WoodPack
WoodPack is a new biodegradable packaging film material from wood pulp that is high performance and scalable. The material achieves mechanical properties equivalent to those of LDPE/HDPE, is water resistant, and biodegrades in about eight weeks in a landfill. We are proud to have Arauco as an allied and as wood pulp provider.
The WoodPack formula was developed at MIT and its patentable. Our goal is to industrially produce WoodPack, completely replacing LDPE/HDPE film, and we target the construction industry as initial market.
Half of global plastic waste comes from packaging film, which is not recyclable and never degrades. However, Latam and the Caribbean together produces less than 10% of the world's plastic waste. We seek to maintain those numbers by manufacturing biodegradable materials such as packaging film.
The problem that we are solving is the difficulty of replacing packaging film materials with a biodegradable solution.
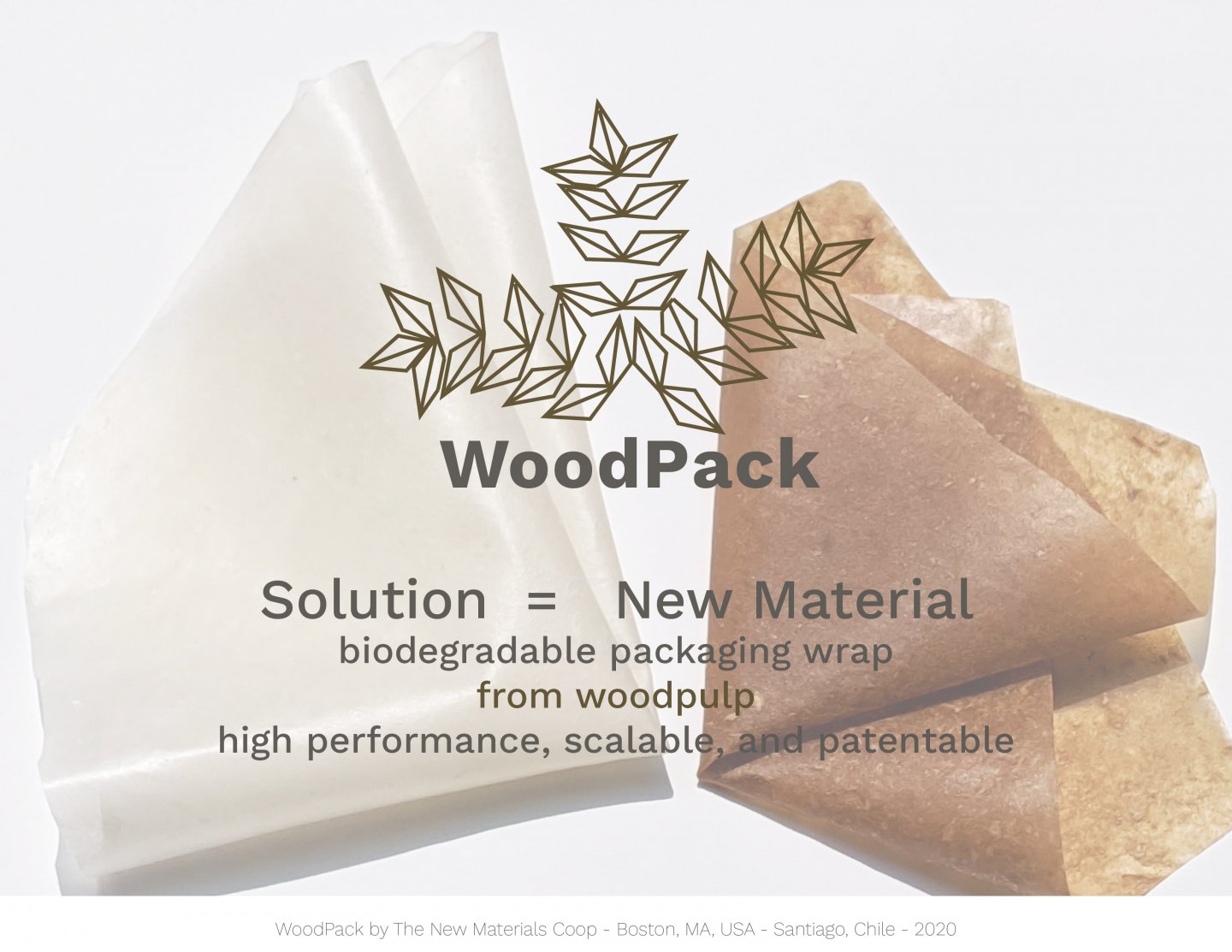
Woodpack is solving the problem of replacing fossil fuel based plastic film materials for the construction industry, which are highly pollutant, with a sustainable solution. Main causes:
Current biodegradable materials do not achieve the mechanical and chemical properties of industry requirements.
Artisanal production of bioplastics.
Latam- Caribbean lacks the facilities to process “degradable” plastics.
Plastic packaging film pollution makes half of plastic waste in the world, equivalent to 90 millions tons per year. This material (LDPE/HDPE) is not recyclable and never degrades, so 96% of film becomes waste, 15% coming from the construction industry.
Available biodegradable packaging films in Latam and the Caribbean do not achieve a minimum industrial requirements such as tensile strength of 9.8 MPa. Fully biodegradable artisanal bioplastics generally achieve lower performance. Mechanically fit films such as Polylactic Film (PLA) are falsely considered biodegradable. It requires a compostable facility to degrade, not common or nonexistent in Latam or the Caribbean.
The forestry industry, and wood pulp as the main component of our material, enables scaling up using already installed infrastructure, unlike fungi or gelatin polymers. Current bioplastic initiatives have often tried to create new economies instead of taking advantage of existing ones.
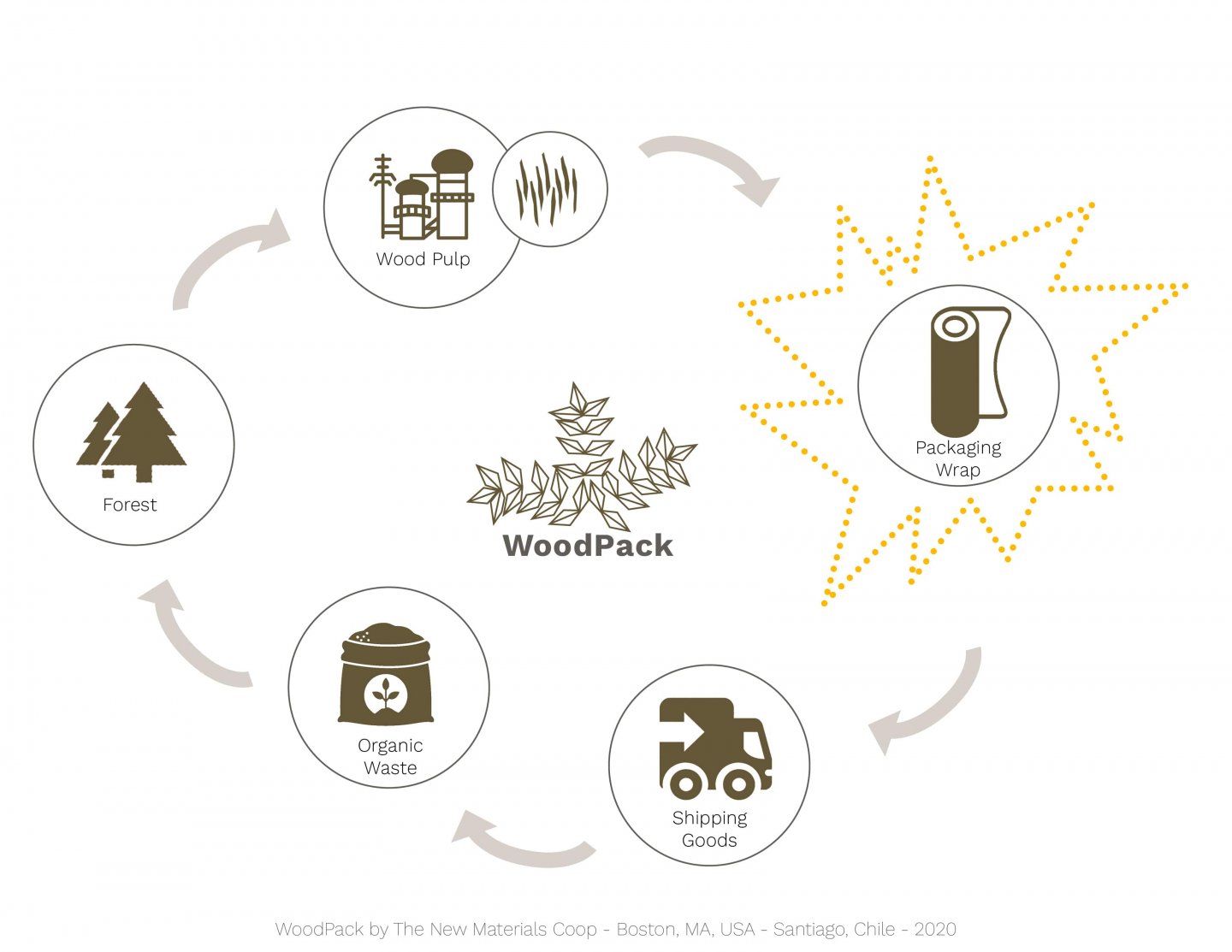
WoodPack serves the construction companies that ship building components and uses plastic film to protect the products they are transporting. Manufacturers, suppliers, distributors, merchants, design and engineering companies.
We understand that the most important aspect of Woodpack is the problem for the clients that is solving. We are centered in developing a customized solution for them. In this aspect we developed two strategies:
Arauco as main supplier and allied: by having regular meetings with the Innovation Manager, understanding our customer and settle the crucial characteristics that they need.
Participation of the client: Designed a survey of 8 questions, now replied (Jan 18th) by 5 possible clients, indicating us, among other subjects, the amount of financial resources invested in buying plastic film, how do they wrap the products to transport and if they would be willing to buy WoodPack even that might be more expensive than regular film.
We provide a New Material, WoodPack: with high performance, with a tensile strength of 27.7 MPa, and some variants achieving 81 MPa; water resistant, with an outdoor life of six months approximately; it is fully biodegradable in a landfill turning into organic waste with a decay time of eight weeks. We are currently testing the chemical advantages of our material. Generally, we assert that it has the same chemical behavior as of wood pulp. The material formula was developed over a year of research at MIT and it is patentable. We have tested traditional plastic film technologies confirming their application. We have currently tested it with additive manufacturing with successful results as well.
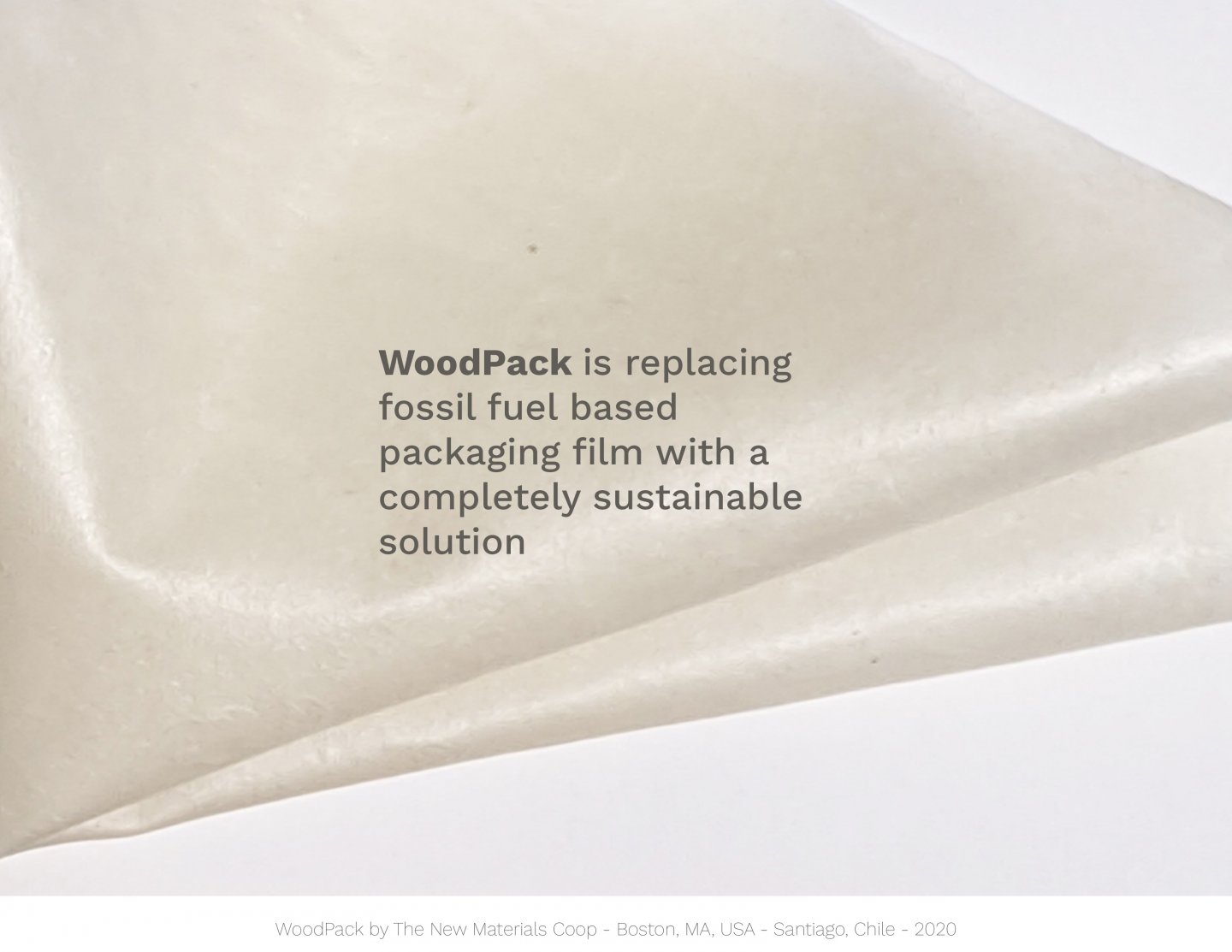
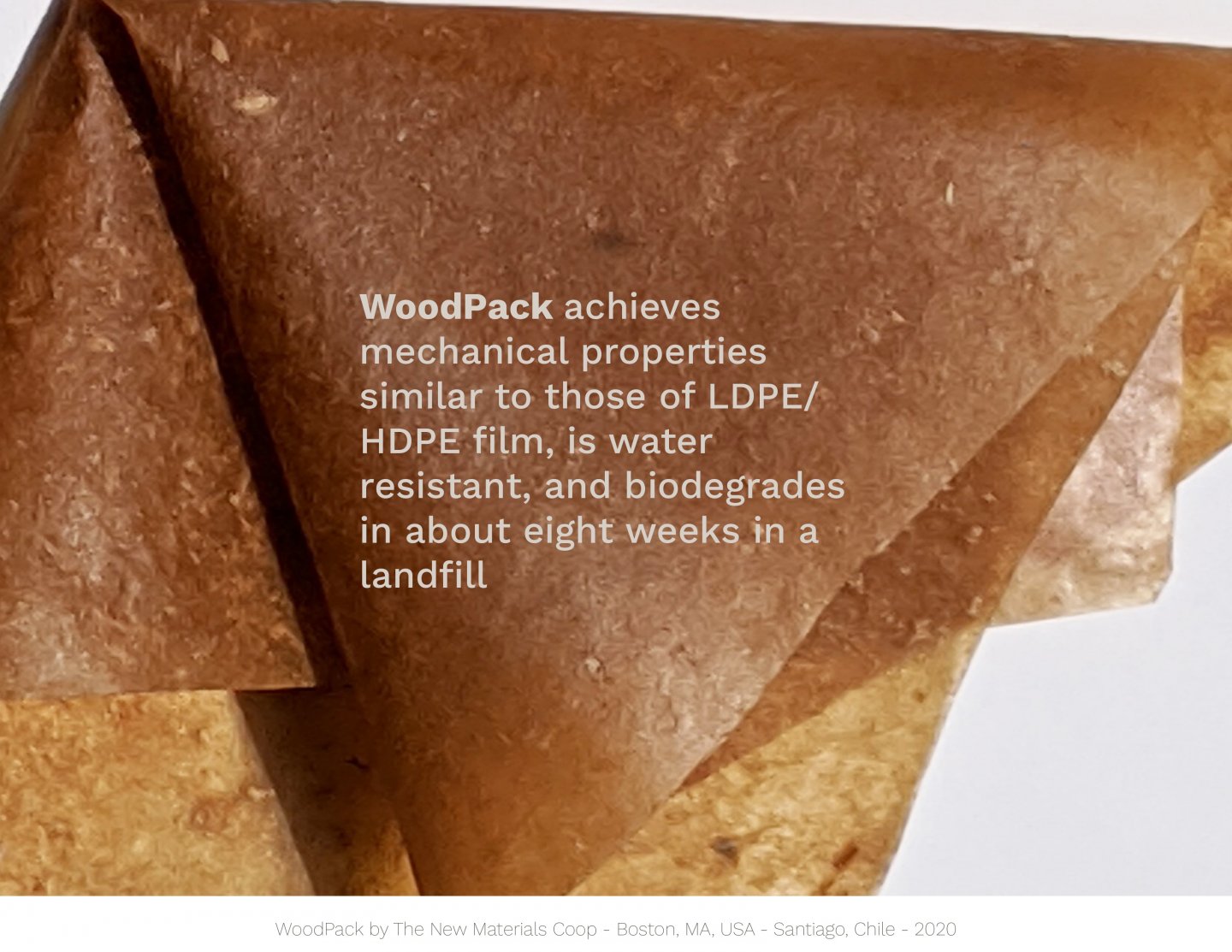
Woodpack can be manufactured on an industrial scale today. Wood pulp is currently available globally on an industry scale, unlike other biopolymers. Our material presents an opportunity to utilize existing wood pulp production infrastructure. We expect to achieve further developments with our main allied, Arauco.
Our team has expertise in Materials and Mechanical Engineering to develop the necessary processes and technologies to industrialize our material / product. In addition, we have Computer Science Expertise to include forefront optimization later on. Further, our team has expertise in Business and in the Construction Industry to succeed in developing our startup and industrializing WoodPack. As paper consumption is declining, WoodPack brings it back to the market as a new product, fulfilling the needs of the clients and the world.
We selected the Construction Industry as our initial market for the following reasons: it requires certifications achievable in the short term, high performance, shipping construction components has tolerance for initial rough finishing, construction is a large scale market and any improvement has a high impact on people's lives. Currently, a highly polluting industry (15% of the world's plastic waste) and we seek to reduce its non biodegradable waste. Construction industry, has a big market in Chile, Latam and the Caribbean and currently growing demand of plastics that can be replaced by biodegradable components. ”The analysts of Ceresana expect global demand for plastics in the construction industry to increase to a level of 73 million tonnes in 2023”.
For Latam and the Caribbean, this is an opportunity to not depend on fossil fuel plastics, maintain low percentage of plastic waste, take advantage of regional resources, and bring Latam and the Caribbean to a Secondary Economic level, shifting from extractive to manufacturing economies.
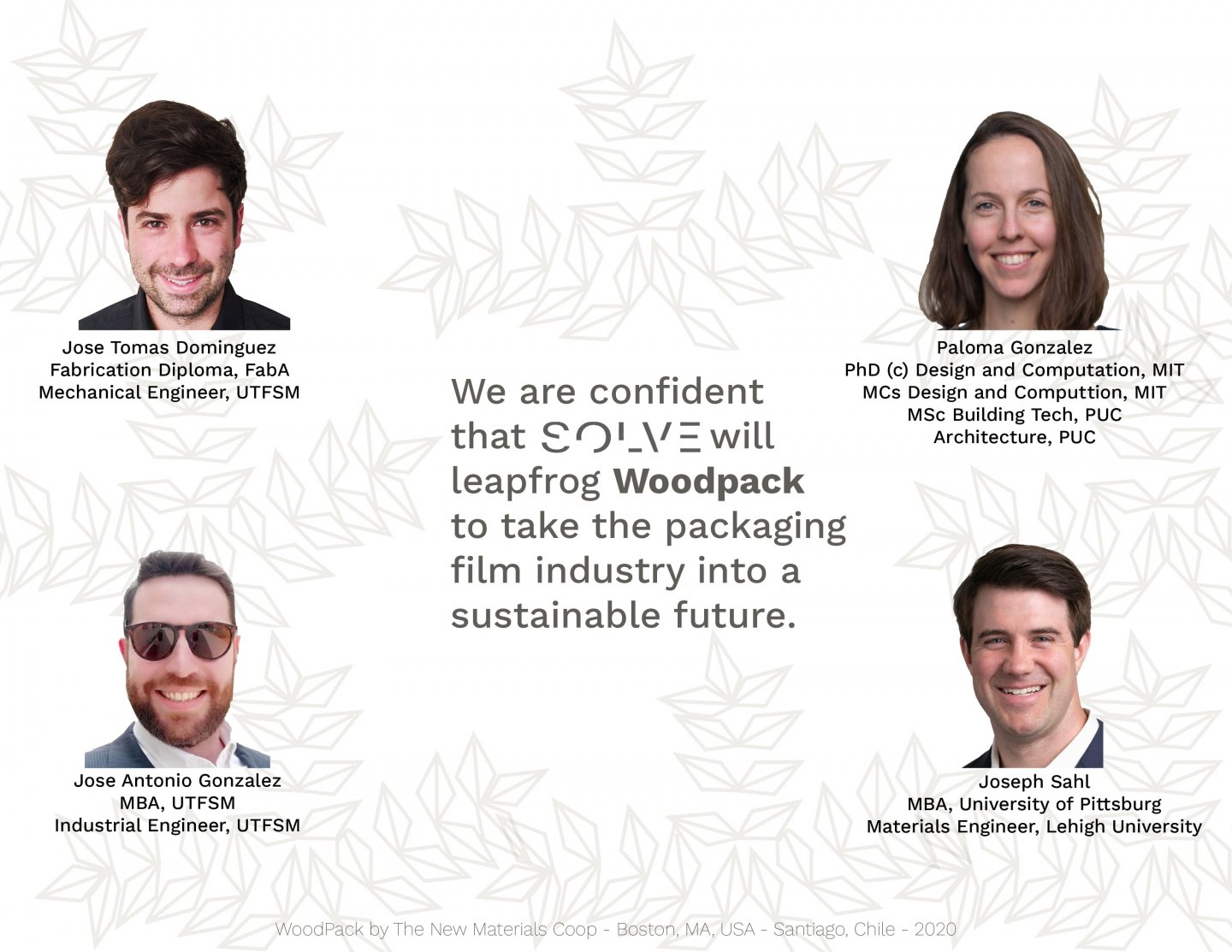
- Shift business models away from the use of plastics in packaging and transportation
- Prototype
The solution presents a completely new material based on wood pulp. Further, such new material is an innovation because of two main reasons, it is a new application of a massibly available raw material, wood pulp, and, it is a new application of existing forestry industry infrastructure for scalability.
It also has a combination of different factors that make it scalable, useful for the industry, and good for the environment:
It is biodegradable in landfill conditions, so it does not need the investment in industrial processing facilities to end the product’s life cycle.
Once it degrades it becomes organic waste to be used as fertile soil by the same forestry industries.
It fits into the forestry industry chain supply, so you don't have to build unexisting infrastructure.
We previously mentioned our aim to contribute shifting into a manufacturing economy the countries of Latam and the Caribbean. We consider this a social innovation resulting from working conditions. There is a need in the region for skilled jobs.
- Rural Residents
- Policymakers/government
- Business owners
- Other
Joseph Sahl, Material Engineer, University of Pittsburgh and MBA, Lehigh University
Jose Tomas Dominguez, Mechanical Engineer, UTFSM
Jose Antonio Gonzalez, Industrial Engineer and MBA, UTFSM
Paloma Gonzalez, R&D Developer, PhD (c), MIT and MSc Design and Computation, MIT.
Our team is a combination of different areas of knowledge ranging from material science, mechanical engineering, business, computer science to design. But it isn’t only about our technical skills, it is the fact that we have been investigating in the development of biopolymers as a side job for the last 3 years. All of this sums career expertise, experience and methodologies, on how to design and manufacture biodegradable materials, but mostly, the passion to solve world’s problems.
We are working with the support of the R&D department of Arauco, a forestry and paper company, they are supplying us with the raw materials to continue with the development of our product.
They are mentoring us on our next steps with the following strategies; showing us their industrial process that could help us develop a more professional product; and teaching us how the forestry and wood pulp market works. Enabling the integration of our product into their supply chain.
It is relevant to mention that in the future we would like to have a hybrid model that includes proprietary and open source technology.
Value proposition: A biodegradable material that perfectly fits the client’s needs.
Channels: Woodpack will use the existing selling channels that are currently used by the plastic wrap industry, enabling the integration of our product to the supply chain of the construction industry.
Key partners: We have our main raw material supplier, Arauco as an allied in the project. At present, we are working with plastic wrap sellers, receiving feedback from them about the product quality.
Key resources: The team, its knowledge in the field of biocomposites; the patentable material formula that we have been developing for over a year, replicable in other regions of the world, and fits the industry required performance.
Stakeholders: Construction packaging industry, forestry industry, Latam cities and countries that depend on the forestry industry, packaging material sellers.
Revenue Model: Our revenues will come from the direct selling of the product to construction material suppliers. Latterly we will expand to the whole packaging film market.
We like the profile of the MIT SOLVE and of the IDB. We identify with the idea of solving the problems that have an impact on people’s lives around the world. We like the idea of being social innovators, as we understand that technology can be a vehicle for change, beyond the innovation itself. As we are Chileans, we feel committed to give back to our country of origin, and to Latam and the Caribbean in general. We understand the context of our people, and we have a clear perspective on what methods are specifically applicable to our communities in Latam and the Caribbean.
We are deeply interested in being part of the IDB incubator. We think that it is the best fit for us to develop our business. The holistic approach of our solution includes an environmental, technological, and social innovation approach that is specific to the Latam and the Caribbean context and its sustainable development in coming years.
- Other
- Business Model
- Funding and revenue model
- Media and speaking opportunities
We are looking to partner with institutions as IDB that are looking to shift the L+C economies to more complex models, we feel our product fits the objective of IDB into developing industries in L+C.
We are also looking to partner with clients, packaging sellers, to push the necessities from the clients toward our company in order to develop a product that fits perfectly the markets needs.
In the spirit of circular economy we would like to partner with farmers, nursery garden or potting soil producers so they can make soil from our waste, finish the life cycle of the product.
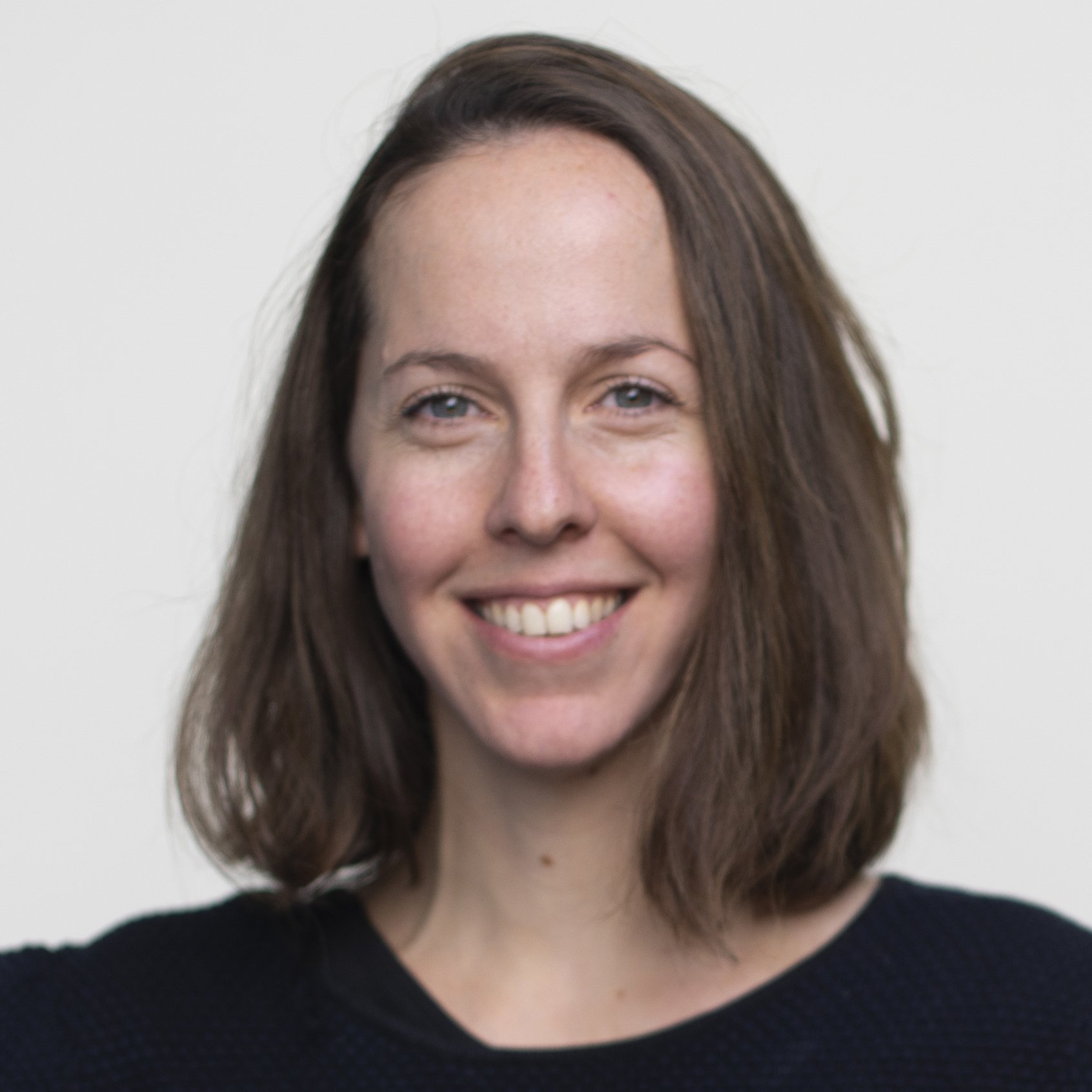