3D Printing Functional Goods from Puerto Rican Plastic Waste
re:3D is a social enterprise committed to decimating the cost & scale barriers to 3D-printing in order to create jobs & enable problem-solvers worldwide to independently address local needs.
Gigabot, re:3D's flagship technology is a large, industrial 3D-printer starting under $9K. Gigabot rivals the printing quality of other industrial printers at 1/10 the cost and boasts a build volume starting at 30X larger than desktop models.
Founded with $40K from Start-Up Chile, re:3D was a top ranking graduate and successfully closed a $250K Kickstarter campaign for Gigabot while in residency. 5 years later, re:3D has continued to sell printers in 50+ countries.
With no outside investment, all developments to enable human-scale 3D-printing solutions have been accomplished through partnerships, crowdfunding and prizes.
Recently re:3D modified Gigabot to directly 3D-print from shredded reclaimed plastic waste to truly enable affordable, sustainable, and locally driven manufacturing in Puerto Rico, the Caribbean & beyond.
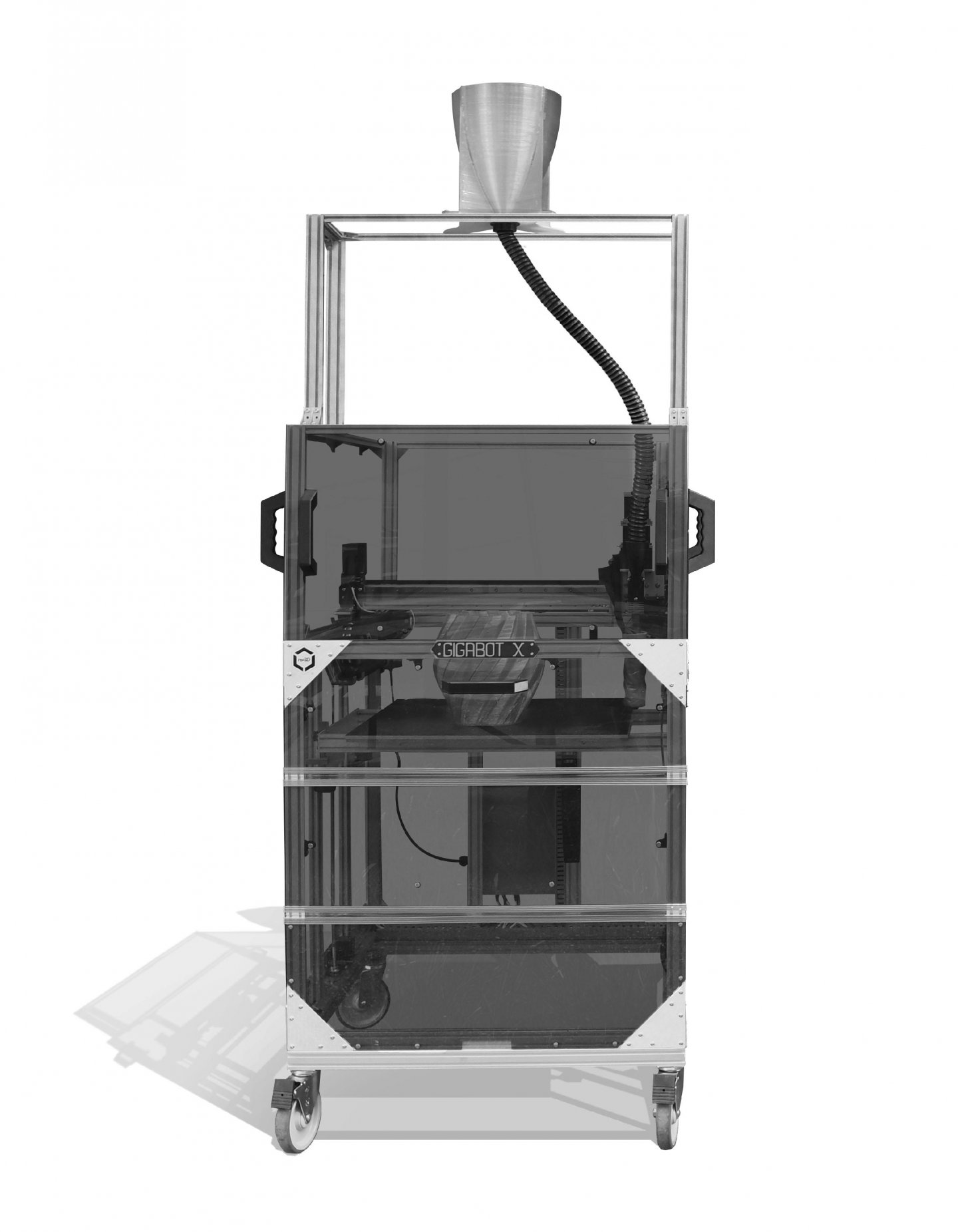
Caribbean islands such as Puerto Rico encounter unique challenges as up to 80% of goods are imported, often with long & expensive supply chains. For critical and high demand goods, resource scarcity & regional considerations must be therefore anticipated in advance in order to ensure all necessary materials are available when needed. Imported goods with potential to be manufactured locally through 3D-printing are an attractive alternative to offsetting the $20B spent on PR imported goods, considering unemployment is at 16.5% and small business is growing at 4%.
While Fused Filament Fabrication offers tremendous benefit for rapid prototyping, mass customization, and low cost fabrication, the technology is contingent on access to high-quality extruded feedstock. Currently the 3D-printer industry represents a "blade & razor" model, where users must have access to feedstock manufacturers. Not surprisingly, heat maps of 3D-printer usage show deployment primarily in N.America, China, and Western Europe. After interviews with current & potential users in the Caribbean & LatAm, re:3D began to question if 3D-printer adoption would increase if access to the 3D-printing supply chain was democratized by leveraging plastic waste. This also offers energy & concomitant emissions savings. For this reason, re:3D opened an office in Puerto Rico in 2017.
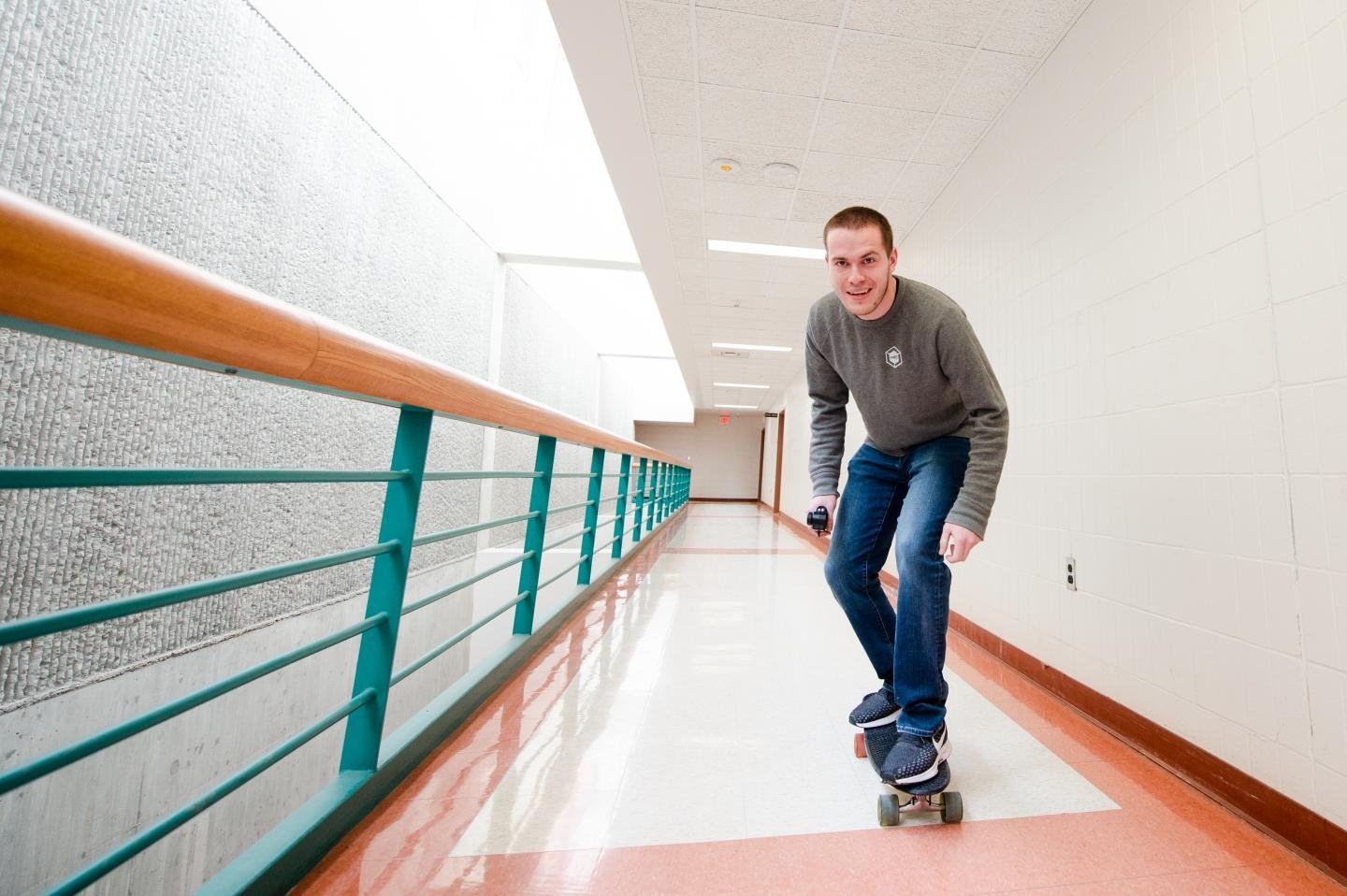
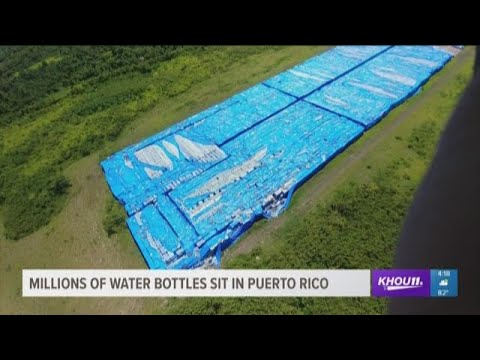
After establishing operations in Puerto Rico in 2017, and enduring hurricane Harvey, which hit our Houston Factory one month before Hurricanes Irma and Maria impacted our team in Puerto Rico, we've personally witnessed the opportunity onsite manufacturing provides in disaster response/resiliency as well in new job creation, education, and in supply chain reduction.
Since 2017, we have:
- Provided free 3D design and printing services to anyone impacted by the hurricanes
- Hosted a monthly island-wide meetup for those interested in earning incomes through 3D printing (over 75 attendees to date)
- Sold Gigabot & services to 3 middle schools, one IoT lab, and several small businesses
- Mentored countless entrepreneurs and regularly support free printer & design workshops for multiple groups including universities, IEEE, the American Chemical Society, and Parallel 18 (the island's startup incubator).
- Cultivated a relationship w/the Puerto Rican Science & Research Trust to explore opportunties to design & print functional objects from discarded water bottles to create new jobs
- Accepted invitations through the island's manufaturing association to meet with 4 of the island's largest manufacturing companies, who provided plastic manufacturing waste to test in our hardware in order to divert it from landfills
This work has yielded significant support & exposed multiple opportunties for scale.
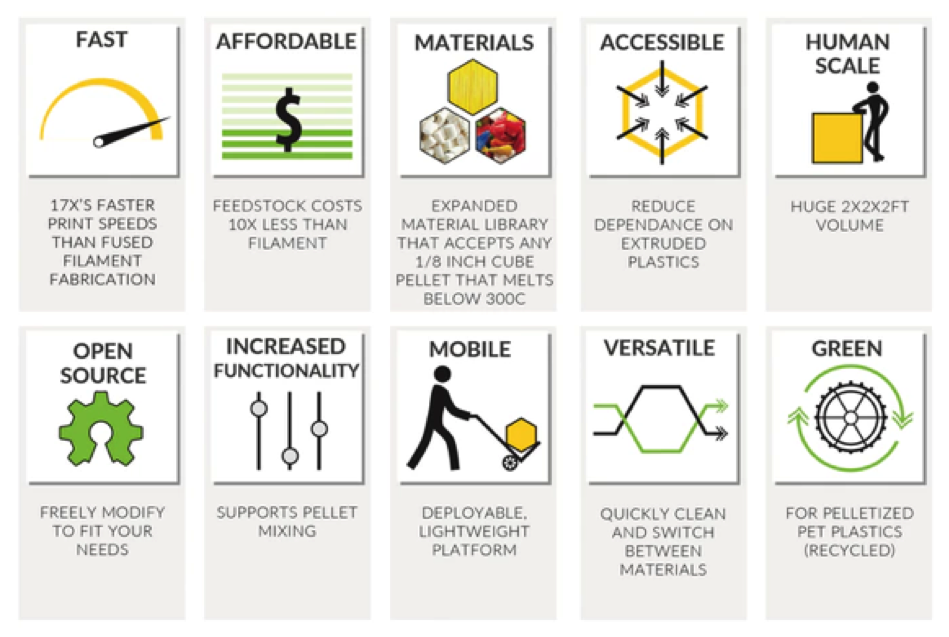
3D-printing offers tremendous benefit for rapid prototyping, mass customization, and low cost fabrication. This creates an untapped opportunity to more affordably and accessibly support industrial manufacturing for island nations.
Specifically, the ability to source locally available raw material and feed it directly as pellets or shavings/flake into a printer rather than extruded filament could be extremely advantageous in regards to reducing cost and increasing capabilities in prototyping. The benefits of this innovation are amplified when 3D-printing large-scale industrial objects (defined as > 18 inches cubed). First, the production of large-scale products represents a larger investment of time and material costs (pellets/flake are at least ~ 1/10th the cost of filament). A second reason for the importance of pellet/flake extrusion is it addresses the need to print faster (up to 17x faster). Finally, a dependence on extruded thermoform plastics limits the available library for printing and the ability to mix materials to engineer new formulations and/or the ability to introduce additives directly into the machine while printing.
With domain expertise in large-scale 3D-printing, re:3D has developed a pellet & flake/regrind extrusion 3D printer capable of printing with polyethylene terephthalate (PET- the material found in water bottles) as well as other reclaimed materials, to further optimize the pellet printer to be able to accept reclaimed flake as well as non uniform pellets. This effort includes developing the ability to consistently dry and to easily clean and switch between materials. A novel mechanism for feeding larger volumes of pellets and/or flake into the platform is also being developed with the requisite controls.
Conversations with re:3D’s existing Caribbean customers who utilize re:3D’s Fused Filament Fabrication (FFF) 3D-printers suggest that this new pellet printer could have value to the Puerto Rican customers if water bottles, a PET plastic, and discarded in abundance on the island could be leveraged as the feedstock. This research proposes to source such water bottles and test the ability to grind & extrude the flake in re:3D’s pellet printer. Working the Puerto Rico Science & Research Trust, early prototypes of local objects made from recycled PET using Gigabot have been produced w/positive feedback, which has generated significant interest in scaling a pilot program to create objects from plastic waste in PR.
- Enable the public sector, especially municipalities, to pilot and implement new and innovative systems in their waste management
- Growth
Currently only two companies have globally commercialized a large format 3D-printer with a minimum of 2ft+ build volume under $30K/ printer (BigRep, 3DP). Neither of these organizations retail a pellet printing system and/or the ability to print with shredded plastic waste, rather they are limited to filament extrusion. There is one company that is recognized for selling affordable hardware to extrude plastic pellets into filament (Filabot), however output can be inconsistent. There is also an amazing movement that uses open source hardware to extrude filament from shredded waste (Precious Plastics) as well as a commercial desktop system (3DEDEVO), however it as well is better suited for makers and smaller volume production. re:3D’s direct drive pellet extruder is unique in that re:3D intends to produce an integrated system that directly leverages pelletized or shredded plastic, rather than extruding feedstock in a secondary device which then requires coiling & loading onto a FFF (Fused Filament Fabrication) 3D-printer. This technology will be available as both a 3D-printer and as a device that can be mounted to other 3D printing platforms besides those sold by re:3D. You can view both our affordable large scale filament as well as pellet/flake printers at https://re3d.org/gigabot. By demand, and subsequent funding from the National Science Foundation, re:3D intends to release an affordable drying and grinding system to complement Gigabot by the end of 2020. This technology is being design based on requirements provided by our Puerto Rican community and will be piloted on the island.
As advocates for helping people independently address local needs, we're motivated by the opportunity to sustainably create jobs, foster economic independence, and stimulate economies. Specifically we're confident that that the Gigabot we modified to print from ground up plastic, as well as our current offering, will create 500 jobs in 5 yrs. Our customers have already created cash flow positive companies, and are impacting their local economies. With the support of MIT solve, we hope to create at least business and 100 jobs in the Caribbean using a large-scale 3D printer that can accept reground plastic (recycled or non-recycled).
Sustainable Input Materials: In 2017, CNBC reported the world has produced over 9B tons of plastic since the 1950s, and only about 9% was recycled. Enabling 3D printers to use plastic waste has the potential to repurpose 30,000 bottles/month into functional products from the consistent use of only 1 Gigabot. The potential for this new technology is endless.
Reducing Transportation and CO2 Emissions: As pollution reduction is tied to supply chain management (less transportation = less pollution), a secondary environmental gain from encouraging local manufacturing is the reduction in transportation costs. A 85% transportation cost savings is anticipated over the next 10 years as 50% of global goods are expected to be made locally- finished goods from Asia, or other major export markets, will not need to be shipped.
Waste Diversion: As several PR landfills are anticipated to close in 5 years, the proposed technology can divert waste with an economic upside.
- Rural Residents
- Low-Income
- Middle-Income
- Policymakers/government
- Business owners
- Other
- Argentina
- Australia
- Austria
- Belgium
- Bolivia
- Brazil
- Bulgaria
- Canada
- Chile
- Colombia
- Denmark
- Egypt
- Estonia
- Finland
- France
- Germany
- Guatemala
- India
- Ireland {Republic}
- Israel
- Italy
- Japan
- Kenya
- Korea South
- Kuwait
- Luxembourg
- Malaysia
- Mexico
- Netherlands
- New Zealand
- Nigeria
- Norway
- Oman
- Philippines
- Poland
- Portugal
- Qatar
- Romania
- Senegal
- Singapore
- South Africa
- Spain
- Sweden
- Switzerland
- Turkey
- Uganda
- United Arab Emirates
- United Kingdom
- United States
- Uzbekistan
- Aruba
- Bahamas
- Belize
- Cambodia
- Cameroon
- Costa Rica
- Dominican Republic
- Ecuador
- El Salvador
- Georgia
- Greece
- Guyana
- Haiti
- Honduras
- Hungary
- Jamaica
- Latvia
- Lebanon
- Liechtenstein
- Lithuania
- Malawi
- Marshall Islands
- Mauritania
- Mauritius
- Micronesia
- Montenegro
- Mozambique
- Nicaragua
- Panama
- Paraguay
- Peru
- Rwanda
- Saudi Arabia
- Sierra Leone
- Solomon Islands
- St Kitts & Nevis
- Taiwan
- Thailand
- Trinidad & Tobago
- Tunisia
- Uruguay
- Vietnam
- Curacao
- Hong Kong
- Macau
- Argentina
- Australia
- Austria
- Belgium
- Bolivia
- Bulgaria
- Canada
- Chile
- Colombia
- Denmark
- Egypt
- Estonia
- Finland
- France
- Guatemala
- India
- Ireland {Republic}
- Israel
- Italy
- Japan
- Kenya
- Korea South
- Kuwait
- Luxembourg
- Malaysia
- Mexico
- Netherlands
- New Zealand
- Nigeria
- Norway
- Oman
- Philippines
- Poland
- Portugal
- Senegal
- Singapore
- South Africa
- Spain
- Sweden
- Switzerland
- Turkey
- Uganda
- United Arab Emirates
- United Kingdom
- United States
- Aruba
- Bahamas
- Belize
- Brasil
- Cambodia
- Cameroon
- Costa Rica
- Croatia
- Dominican Republic
- Ecuador
- El Salvador
- Georgia
- Germany
- Greece
- Guyana
- Haiti
- Honduras
- Hungary
- Jamaica
- Latvia
- Lebanon
- Liechtenstein
- Lithuania
- Malawi
- Maldives
- Malí
- Marshall Islands
- Mauritania
- Mauritius
- Micronesia
- Moldavia
- Montenegro
- Mozambique
- Nicaragua
- Panama
- Paraguay
- Peru
- Qatar
- Romania
- Rwanda
- Saudi Arabia
- Sierra Leone
- Solomon Islands
- St Kitts & Nevis
- Taiwan
- Thailand
- Trinidad & Tobago
- Tunisia
- Uruguay
- Uzbekistan
- Vietnam
- Curacao
- Hong Kong
- Macau
re:3D’s current customer base includes users from 50+ countries. The largest traction has been in manufacturing, rapid prototyping, design, and education, to include many enterprises and federal agencies. One-time sales average $15500 USD for a Gigabot, with repeat sales for upgrades, additional Gigabots, custom solutions and feedstock. re:3D also offers services for installation, maintenance, and upgrades.
Winning this award will allow us to modify Gigabot to accept at least 3 additional types of reclaimed plastic commonly found in trash (e.x. plastic shopping bags, cellulose acetate from cigarette butts, and Polypropylene from drinking straws). We anticipate the Garbage-eating Gigabot + the commercial grinder to scale to at least 10 new countries and to create at least four more jobs within re:3D within 6 months of commercial sales. As this solution will provide groups and individuals one more tool in their toolkit for onsite fabrication, we believe it will stimulate increased opportunities for job creation whether it be in product/output design & sales, or in plastic trash collection & fabrication. Specifically, we believe we can create 500 jobs within 5 years through 2nd and 3rd offsets by enabling locally driven, sustainable, and affordable manufacturing. Finally, we hope that by expanding the reach of 3D printers, we can support technology adoption & innovation in new & emerging markets that will offer a sustainable upside.
Along w/waste reduction and increased processing of recycled plastics, the use of recycled materials for additive manufacturing to promote job growth for collection, sorting & material processing will be measured. There is also potential to further stimulate new business creation for problem-solvers worldwide who can use this technology for locally-driven, affordable low-rate manufacturing. We will measure impact by the number of jobs created with our Gigabot modified to accept reclaimed plastic through pellet extrusion as well as the quantity of reclaimed plastic that our customers report being repurposed through this technology. Currently re:3D provides an annual survey to customers that yields an 80%+ response rate. This questionnaire allows customers to reveal employment created through the use of Gigabot, as well as materials used and hours spent printing. We intend to continue polling our customers as well as those that purchase our systems to 3D print from waste once complete.
While we welcome MIT Solve's feedback on how we can better quantify impact, we are aware that we have delivered over 500 systems to 3D print affordably large-scale in the last 5 years, and 6 systems to print specifically from shredded waste in the last six months since the beta system was released.
The biggest demand for the commercialized grinder and printer system has come from island nations such as Puerto Rico, the Philippines and Aruba. Based on initial purchase orders and inquiries, re:3D anticipates $200K and 500 jobs created in 2nd and 3rd offsets within 5 years of commercial release.
Within the next year we hope to have completed a six month strategic pilot with either 1) a huge manufacturing company (and household name that is disposing of metic tons annually in Puerto Rican landfills) and/or 2) a contractor and/or government agency assigned to disposing of the spoiled water bottles sitting on landfills and warehouses in PR. We are in contact with multiple groups that could grant permission for either objective and welcome feedback from the MIT SOLVE community.
Within the next five years, we hope to have scaled our efforts to create hundreds of job in Puerto Rico, while decreasing the dependence on imported goods. We also hope to have scaled to Aruba, and have supported our customer and collaborator Brenchie's Lab (who also applied to this challenge), to have maximized opportunity to scale new job creation and waste reduction across their island. Not so secretly, we are also hoping that our peers in the BVI, DR, and Bahamas whose governments expressed interest in our technology, will have also initiated strategic pilots.
As a bootstrapped company, being lean is a necessity and outbound marketing is a challenge. For this reason, we depend on speaking opportunities and channel partnerships to promote our offerings. As former NASA nerds & serial entrepreneurs, we lack a network in foundations, large corporate organizations, and academia. We need to aggressively pursue introductions to strategic partners to succeed.
Assuming re:3D is successful in pioneering a commercially available modification of Gigabot to 3D print from plastic waste + developing the associated hardware, the utility of Gigabot's printable output is inherently dependent on the structural properties of the plastic input filament material. Thus, it may not be suitable for all intended uses. Additionally input material will likely be sourced from, multiple waste providers, and some waste may be contaminated. re:3D is thus prioritizing research to include mixed & dirty plastics.
Despite risks of adding technical features to a proven platform and then having to support community management, re:3D’s engineers feel it is imperative to start prototyping solutions to enabled 3D printing from reclaimed plastic with the support of academics devoted to additive manufacturing. We also feel that it is inherently right.
These developments needed to optimize the grinder, shredder and dryer for income driving Puerto Rican needs will consume valuable engineering, management, and resources that re:3D could allocate to other priorities. However, with the support of this award, re:3D could offset these risks and pioneer a much needed advancement.
In order to maximize commercial viability, the ability to 3D print directly from waste will not only be a complement to Gigabot, but also a stand-alone, modular commercial system that would be adaptable to both industrial and consumer based additive manufacturing machines. If expert analyst projections of the industrial large – scale 3D printing marketing hold true, 3D printing from reclaimed plastic could yield a $600M opportunity in the next five years.
- My solution is already being implemented in Latin America and the Caribbean
We currently have multiple customers using our filament - based Gigabot & services in Puerto Rico, as well as Aruba, Bolivia, Colombia, Argentina, and Chile (where we started).
In order to evaluate the strategic potential to use shredded and/or pelletized waste to print functional objects that could have local demand and/or create jobs, we maintain an office in Puerto Rico in partnership with Parallel 18 and the Puerto Rico Science & Research Trust (PRSRT).
As part of the PRSRT support, re:3D worked with connections made through the Parallel18 community to source requirements for potential prints to be made with rPET pellets as a demonstration of the ability to print functional prints from a reclaimed material. From 2018-now, re:3D had the honor of identifying a use case for a functional print made from rPET with Sandra’s Coffee Farms in Adjuntas Puerto Rico who shared a real-world need to fabricate a better coffee picking basket that could improve both yields and worker comfort. Over the course of 6 months, three trips were made to Sandra’s farms to observe current practices, and interview end-users. This research resulted in six revisions. After identifying an ideal form that enhanced comfort for workers, while maximizing the amount+quality of bean picked, the basket was tested extensively
We believe, this is just one of many functional prints that could be be created from Gigabot X using reclaimed materials fro recycled water bottles in Gigabot X.
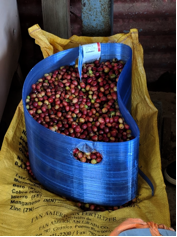
Example of functional coffee picking basket after 6 iterations printed from recycled water bottles in Puerto Rico.
N/A
N/A
27 people work on our team from our Houston, Austin and San Juan offices.
Our unfair advantage is that our NASA team of scientists & engineers has the knowledge, network and now how to execute our vision. We also have a reliable, quality, industrial 3D printer we have supported in 50+ countries for 5 years, giving us confidence we can work with users globally to print their dreams using local resources.
The re:3D team consists of dynamic, passionate makers with diverse professional backgrounds, yet united by one singular vision: to enable 3D-printing accessibility for onsite fabrication. Teammates focused on new product development have highly complementary pedigrees that often leverage past professional NASA experiences. Each team member had a unique moment that fostered an interest in 3D printing & frontier markets.
Professionally and as problem solvers, they have each also witnessed emerging gaps, specifically relating to the functionality and sustainability of 3D printing processes, as well as geographic access. Key contributors & co-founders include Samantha Snabes and Matthew Fiedler, who possess the firmware, business strategy, robotics, marketing, and additive manufacturing background necessitated to pioneer the technology proposed.
Future hires include additional engineers & machinists as well as a dedicated materials scientists to help identify & overcome challenges in working with reclaimed plastic. These hires have already been identified from Matthew & Samantha's network of former NASA employees.
Last year we won the City of Austin Reverse Pitch competition (reversepitch.org), intended to advance the City's goal of being zero waste by 2040. For the competition re:3D chose to work with a waste-stream from HID Global, and pitched the idea of creating usable furniture from their post-manufacturing waste polycarbonate.
Consequently, we have a budding opportunity to work with the Habitat for Humanity REstore. First, we are going to release a line of recycled furniture which will be sold there. The first items will be furniture printed on our GigabotX 3D-printer, utilizing recycled plastic feedstock and wood from the REstore. Next, we are installing a grinder system at the REstore, which we'll utilize to take the polycarbonate feedstock from the Reverse Pitch competition and turn it into a useable feedstock for the GigabotX Printer. We will then use this ground up PC to create more furniture for sale at the REstore. Finally, we are going to work w/REstore to analyze the waste plastics that are going through their donation area, to assess usability as a feedstock in 3D printing to reduce the REstore's waste-stream, to be replicated in Puerto Rico.
MARKET POTENTIAL
With over $6 Million in sales and penetration into multiple verticals, re:3D is poised to capitalize on the growing industrial 3D printing segment. The introduction of a new printer & drying system to allow 3D printing from pellets & recyclables promises to open up new international markets and double sales within one year of commercialization. The target market for this new technology includes medium to large manufacturers seeking to print with non-extruded materials and/or are in geographies whose supply chains constrain access to imported feedstock such as NGOs, island nations and enterprises with remote operations. Federal agencies include organizations supporting disaster response.
BUSINESS MODEL/EXECUTION PLAN
re:3D’s revenue is generated from direct hardware sales, design & contract print services, as well as training & advising businesses on leveraging 3D printing to maintain their competitive advantage.
TRACTION
re:3D’s current customer base includes users from 50+ countries. The largest traction has been in manufacturing, rapid prototyping, design, and education, to include many enterprises and federal agencies. One-time sales average $15500 USD for a Gigabot, with repeat sales for upgrades, additional Gigabots, custom solutions and feedstock. re:3D also offers services for installation, maintenance, and upgrades. You can view a map of our customers at https://re3d.org/gigabot.
re:3D has been incredibly fortunate to be financially profitable from the first year (see above).
Going forward, we believe that this new 3D printing technology that connect directly accept shredded waste will be targeted at an expanded manufacturing industry, valued up to $12 trillion. Researchers at Gartner predict a dramatic increase in the adoption of 3D printing by the manufacturing industry, as 40% of manufacturers are planning to double their use of 3D printing in the next five years, but they are waiting to observe the success of early adopters, such as the government, enterprise, schools, and nonprofits. By removing a barrier to entry by further reducing the cost with our innovative technology, we will be in a competitive category of our own. re:3D already has these early adopters as customers, as our competitive price point is accessible for many different sectors. Over 50% of our customers are buying their second, third or fourth Gigabot in their first year and are demanding the ability to 3D print from ground-up plastic to further scale operations. For this reason, the ability to 3D print directly from plastic waste, or ground-up plastic, will not only be a complement to theGigabot we currently sell in 50+countries, but also a stand-alone, commercial adaptable to industrial additive manufacturing machines. If expert projections hold true, 3D printing from reclaimed plastic could provide a $600M opportunity in the next five years that re:3D will be uniquely poised to capture.
We applied to Rethink Plastics Challengee as it would provide us with the resources to make 3D printing from trash a reality, and we would love to have MIT SOLVE as a partner who share our relentless focus for innovation, sustainability and economic impact. As a veteran, maker, social entrepreneur & the only women CEO leading a 3D printing hardware manufacturing company (that fabricates in-house), I have felt incredibly marginalized during re:3D's journey. Not only would MIT Solve help re:3D bring our technology solutions to the largest audience possible, I not so secretly hoping based on other submissions not done at the the 11th hour like myself that it would provide a network, and much needed support to continue pursuing a road less traveled. I would also be incredibly honored to collaborate & learn from the past, present and future leaders in the program!
- Other
- Technology
- Media and speaking opportunities
We are actively seeking strategic partnerships to pilot this technology. Specifically we are targeting manufacturing companies who are sending clean & virgin waste that we could otherwise divert to local landfills anticipated to reach capacity in 2 years in Puerto Rico.
We would be over the moon excited to collaborate with any manufactures who are currently paying to dispose of waste in the Caribbean, MIT SOLVE, or the UN. Having quit our jobs at NASA, and foregone larger salaries our team is 1000% committed to 3D printing useful objects from plastic waste where it makes sense!
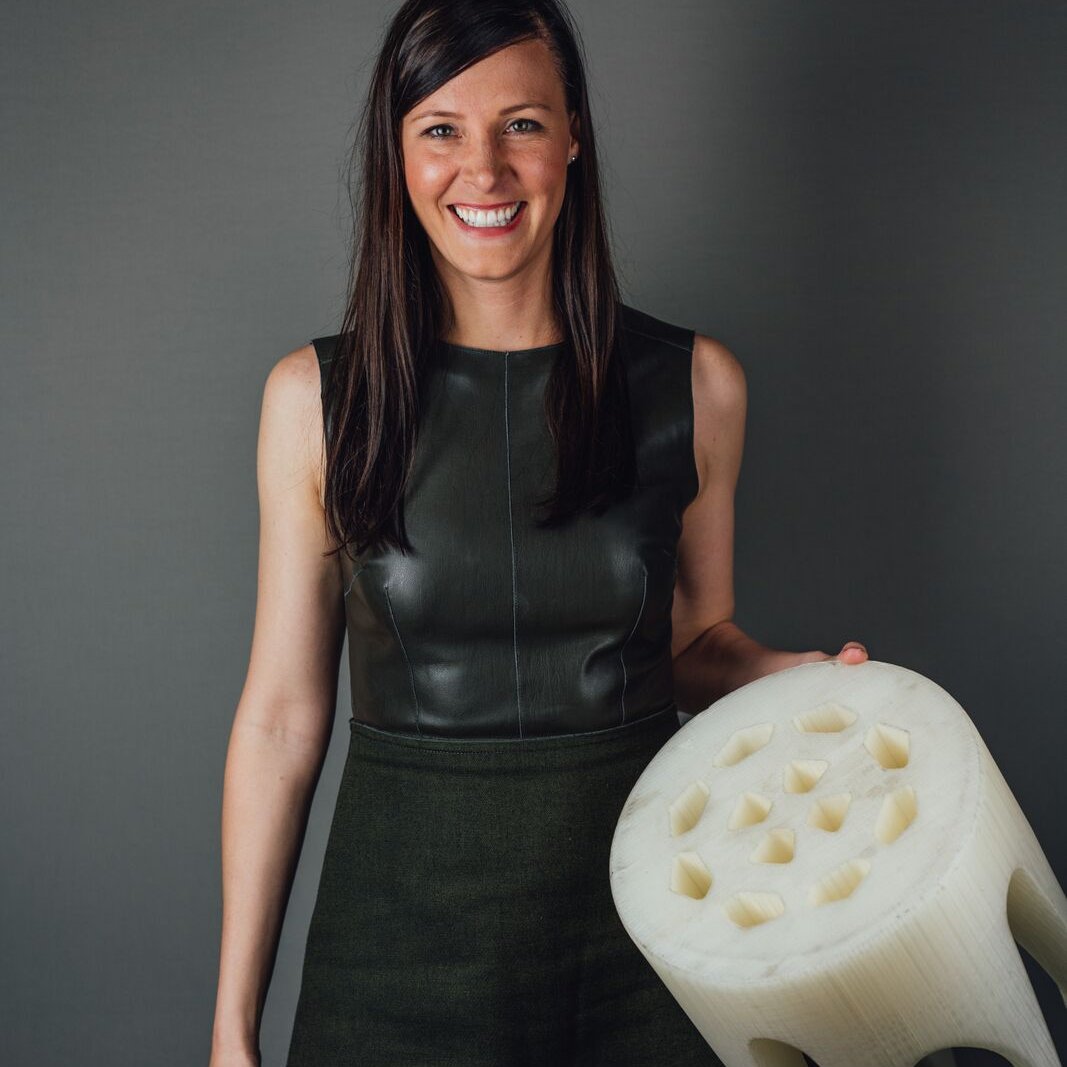
Co-founder and Catalyst