We convert wastewater to biodegradable plastic.
Earth’s growing population has resulted massive amounts of food processing and municipal wastewater and that must be treated to avoid environmental harm. Plastics waste is accumulating in landfills and the environment. PHA Global’s technology uses bacteria to solve the wastewater and plastic waste problem. Our microbes harness organic wastewater and convert it into renewable, biodegradable plastic.
Wastewater
Wastewater treatment is a costly byproduct of commercial activity. Agro-industrial waste streams represent outsized waste treatment problems compared to the communities where they exist. Frequently, these communities are located in environmentally-sensitive areas. Using palm oil as a case study, Latin America and the Caribbean produce approximately 4.5 million metric tons (MT) of palm oil each year. It is estimated that 2.5 tons of palm oil mill effluent (POME) is produced for each metric ton of crude palm oil, which results in more than 11 million MT of POME. POME is a high-strength acidic wastewater that requires a high degree of treatment to avoid environmental harm.
Plastic Waste
More than 380 million metric tons of plastic are produced each year. Less than 10% of plastic is recycled. The rest is incinerated, landfilled, or pollutes the environment. Renewable, biodegradable plastics are an attractive alternative to petroleum-based plastic but their high cost of production has limited their ability to enter the market.
- Waste generators want an affordable water treatment technology. We are reaching out to wastewater generators to understand their needs such as flow rate, treatment requirements, and operational schedule.
- Regulatory agencies manage water treatment standards and will be needed to accept our technology as a viable treatment method.
- Plastic and chemical manufacturers are looking for environmentally friendly, cost-effective alternatives to petroleum-based plastics to differentiate themselves from their competitors. We will send our offtake partners samples of our bioplastic for product development.
Our proprietary technology uses microbes to convert organic wastewater into polyhydroxyalkanoates (PHAs), a family of biodegradable polyesters. PHAs are biodegradable plastics with commercially attractive material properties such as resistance to boiling water, UV stability, and good barrier performance.
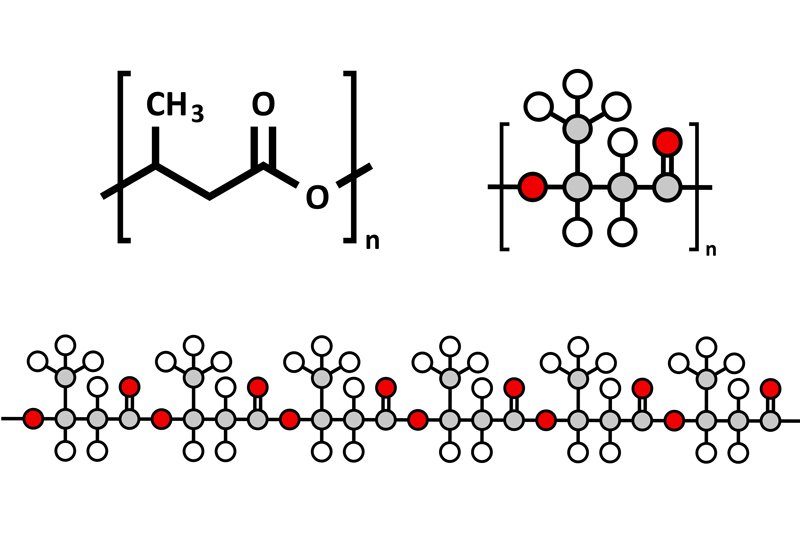
How our process works:
- Wastewater is taken from the source and fed to an acidogenic digester where complex organic compounds are broken down into a fatty acid feedstock over the course of several hours.
- The fatty acid feedstock is fed to an aerated bioreactor where our microbes convert the fatty acids into polyhydroxyalkanoate (PHA) bioplastic. The microbes store the bioplastic within their cells.
- A crude mixture containing microbes and bioplastic is separated from the water stream. The water stream undergoes final treatment to meet regulatory requirements before discharge.
- The crude mixture is processed into refined bioplastic based on its end use.
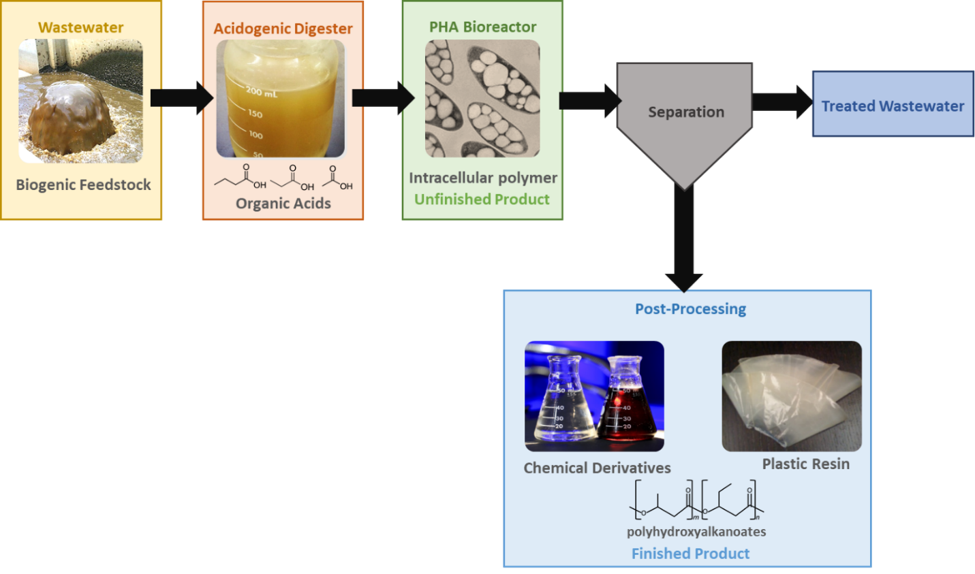
- Shift business models away from the use of plastics in packaging and transportation
- Enable the public sector, especially municipalities, to pilot and implement new and innovative systems in their waste management
- Prototype
Our commercial innovation is our dual-value proposition:
- Wastewater Treatment: our process meets water treatment standards in a small footprint without producing methane.
- Bioplastic Production: we capture waste carbon as bioplastic, a high-value product. Our waste feedstock allows us to produce bioplastic at a lifecycle and cost advantage compared with existing production techniques that use sugars or food oils as a feedstock.
Our technological innovations:
- A library of more than 70 species of plastic-producing microbes from the natural environment that have been selected based on yield, growth rate, and resistance to process upset.
- Optimization of the operating conditions for bioplastic production
- Extraction technology to refine bioplastic from crude mixture
We have tested our process on multiple feedstocks in the lab, including municipal waste, food waste, ethanol byproducts, and other feedstocks.
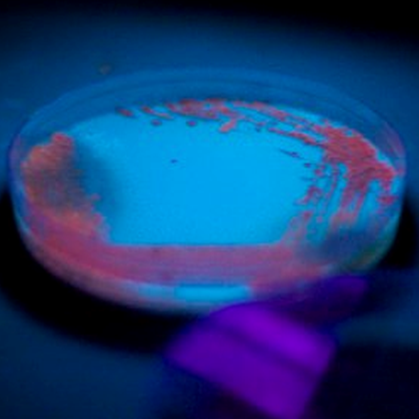
Activity: We deploy an innovative technology captures the carbon in organic wastewater and converts it into biodegradable plastic.
Outputs:
- Bioplastic is produced at a cost-competitive level with petroleum-based plastic
- Solution demonstrates the ability to meet water treatment and methane reduction regulatory standards
- Pilot demonstration validates economic model
Short-term Outcomes:
- Wastewater users meet water treatment requirements as a cash-flow
- Bioplastic samples are sent to offtake partners for application and market validation
- Early-stage commercial applications validated and market entry
- Commercial-scale modular plant design performed with global engineering design and manufacture partner
Long-term Outcomes:
- Renewable, biodegradable polymers replace conventional petroleum-based plastics in most applications
- Organic waste is increasingly viewed as a resource. Collection systems are developed/improved to shift organics from lifecycle dead-ends to biomaterial production facilities
- Additional feedstocks are tested and accessed by upcycling technologies.
- Agro-industrial waste facilities shift their model from crude resource extraction to full-cycle biorefineries
- Rural Residents
- Urban Residents
- Very Poor
- Low-Income
- Policymakers/government
- Business owners
- United States
- Malaysia
- United States
- Malaysia
We plan on constructing our first commercial scale plant within the next three years. We are targeting large high-impact wastewater generators and are investigating palm oil mill effluent (POME) as a feedstock for our process. Assuming atypical POME wastewater treatment facility as our first customer:
- Water Treatment: Our first plant will treat 260 liters of POME per minute, about 5 million liters of POME per year.
- Methane Reduction: Methane is a greenhouse gas 30 times as potent as carbon dioxide. A typical palm oil wastewater facility is estimated to produce 3,288 metric tons of methane each year, equating to 11,804 metric tons of carbon dioxide. Our solution converts the organic carbon in wastewater into biomass, bioplastic, and carbon dioxide. We will produce only a fraction of the GHG equivalents of existing treatment systems.
- Bioplastic production: Our first plant will produce over 1,000 MT of PHA bioplastic per year.
Our commercial scale plants will be of modular design so they can be rapidly constructed and deployed. We plan on second commercial facility with be commissioned within two years of operating our first plant with subsequent plants constructed quickly thereafter.
There are over 1,200 palm oil mills in Malaysia and Indonesia alone. In addition to Southeast Asia, oil palm is extensively cultivated in Africa as well as South and Central America.
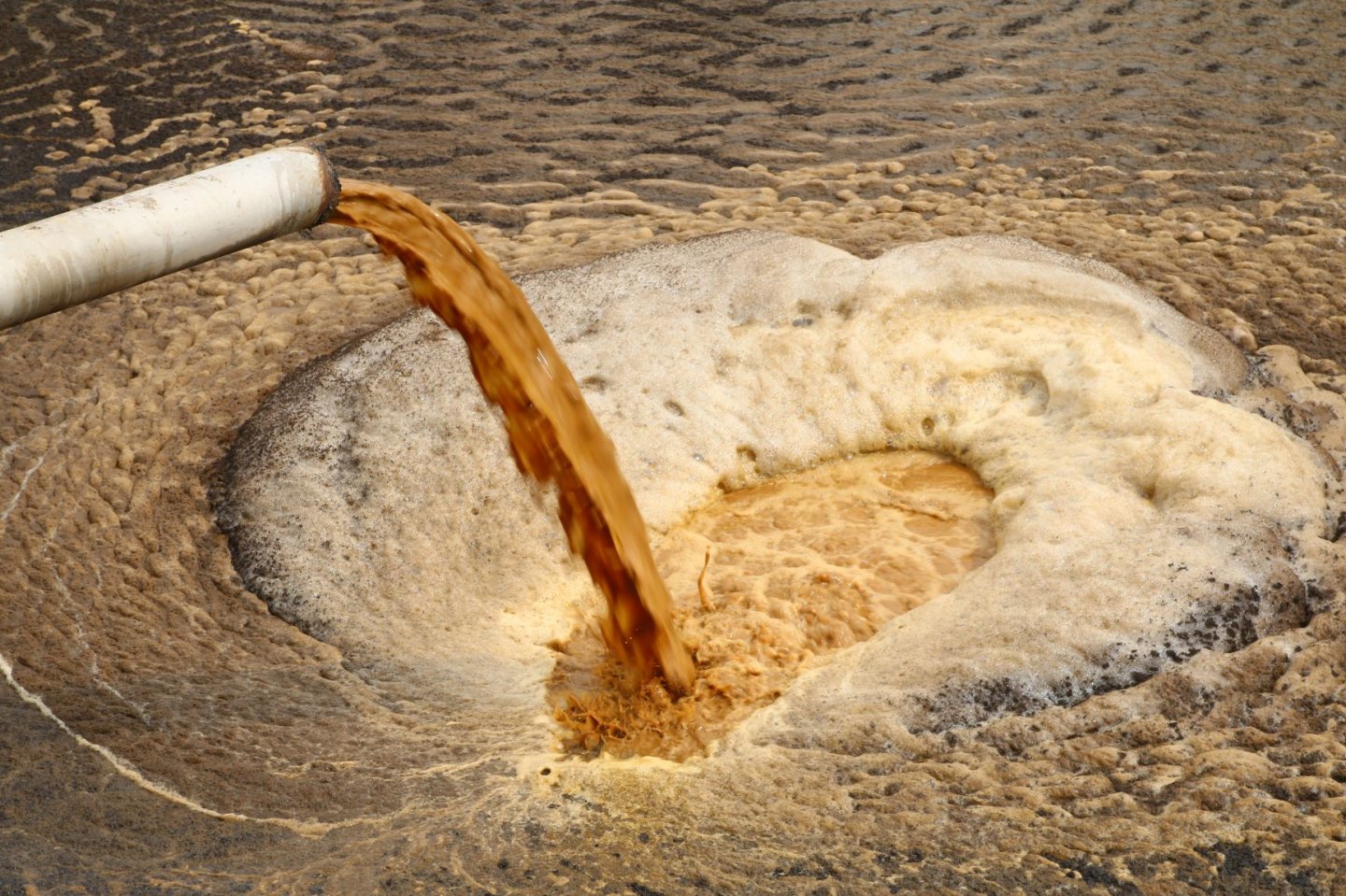
Environmental: we will measure our environmental impact by quantifying the methane mitigated and water treated.
Economic: our economic impact will be directly measured through our sales and through demand for commercial bioplastic.
Social: we hope our social impact will be measurable as a shift away from conventional plastics to renewable, biodegradable plastics. We also hope that adopting our technology will further encourage industry to adopt other technologies that fit with the circular economy.
Our major milestone is to deploy a pilot-scale demonstration plant that will continuously treat wastewater and produce bioplastic on-site at a wastewater generator.
- 2020:
- Fundraise at the Series A level to support demonstration project.
- Complete detailed design and fabrication of demonstration plant.
- On-site installation and commissioning of pilot plant.
- Transfer bioplastic samples produced from demonstration plant to offtake partners.
- 2021:
- Conclude pilot demonstration.
- Identify & engage first commercial-scale waste partner.
- Finance of first commercial scale plant.
- Official acceptance by regulatory agencies: water treatment, methane reduction, sustainability criteria.
- Front-end engineering of commercial-scale plant modules.
- Validation of techno-economic model for commercial-scale operation.
- 2022:
- Finalize design and commercial-scale plant modules.
- Construct of first commercial-scale plant modules.
- Transfer demonstration plant to new waste feedstock.
- Operate commercial-scale plant.
- First sale of commercial product. Validation of commercial revenue and payback.
- Product research & development.
- 2023:
- Construction and installation of second commercial-scale plant.
- Expansion of bioplastic extraction facilities.
- 2024 onward: Construction and installation of additional commercial plants.
Within the next five years, our major goals are to install our first commercial scale plant, expand product applications, and begin pilot demonstrations on new feedstocks/geographic areas. We will be profitable after our first commercial scale plant.
- Regulatory acceptance: We will need regulatory agency acceptance as an approved waste treatment method. We also want any required certifications where our technology is being used for sustainability or environmental tax credits. Acceptance testing can be a time
- Technology scale up and field operation: Although we have a solid understanding of our technology, there are inevitable technical challenges associated with scale up and field operation of a new process.
- Operation in a remote area: Many of feedstocks that are advantageous for our technology are in geographically remote locations.
- Product & market development: The market for commercial bioplastic already exists and is growing, but we will have to identify and secure the most suitable market segment based on our material properties.
1-year barriers:
- Regulatory acceptance: We are building relationships with regulatory agencies to familiarize them with our technology. We will involve them in the demonstration project to ensure it incorporates any acceptance testing they require.
- Technology scale up and field operation: Our pilot plant will incorporate remote monitoring & control to address unexpected problems. We are partnering with global wastewater engineering firms for scale-up.
- Operation in a remote area: The pilot plant will be designed as a mobile, containerized skid. Skidded construction will allow for acceptance testing and early troubleshooting at the manufacturer’s facility.
- Product market & development: Product samples from our pilot plant will be sent to our offtake partners for testing and product validation.
- Product market & development: The commercial PHA market is rapidly expanding and unlikely to become saturated. We will be able to take advantage of the expanding market as fast followers and develop our own applications.
5-year barriers:
- Regulatory acceptance: Once the first pilot demonstration is complete, we will keep the pilot plant active. A new pilot demonstration will be performed on a new feedstock or to demonstrate the pilot plant to a new set of regulatory agencies (such as agencies in a new country).
- Operation in a remote area: Commercial scale plants will be constructed as modules. Modules will be manufactured off-site and transported to the customer to minimize on-site installation work. Modular construction will address a wide range of customer sizes by adding additional modules and accelerate commercialization.
- I am planning to expand my solution to Latin America and the Caribbean
Our technology has been tested on multiple feedstocks. Agricultural exports are a major part of Latin America and Caribbean economies and there are a wide variety of suitable agro-industrial waste feedstocks that we could process.
Using palm oil as a case study, Latin America and the Caribbean produce approximately 4.5 million metric tons (MT) of palm oil each year. It is estimated that 2.5 tons of palm oil mill effluent (POME) is produced for each metric ton of crude palm oil, which results in more than 11 million MT of POME.
PHA Global is a spin out of Origin Materials, Inc. We currently have two full-time staff members dedicated to this project, but as a spin out we have access to the network and resources of a much larger company. We are poised to make additional hires are we complete more financing.
We have technical expertise in biology, wastewater treatment, chemistry, and technology scale-up. As innovators, we and our parent company have start-up experience and the ability to bring an new process to market.
We have had detailed talks with global engineering firms about our proposed pilot and commercial scale plants. We have potential off-take partners, who has done preliminary testing of our product. We have had discussions with Malaysian government agencies and prospective Malaysian business partners.
We will generate revenue through licensing fees and sale of bioplastic resin.
We will collect fees by licensing our technology to directly to wastewater customers or as part of a technology package provided by an engineering partner. As part of the license agreement, we will establish contracts to purchase crude bioplastic from our licensees. We will refine the crude bioplastic at a centralized processing facility.
We will sell refined bioplastic to our offtake partners. Market information on PHA price is limited, but studies on PHA economics have assumed a price of $6 USD/kg while some PHA manufacturing prices as low as $2 to $3 USD/kg, on par with petroleum plastics. Price is largely dependent on application and degree of polymer refinement.
In the long term, we will expand our focus into accessing new feedstocks for production, extraction technology (refining crude product), and novel product applications which will maintain our competitive advantage.
- Pilot demonstration plant (Series A, $5M)
- 10 kg PHA production per day sent to offtake partners for product validation
- Demonstrate wastewater treatment for regulatory partners
- Expansion of R&D operations
- First commercial plant (purchased by end user, or project/debt finance)
- Profitable once operating
- >1000 MTPY PHA production
- Follow up commercial plants (purchased by end user through licensing agreement).
- Construction of bioplastic extraction facility
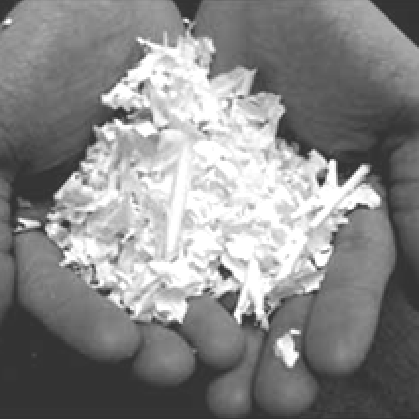
We understand the importance of having connections with regulatory agencies and a strong local knowledge to tackle the logistical challenges associated with operating a plant overseas. We are reaching out to wastewater generators in South and Central America. We think Solve could help us complete our network there.
- Technology
- Distribution
- Funding and revenue model
In addition to the Latin American partners mentioned above, we are interested in
- Wastewater generators: particularly high-strength wastewater generators that operate year-round.
- Research institutions in Latin America: we want to collaborate with local researchers
On the applications side, we are looking for:
- 3D printing: PHA/PLA blends are already available for 3D printers! We would be interested in having someone test our polymer
- Natural fiber reinforced composites: are an area of academic study for PHA, we would be interested in finding a partner to explore commercialization
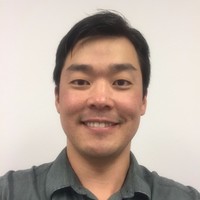