lost of income for small farmers and higher prices for poor consumers.
The PHL is due to:
- low roads infrastructures to carry crops to the cities where most customers live,
- lack of cold warehouses to increase the shelf life of the crops,
- low number of processing facilities. The existing ones are often build near the cities, which favor large farmers who can carry the crops on long distances.
On the other end of the food value chain:
- The Africa's growing urban population is increasingly seeking processed and easy-to-process foods (FAO - “SAVE FOOD” report),
- African middle class and dispora represent more than 170 millions potential customers (McKinsey Global Institute and World bank reports) for the end products made from those lost crops.
Our solution is technical and organisational. It focus on vegetable and fruits, that are the more vulnerable post-harvest crops.
On the technical hand, we are designing a modular mini-factory that can process fruits and vegetables as close to the farms as possible. Vegetables are processed into puree and fruits are processed into puree or juice. The purees are packaged in 400 gram and 800 gram bags and the juices are packaged in 33 cl and 1 l bottles. They are then thermally stabilised, which extends their shelf life by 1.5 years.
By moving processing closer to the farms, our solution bypass the lack of road and cold storage infrastructures.
On the organizational hand, we designed an ecosystem which consist of partenering with other stakeholders in the food value chain in order to make sure small farmers get fair prices for their crops and the end products are sold on local, national or international markets. The ecosystem partners will include government agencies, food processors, farmers, end products distributors, waste management companies, NGOs, etc.
Our number one targetted beneficiaries are small farmers.
As the son of small farmers from Cameroon, I know much of their needs. As a company, we've done or ordered 4 missions in our pilot country (Ivory Coast) and study all the stakeholders thoroughly in order to understand their needs (fruits and vegetable farmers, food processors, food distributors, NGOs, cooperatives and goverment agencies. In addition to getting their needs, we got useful inputs to improve our solution.
Small farmers needs are:
- To Get crops out of its landlocked farms,
- To Sell all crops not needed for family consumption,
- To Sell crops at a price high enough to pay for expenses and get profit to live decently.
Our solution adresses these needs in the following ways:
- Small farmers can easily carry their crops to the mini-factory and
get they shelf life extended so they won't be in a hurry to sell (at low
price) anymore. - Thanks to our distributors partners, we will actually widen small farmers productions' market to national and international markets in addition to they current local market.
- Improve supply chain practices to reduce food loss, scale new business models for producer-market connections, and create low-carbon cold chains
Moving processing to farms is a way to:
- improve supply chain. For a given distance between the farms as the customers in the cities, we reduce the distance fragile fresh crops have to travel and increase the distance stabilized and easy-to-pack end products travel.
- remove/reduce the need for cold storage
Bringing together the farmers, food processors and end products ditributors favor producer-market connections.
- Prototype: A venture or organization building and testing its product, service, or business model
- A new business model or process
- Internet of Things
- Manufacturing Technology
- Rural
- Poor
- 1. No Poverty
- 2. Zero Hunger
- 8. Decent Work and Economic Growth
- 9. Industry, Innovation, and Infrastructure
- For-profit, including B-Corp or similar models
Full-time : 3
Part-time: 3
Design partner (www.cirad.fr): 5
Victor NONO (Founder & CEO)
Eng. Information & com. Technology
MBA HEC-Paris
Timoty SAVOURÉ (R&D Manager)
Eng. Agronomy / MSc. Food processing
PhD student Food processing
Othmane ENNASRI (CTO & Business Development)
Eng. Mechanical eng. & production
MSc. Industrial & Logistics Project Mgt
Brice AGUI-M. (Supply chain & Bus. devt)
MSc. Agrifood business development
MSc. student Global supply chain
Privat LASME (CEO Advisor)
Msc Food engineering
PhD Food technology
MBA Laval University (Canada)
Christelle NONO (R&D engineer)
Eng. Agronomy & food processing
Pr Antoine COLLIGNAN (CIRAD)
PhD in food process engineering from Bordeaux University (France) and McGill University (Canada).
Pr Manuel DORNIER (CIRAD)
PhD in food process engineering from ENSIA (now part of AgroParisTech, “Paris Institute of technology for life, food and environmental science”).
Dr Michel RIVIER (CIRAD)
Engineer in mechanical and Automatic Engineering
PhD in food process engineering.
Dr Martial MADOUMIER (CIRAD)
PhD on the design of the milk evaporation process by multi-criteria optimization.
Our team members are complementary, and everyone is involved, with a sense of the mission we are here for.
We have been working with CIRAD (www.cirad.fr) for more than 3 years.
We are using CIRAD expertise and facilities to design our mini-factory and build the first prototype.
- Organizations (B2B)
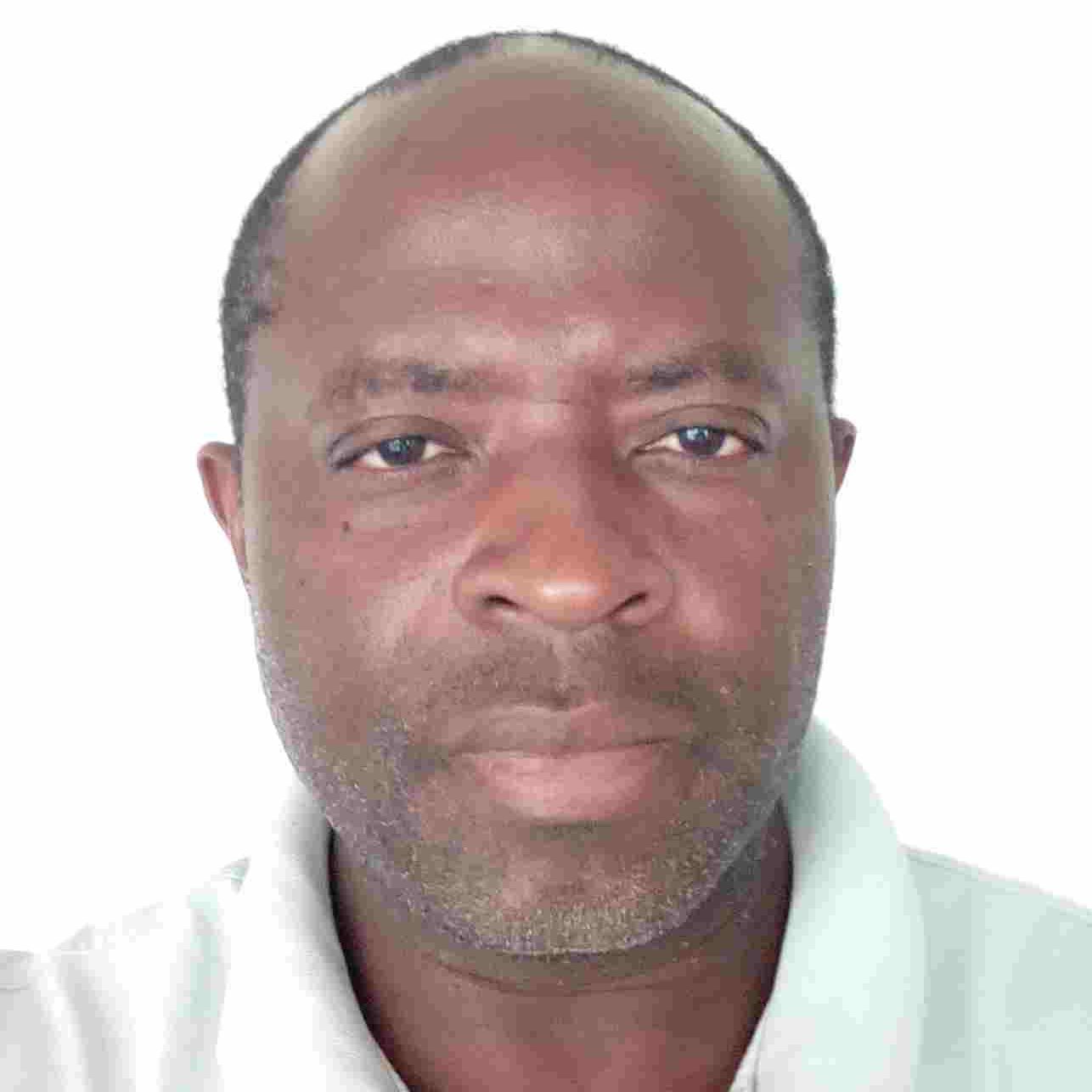
CEO